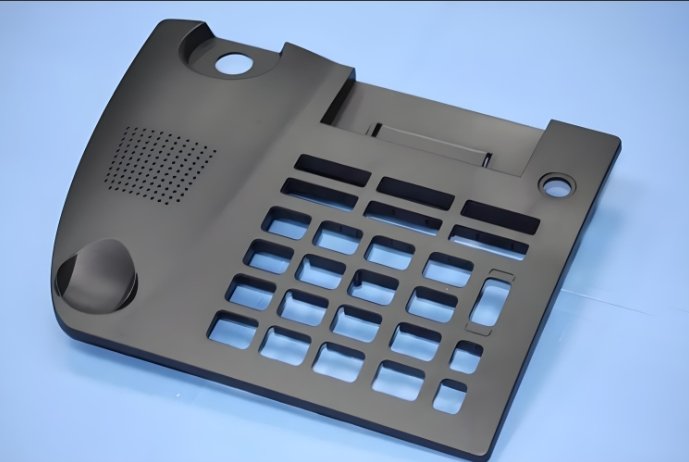
In the world of housing injection molding, precision is everything. Tight tolerances are not just a luxury—they are a necessity. Whether it’s for electronic enclosures, automotive components, or consumer devices, the parts must fit perfectly. However, maintaining those tolerances isn’t always easy. Even small errors can lead to product failures, assembly problems, and costly rework.
This is where a skilled mold maker becomes critical. Tolerance issues are often rooted in both design and tooling. Solving them requires careful planning, smart processing, and a deep understanding of material behavior. In this article, we will explore why tolerance problems occur and how to fix them for good.
Our focus is on improving accuracy in housing injection molding, with real solutions from the mold room to the molding machine.
What Are Tolerance Issues in Housing Molding?
Tolerance refers to the allowable limit of variation in a dimension. For example, a housing may need a snap-fit slot with a tolerance of ±0.1 mm. If the molded part is outside this range, the fit may be too loose or too tight.
Tolerance issues in housing injection molding can include:
- Warped or twisted parts
- Gaps in snap-fits or joints
- Tight assemblies that won’t close
- Deformed mating features
- Dimensional drift from one batch to another
To solve these problems, both the mold maker and process team must understand how plastic behaves during and after injection.
Why Tolerances Are Hard to Control in Plastic Parts
Unlike metal machining, plastic molding deals with a material that shrinks, flows, and warps in unpredictable ways. Here are the major challenges in housing injection molding:
1. Shrinkage Variability
All plastics shrink as they cool. The amount depends on:
- Material type
- Mold temperature
- Cooling rate
- Wall thickness
If the shrinkage is not uniform, parts may come out too big or too small in different areas.
2. Tool Wear
Over time, molds wear out. Edges may soften, parting lines shift, or inserts loosen. A quality mold maker monitors this closely. Poor maintenance leads to shifting dimensions and tolerance failures.
3. Inconsistent Processing
Fluctuations in processing parameters can change part dimensions:
- Temperature variations
- Inconsistent packing pressure
- Improper cooling times
Even a 5°C difference can result in measurable tolerance errors in housing injection molding.
4. Poor Mold Design
If the mold is not designed with proper tolerancing in mind, parts will not meet spec. The mold maker must factor in:
- Shrinkage compensation
- Cooling line layout
- Ejection force balance
Failing to do so causes warping, sink marks, and tolerance drift.
How a Skilled Mold Maker Solves Tolerance Problems
Step 1: Analyze the Design
Before cutting any steel, the mold maker must evaluate the 3D model.
- Are tolerances realistic for injection molding?
- Are there unnecessary tight fits?
- Can any features be redesigned to allow more tolerance?
Design simplification is often the first step in solving tolerance issues.
Step 2: Choose the Right Material
Different plastics behave differently. A mold maker must match material to part requirements.
- For high-precision parts: Use low-shrinkage materials like ABS or PC
- For flexible parts: Use PP or TPE, but expect more variation
- For dimensional stability: Consider filled resins (glass-filled, mineral-filled)
Each choice affects the final tolerance in housing injection molding.
Step 3: Design with Tolerance Compensation
A seasoned mold maker builds shrinkage and warpage into the mold layout.
- Oversize or undersize features by calculated amounts
- Adjust cavity shape to counter warp
- Use precision machining on inserts for critical dimensions
This proactive approach helps keep parts in spec after cooling.
Step 4: Optimize the Cooling System
Uneven cooling causes uneven shrinkage. This leads to warped or off-size parts.
- Use symmetrical cooling channels
- Add baffles or bubblers near hot spots
- Use conformal cooling if possible
In housing injection molding, even wall cooling is essential for accurate housings.
Step 5: Control the Injection Molding Process
The machine operator must monitor and fine-tune the process. Key parameters include:
- Injection pressure and speed
- Hold pressure and time
- Mold and melt temperature
- Cooling time
Data-driven control ensures consistent output. Many mold makers recommend using sensors in the mold to measure cavity pressure and improve repeatability.
In-Machine Adjustments for Dimensional Accuracy
Sometimes, the mold is good, but the part is still out of spec. Try these quick fixes:
1. Adjust Hold Pressure
Increase hold pressure slightly to reduce shrinkage in thick areas.
2. Modify Cooling Time
Longer cooling reduces part distortion. This helps improve tolerance in critical areas.
3. Balance Filling
If one side fills faster, it may shrink differently. Use sequential valve gates or modify runner size to improve balance.
These steps help achieve better tolerance in live production, especially for tight housing injection molding jobs.
Measurement and Quality Checks
You can’t fix what you can’t measure. Accurate measurement is vital.
- Use CMM (Coordinate Measuring Machine) for critical dimensions
- Compare actual parts to CAD models
- Use SPC (Statistical Process Control) to track dimensional trends
A good mold maker will provide detailed inspection reports during T1 and production runs.
Long-Term Strategies for Better Tolerances
To build a tolerance-friendly production system:
- Choose the right mold maker with experience in tight-tolerance housings
- Use mold flow simulation before tooling begins
- Stick to consistent machine settings and material lots
- Monitor tool wear and schedule preventive maintenance
Housing injection molding demands a high level of control. Investing in these areas pays off in fewer rejects and happier customers.
Real-World Example: Fixing a Tolerance Issue
A client came to us with a USB hub housing that would not snap together correctly. Measurements showed inconsistent wall dimensions and warped clips.
We worked with our mold maker to:
- Increase cooling in clip areas
- Change the resin from standard ABS to glass-filled ABS
- Adjust the mold cavity to allow more clearance
The result? Perfect snap fits, zero flash, and a 50% drop in rejections.
Conclusion: Tolerances Are Manageable
Tolerance issues in housing injection molding are frustrating—but they’re not impossible to fix. The key is to treat tolerances as a full-system challenge. It’s not just about the mold. It’s about the design, material, machine, and process.
A skilled mold maker plays a central role in controlling tolerances. From the first CAD file to the final molded part, every step must align to keep dimensions in check.
Key tips to remember:
- Choose materials wisely
- Design for plastic behavior
- Use flow simulation
- Build molds with shrinkage in mind
- Monitor and stabilize processing
With this complete approach, you’ll solve tolerance problems and gain long-term success in housing injection molding.