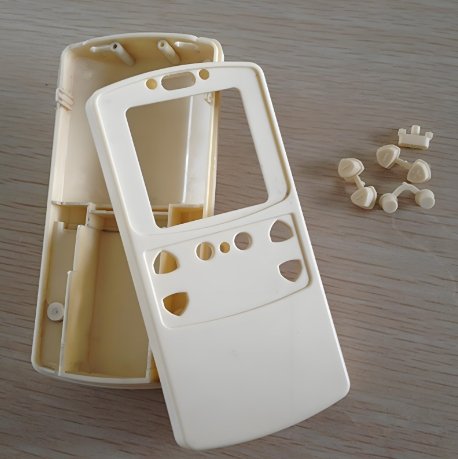
Engineering plastics are advanced materials known for their high strength, thermal resistance, and durability. These materials are ideal for technical components used in automotive, electrical, industrial, and consumer applications. However, molding them requires exceptional skill, the right equipment, and precise tooling.
A trusted Injection Molding Company with an experienced Mold Maker can help you harness the full potential of engineering plastics, delivering complex and high-performance parts at scale.
This article explores why you need a professional partner for engineering plastic projects, what to look for in a Mold Maker, and how a specialized Injection Molding Company guarantees quality and reliability.
What Are Engineering Plastics?
Engineering plastics are a class of thermoplastics that offer superior mechanical and thermal properties compared to commodity plastics like PP or PE. These materials include:
- ABS (Acrylonitrile Butadiene Styrene)
- PA (Nylon)
- PBT (Polybutylene Terephthalate)
- PC (Polycarbonate)
- PPS (Polyphenylene Sulfide)
- PEEK (Polyether ether ketone)
- Acetal (POM)
They are used when strength, impact resistance, heat stability, and chemical resistance are critical.
Why Choose an Injection Molding Company for Engineering Plastics?
Working with engineering plastics is far more complex than with standard resins. Their processing windows are tighter, and they often require higher temperatures and pressures. An experienced Injection Molding Company provides:
1. Specialized Equipment
These materials need advanced machines with accurate temperature control and high-pressure injection capability. A professional Injection Molding Company invests in such equipment to ensure precise molding of engineering plastics.
2. Advanced Processing Knowledge
Different engineering plastics behave differently. Some absorb moisture (like Nylon), while others are brittle if not processed correctly. A skilled Injection Molding Company understands each resin’s behavior and optimizes processing parameters accordingly.
3. Tooling Precision from a Skilled Mold Maker
Engineering plastics often demand tighter tolerances and cleaner surface finishes. A professional Mold Maker creates molds with exact dimensions, excellent cooling channels, and durable materials to handle high molding temperatures.
The Role of the Mold Maker in Engineering Plastics
Tooling is the heart of any molding project. For engineering plastics, this is especially true. A Mold Maker must consider:
- Thermal expansion rates of the plastic
- Shrinkage behavior
- Tool steel selection for high wear resistance
- Gate and runner design
- Cooling system design
With these considerations, a qualified Mold Maker ensures the mold performs efficiently across long production runs while maintaining part quality.
Applications of Engineering Plastic Molding
When you work with a reliable Injection Molding Company, you can produce engineering plastic parts for demanding industries such as:
Automotive
Gears, connectors, brackets, engine components, housings.
Electrical & Electronics
Switch housings, connectors, insulators, circuit protection.
Industrial
Bearings, bushings, levers, pump parts, high-wear components.
Medical
Durable instrument housings, device components, surgical tools.
Consumer
Power tool casings, sports gear, appliance parts.
Each application demands consistent performance, dimensional accuracy, and material strength—all of which depend on the quality of the Mold Maker and the Injection Molding Company.
Challenges in Engineering Plastic Molding (and Solutions)
Challenge | Solution by a Reliable Injection Molding Company |
---|---|
High shrinkage | Tool compensation through precise Mold Maker design |
Warping or internal stress | Controlled cooling and mold flow balance |
Flash and burrs | Tight tooling tolerances and optimized clamp force |
Surface defects | Proper mold polishing and advanced gating |
Inconsistent strength | Correct temperature and moisture conditioning |
A poor setup or weak tooling can result in wasted parts and delays. That’s why a seasoned Injection Molding Company and Mold Maker team are non-negotiable.
Benefits of Partnering with a Specialized Injection Molding Company
1. Material Expertise
Get advice on selecting the right engineering plastic for your needs—based on impact strength, temperature limits, and chemical exposure.
2. In-House Mold Making
In-house tooling allows fast iterations and better control. A skilled Mold Maker ensures molds are built to perform with precision and repeatability.
3. Short Lead Times
Because the company understands engineering resins well, setup and processing are efficient.
4. Quality Control
An experienced Injection Molding Company applies rigorous inspection and testing—from first article inspection (FAI) to in-process control.
5. Design Optimization
The company helps optimize your design for manufacturability (DFM), minimizing defects and reducing material usage.
What to Look for in an Engineering Plastic Injection Molding Partner
Not all Injection Molding Companies are equipped to handle engineering plastics. Here are traits to look for:
- Proven track record in PEEK, PPS, PC, PA, and POM
- In-house Mold Maker team with high-speed CNC and EDM tools
- Tooling hardened to withstand high temperatures and abrasives
- Scientific molding practices and mold flow simulation
- Clean, temperature-controlled molding floor
- ISO certification and traceability
Choose a partner that can support you from concept to production—with technical excellence and reliable communication.
Case Example: High-Performance Nylon Component
A client needed a high-strength gear made from Nylon 6/6 with 30% glass fiber for use in a power tool. A full-service Injection Molding Company with an in-house Mold Maker delivered:
- A multi-cavity tool using H13 hardened steel
- Mold flow simulation to optimize gate placement
- Automated production with robotic part handling
- Parts that passed rigorous tensile and fatigue tests
The project showed how important it is to partner with specialists who understand both the material and the mold.
Conclusion
Engineering plastics offer incredible advantages—but only when molded by experts. Their high strength, temperature resistance, and durability come at a cost: more complex processing and tooling. That’s why you need a reliable Injection Molding Company that can manage the entire process.
With a skilled Mold Maker building high-performance tools, and advanced machinery controlling the molding process, your engineering plastic parts will meet every expectation. Whether you’re in automotive, industrial, or medical, the right partner will save you time, reduce scrap, and deliver performance.