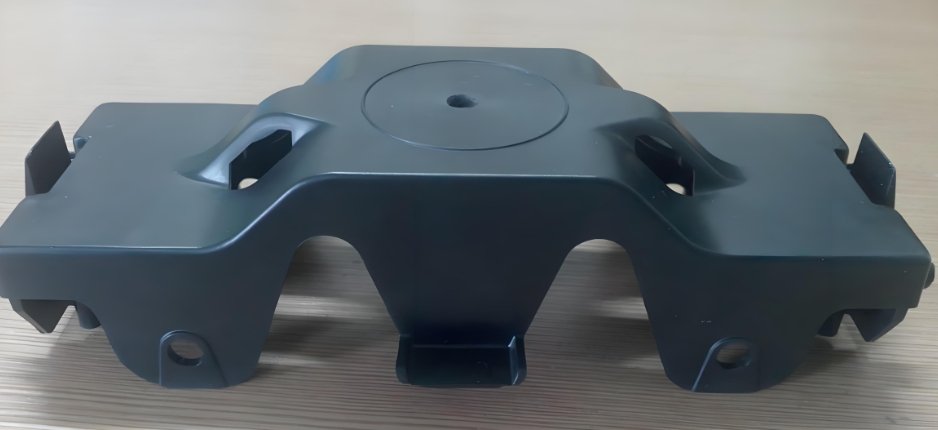
Food safety is a top priority in modern manufacturing. When producing plastic components that come into contact with food, you need absolute precision, strict cleanliness, and compliance with global safety standards. That’s where a food-grade Injection Molding Company steps in. With the support of an experienced Mold Maker, such a company can produce high-quality, hygienic plastic parts that meet both regulatory and customer expectations.
This article dives into why choosing a specialized Injection Molding Company with certified processes and a reliable Mold Maker is essential for food-grade plastic applications.
What Is Food-Grade Injection Molding?
Food-grade injection molding involves producing plastic parts that are safe for direct or indirect contact with food. These parts include containers, utensils, dispensers, caps, lids, and packaging components. A top-tier Injection Molding Company ensures that every material and process follows strict standards like FDA, EU 10/2011, or NSF certifications.
With an expert Mold Maker designing your tools, the resulting parts are not only compliant but also clean, durable, and easy to maintain in a food-safe environment.
Why Choose a Food-Grade Injection Molding Company?
1. Material Certification
A specialized Injection Molding Company works only with food-grade resins like:
- Polypropylene (PP)
- Polyethylene (PE)
- Polystyrene (PS)
- Polycarbonate (PC)
- Nylon (PA)
These materials must be free of BPA, phthalates, and other harmful additives. The Injection Molding Company sources and certifies materials to ensure compliance with international food-contact standards.
2. Cleanroom Manufacturing
Food-grade parts must be produced in a contamination-free environment. Many reputable Injection Molding Companies offer Class 7 or Class 8 cleanroom molding to eliminate dust, bacteria, and foreign particles.
3. Precision from an Expert Mold Maker
A reliable Mold Maker builds molds that are easy to clean, resist corrosion, and minimize dead zones. Polished steel surfaces and streamlined ejection systems ensure sanitary, efficient production.
Role of the Mold Maker in Food-Safe Production
The Mold Maker plays a critical role in food-grade part production. They:
- Choose stainless or corrosion-resistant mold steel
- Design smooth-flow channels to reduce contamination
- Polish mold surfaces to prevent material build-up
- Include self-draining features where needed
- Ensure molds are easy to clean and disassemble
Without a skilled Mold Maker, even the most hygienic resin can be ruined by poor tooling design. That’s why a great Injection Molding Company always partners closely with or employs expert Mold Makers.
Common Food-Grade Applications
A food-grade Injection Molding Company serves industries like:
➤ Food Packaging
Lids, trays, cups, and sealable containers require precision and safety.
➤ Beverage Industry
Caps, nozzles, dispensers, and closures must be tamper-proof and food-safe.
➤ Kitchenware
Utensils, measuring spoons, mixing containers, and handles demand heat resistance and hygiene.
➤ Commercial Food Equipment
Plastic housings, gaskets, gears, and pump parts in food processors and dispensers.
For each application, the Injection Molding Company ensures that molds built by the Mold Maker meet production goals while upholding food safety.
Quality and Regulatory Standards You Can Trust
When working with a specialized Injection Molding Company, you benefit from strict adherence to standards like:
- FDA (U.S. Food and Drug Administration)
- EU Regulation 10/2011
- NSF (National Sanitation Foundation)
- ISO 9001 and ISO 13485 (if used for food-related medical devices)
- HACCP-compliant manufacturing protocols
A qualified Injection Molding Company integrates these practices into both their molding and Mold Maker departments to ensure 100% compliance.
Features of an Ideal Food-Grade Injection Molding Company
When choosing your Injection Molding Company, make sure they offer:
✅ Full traceability of raw materials
✅ Cleanroom or hygiene-controlled production
✅ In-house Mold Maker team for fast revisions
✅ Use of food-safe lubricants and non-toxic colorants
✅ Post-molding inspection and sterilization (if required)
✅ Detailed record-keeping for audits and recalls
Partnering with the right Injection Molding Company ensures your food-grade components are not only safe but also produced cost-effectively.
Case Study: Food Dispenser Nozzle for a Beverage Brand
A client needed a tamper-proof nozzle for a drink dispenser. The original prototype failed due to contamination risk and leakage.
The chosen Injection Molding Company worked closely with their in-house Mold Maker to redesign the tool. They improved flow channels, added a snap-fit design, and used FDA-approved Polypropylene.
The new version passed NSF certification on the first try. Production scaled to 100,000 parts monthly with zero customer complaints.
Advantages of Working with a Full-Service Injection Molding Company
1. One-Stop Service
From CAD design to mold making, sampling, mass production, and packaging, everything is handled under one roof.
2. Lower Long-Term Costs
In-house Mold Maker services reduce outsourcing fees and avoid delays.
3. Fast Turnaround
Quick prototyping and sampling allow for fast approvals and production.
4. Risk Reduction
Compliance and traceability protect your brand from recalls and legal issues.
5. Custom Mold Maintenance
Your Mold Maker maintains and repairs your tooling for years of reliable use.
How to Select the Right Food-Grade Injection Molding Company
Here are key questions to ask:
- Do they have food-grade certifications?
- Are their Mold Maker teams experienced with hygienic design?
- Can they provide full material traceability?
- Do they offer cleanroom production or alternatives?
- What industries do they already serve?
A top Injection Molding Company will be transparent, experienced, and proactive in meeting your project’s needs.
Conclusion
Food-grade injection molding is not just about materials—it’s about the entire process. A trusted Injection Molding Company combines certified materials, cleanroom environments, precision molds, and rigorous inspection standards to produce parts that are both safe and reliable.
Behind every successful food-grade project is a skilled Mold Maker who designs the tooling with hygiene, durability, and manufacturability in mind.
Whether you’re producing bottle caps, food containers, or dispenser parts, choosing the right Injection Molding Company ensures compliance, quality, and peace of mind. Your reputation—and your customer’s health—depends on it.