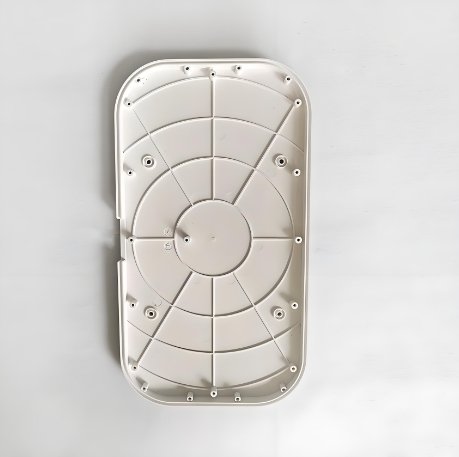
In today’s healthcare industry, there is no room for error. Medical components must be accurate, sterile, durable, and produced under strict quality controls. That’s why partnering with a specialized Injection Molding Company that offers FDA-compliant manufacturing and expert Mold Maker support is critical for your success.
From surgical tools and diagnostic devices to fluid management components and enclosures, every part requires flawless execution. This article explores what makes a truly reliable medical-grade Injection Molding Company, how an experienced Mold Maker ensures precision, and why FDA compliance is essential.
What Is Medical-Grade Injection Molding?
Medical-grade injection molding refers to the manufacturing of plastic components that meet the stringent requirements of the healthcare industry. These parts are used in applications where failure is not an option. A reputable Injection Molding Company must follow strict standards such as ISO 13485, FDA 21 CFR Part 820, and other global medical regulations.
Equally important is the Mold Maker who creates the tooling that shapes the final product. Without high-precision molds, even the best materials and machines can fail to deliver consistent results.
FDA Compliance in Injection Molding
An Injection Molding Company with FDA compliance ensures that every aspect of the production process—from material sourcing to final inspection—meets or exceeds regulatory standards.
Key FDA-related features include:
- Use of FDA-approved medical-grade resins
- Traceability of every batch of material
- Documented quality management systems
- Cleanroom molding (Class 7 or Class 8)
- Sterile packaging options
- Complete validation and IQ/OQ/PQ procedures
Every mold must also be validated. This is where the Mold Maker plays a crucial role. They design molds that are capable of producing parts within extremely tight tolerances, ensuring that each part functions as intended in medical settings.
Role of the Mold Maker in Medical Manufacturing
An experienced Mold Maker is not just a tool builder—they are the cornerstone of precision and repeatability. In a medical Injection Molding Company, the Mold Maker ensures:
- Flawless mold cavity alignment
- Clean, polished surfaces to avoid contamination
- Precision gating to prevent flash or defects
- Venting systems to eliminate trapped gases
- Long mold life with minimal maintenance
When working with a qualified Mold Maker, your tooling supports years of production with low rejection rates and consistent part quality.
Common Medical Applications
Medical-grade plastic injection molding is used in a wide range of healthcare devices and tools:
1. Diagnostic Devices
Cassettes, housings, and sample holders for rapid test kits or analyzers.
2. Drug Delivery Systems
Components for auto-injectors, inhalers, and infusion pumps.
3. Surgical Tools
Handles, grips, clips, and disposable surgical components.
4. Implant Packaging
Sterile barriers and secure containers for surgical implants.
5. IV and Fluid Management
Connectors, valves, ports, and tubing components made with FDA-compliant materials.
For each of these, the Injection Molding Company and Mold Maker must work together to ensure function, hygiene, and compliance.
Benefits of Choosing a Medical-Grade Injection Molding Company
✅ FDA-Certified Materials
Only biocompatible resins such as Polycarbonate, Polypropylene, ABS, and PEEK are used.
✅ Cleanroom Production
Injection molding in ISO Class 7 or 8 cleanrooms minimizes contamination risk.
✅ Traceable Production
Every part is traceable back to its resin lot, molding parameters, and mold design.
✅ In-House Mold Maker Capabilities
Faster iterations, easier maintenance, and lower costs when molds are built and maintained internally.
✅ Sterile Packaging Options
Many companies offer in-line or post-molding packaging to preserve sterility.
Choosing the right Injection Molding Company ensures that your product is not just high quality—but safe and regulatory-ready.
Case Study: Diagnostic Housing for a Portable Analyzer
A client needed a high-precision housing for a point-of-care diagnostic analyzer. The component required tight tolerances, resistance to chemical cleaning agents, and low particulate generation.
The selected Injection Molding Company used a medical-grade polycarbonate resin. Their in-house Mold Maker designed a two-cavity mold with polished inserts and tight cooling control. Molding occurred in a Class 8 cleanroom and included inline vision inspection.
The result? Zero contamination, 99.9% dimensional accuracy, and successful FDA submission.
How to Choose the Right Medical Injection Molding Partner
Ask These Questions:
- Are you ISO 13485 certified?
- Do you use FDA-compliant resins and processes?
- Do you have cleanroom capabilities?
- Is your Mold Maker team experienced with medical parts?
- Do you offer full validation (IQ/OQ/PQ)?
- What quality controls do you use during molding?
A professional Injection Molding Company will answer these questions transparently, with documentation to support every claim.
The Future of Medical Injection Molding
As medical devices grow smaller and more complex, the partnership between Injection Molding Company and Mold Maker becomes even more important. Micro-molding, overmolding, and multi-material applications require extreme precision and advanced tooling.
3D simulation tools, automated inspection, and data-driven production monitoring are helping Injection Molding Companies improve speed, accuracy, and traceability. Meanwhile, Mold Makers are leveraging precision machining, EDM, and laser texturing to achieve incredible detail and reliability.
Conclusion
For any medical plastic project, quality and safety are non-negotiable. A certified Injection Molding Company with FDA-compliant systems and a skilled Mold Maker can deliver exactly that.
From diagnostic devices to surgical tools, every successful part begins with expert mold design and ends with careful molding execution. The right partner ensures speed, precision, traceability—and ultimately, patient safety.
Whether you’re developing a new device or scaling production of an existing one, choosing a trusted Injection Molding Company backed by a capable Mold Maker team is your best investment in quality.