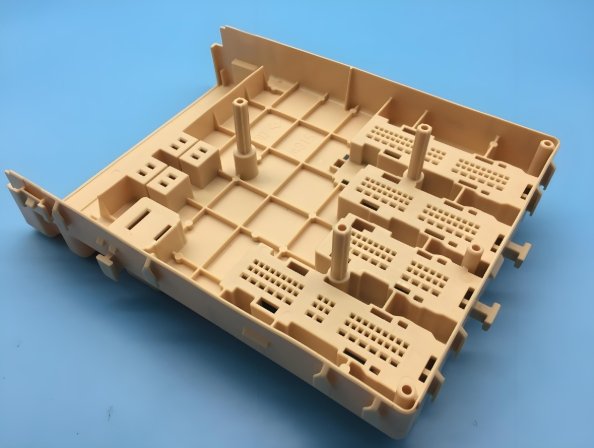
In Electronic Injection Molding, shrinkage is a common issue that can affect the quality of molded parts. Shrinkage occurs when the material cools and contracts after being injected into the mold. This can lead to dimensional inaccuracies and performance issues. To ensure high-quality electronic components, it’s important to address shrinkage effectively.
Understanding the Cause of Shrinkage
Shrinkage happens due to the cooling process. As the molten material cools down in the mold, it contracts. The rate of cooling and the material used can influence how much shrinkage occurs. Mold makers need to understand these factors to predict and control shrinkage.
Factors That Influence Shrinkage in Electronic Injection Molding
Several factors affect shrinkage during electronic injection molding:
- Material Properties: Different materials shrink at different rates. Thermoplastics, like ABS or polycarbonate, behave differently than thermosets.
- Mold Design: The shape and structure of the mold can impact how the material flows and cools, affecting shrinkage.
- Injection Pressure: High pressure can help reduce shrinkage by forcing more material into the mold.
- Cooling Time: Longer cooling times allow the material to settle properly, reducing shrinkage.
A skilled mold maker can control these variables to minimize shrinkage.
Shrinkage in Electronic Components
Electronic components are particularly sensitive to shrinkage. These components need to maintain precise dimensions to fit perfectly into devices. Even small deviations can cause malfunction. For example, connectors, housings, or insulators must align accurately in electronic assemblies. Shrinkage can cause gaps, misalignments, or stress on the components, which may lead to early failure.
How to Minimize Shrinkage in Electronic Injection Molding
There are several approaches to minimize shrinkage in electronic injection molding:
- Optimizing Mold Design: The mold should have uniform wall thickness. Thin walls cool faster than thick ones, leading to more shrinkage. Uniformity helps control this process.
- Control Cooling Rate: The cooling system in the mold must be carefully designed. It should ensure that the material cools evenly. This reduces the chances of uneven shrinkage.
- Use of High-Quality Materials: Selecting materials with low shrinkage rates can help. Many materials are designed to minimize shrinkage in injection molding processes. A mold maker can recommend the best material for each application.
- Precise Injection Pressure: Ensuring the correct injection pressure is key to controlling shrinkage. Too much pressure can lead to warping, while too little can cause underfilling and excessive shrinkage.
- Use of Injection Molding Simulation Software: Modern simulation tools can predict shrinkage and optimize mold designs. These tools model how the material will behave during cooling, giving mold makers insight into potential issues.
The Role of a Mold Maker in Shrinkage Control
A skilled mold maker plays a crucial role in minimizing shrinkage. They must design molds that distribute material evenly and cool at a controlled rate. Using advanced techniques, they can design molds that compensate for shrinkage by adjusting wall thickness and cooling systems. By selecting the right materials and applying precise techniques, a mold maker can reduce shrinkage significantly.
Challenges in Electronic Injection Molding
While shrinking is a natural part of electronic injection molding, it presents unique challenges. As electronics become more compact and complex, the parts need tighter tolerances. Meeting these requirements is difficult, especially with shrinking components. Mold makers must carefully balance cooling rates, injection pressures, and material choices to prevent shrinkage from affecting part performance.
Advanced Techniques for Shrinkage Reduction
To further improve mold quality, mold makers often turn to advanced methods. One common technique is the use of mold temperature controllers. These devices regulate the temperature within the mold to ensure consistent cooling. Another method involves incorporating gate design optimization. The gate is the point where material enters the mold. A well-designed gate allows for controlled material flow, reducing the chances of shrinkage.
Test and Quality Control
Once the mold is built, mold makers perform thorough testing. They monitor how the material shrinks as it cools. By analyzing the test results, they can adjust the mold design if necessary. Regular quality control checks are essential to maintaining consistent mold performance.
Conclusion: The Importance of Shrinkage Control in Electronic Injection Molding
In electronic injection molding, shrinkage is a critical issue. It can compromise the functionality of electronic components if not addressed properly. By understanding the causes of shrinkage and applying the right strategies, mold makers can ensure the production of high-quality, accurate electronic parts. With careful attention to mold design, material selection, and cooling systems, shrinkage can be minimized, leading to better performance and longer-lasting products.
Efficient shrinkage control in electronic injection molding requires expertise and experience. A mold maker who understands the complexities of shrinkage can greatly improve the final product’s quality. By using advanced technologies, testing, and quality control, manufacturers can produce electronic components that meet the highest standards.