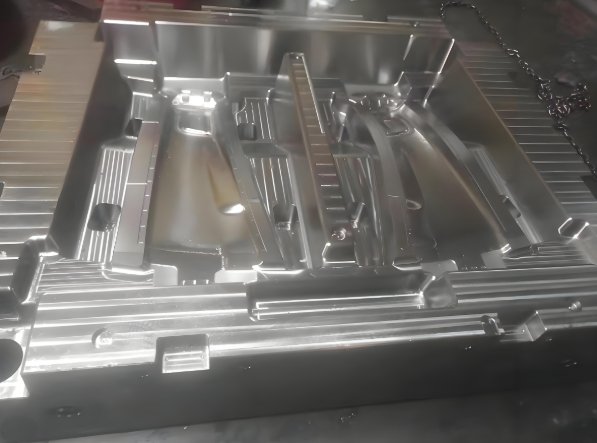
Vehicle safety is a priority for every manufacturer. Automotive Injection Molds play a key role in producing safety-critical components. Skilled Mold Makers use advanced techniques to meet these demands. These techniques ensure precision, durability, and reliability.
The Importance of Injection Molds in Automotive Safety
1. Critical Safety Components
Injection molds create airbags, seatbelt housings, and crumple zone parts. These parts must perform flawlessly in emergencies.
2. High Precision
Safety components require tight tolerances. Even slight defects can lead to failure.
3. Durability Under Stress
Molded parts endure extreme conditions. They resist impact, heat, and pressure during accidents.
Techniques for Advanced Safety Components
1. Two-Shot Molding
This technique combines two materials. It creates parts with different properties in one process. For example, rigid frames with soft cushioning for impact absorption.
2. Gas-Assisted Molding
This method reduces part weight. Lighter parts improve vehicle efficiency. It also enhances strength for better safety.
3. Overmolding
Overmolding joins multiple layers. It creates stronger and more flexible parts. This is essential for energy-absorbing components.
4. Insert Molding
Metal inserts are molded with plastic. This strengthens parts like brackets and reinforcements.
Key Automotive Safety Parts Produced
1. Airbag Housings
Injection molds create lightweight and sturdy airbag enclosures. These parts ensure rapid and reliable airbag deployment.
2. Seatbelt Components
Molded plastic parts support seatbelt mechanisms. They remain strong during high-pressure conditions.
3. Crash Absorption Panels
Energy-absorbing panels reduce collision impact. Injection molding ensures these panels meet precise standards.
4. Child Safety Seats
Plastic molds create strong yet lightweight child seats. These meet strict safety regulations.
Innovations in Safety Molding
1. Smart Molds
Sensors track mold performance. They ensure consistent quality for safety-critical parts.
2. 3D Mold Prototyping
3D printing speeds up prototype testing. It ensures safety parts meet all requirements before production.
3. High-Performance Polymers
Advanced plastics withstand higher stress. They improve the durability of safety components.
4. Automated Quality Checks
AI-driven inspections catch defects early. This prevents faulty parts from reaching vehicles.
Role of Mold Makers in Automotive Safety
1. Material Expertise
Mold Makers select the right materials. They ensure parts are strong, lightweight, and heat-resistant.
2. Precision Engineering
High-tech tools deliver perfect molds. This reduces defects in safety-critical parts.
3. Customization for Manufacturers
Every automaker has unique designs. Mold Makers adapt molds to fit specific safety needs.
4. Sustainability
Modern molds reduce waste. This supports eco-friendly production goals.
Challenges in Safety Molding
1. Strict Regulations
Safety components face tough standards. Meeting these requirements demands precision.
2. High Production Costs
Developing advanced molds requires investment. However, long-term benefits outweigh these costs.
3. Material Limitations
Not all plastics can handle extreme conditions. Finding the right material is critical.
Applications of Advanced Safety Molds
1. Passenger Safety Systems
Airbags, seatbelts, and child seats rely on injection molds. These parts protect lives in accidents.
2. Structural Integrity
Crash-absorbing panels and reinforcements improve vehicle strength. Injection molds ensure their reliability.
3. Electronic Safety
Housings for sensors and cameras safeguard electronic safety systems. These are vital for modern vehicles.
Trends in Safety Molding
1. Sustainable Materials
Recycled and biodegradable plastics are being used. This supports eco-friendly manufacturing.
2. Lightweight Components
Reducing part weight improves fuel efficiency and safety. Advanced molding techniques achieve this.
3. AI Integration
AI helps design better molds. It predicts potential flaws before production begins.
4. Collaborative Design
Mold Makers work closely with automakers. This ensures molds meet all safety and design requirements.
Future of Injection Molding for Safety
1. Enhanced Materials
New polymers will offer even better strength and flexibility.
2. Fully Automated Production
Robots will handle more tasks. This improves precision and reduces errors.
3. Custom Safety Features
Injection molds will create unique designs for personalized safety solutions.
Choosing the Right Mold Maker
1. Experience in Safety Molding
Select a Mold Maker with a proven track record. Their expertise ensures high-quality results.
2. Advanced Tools
Modern machinery delivers better molds. Choose providers with cutting-edge technology.
3. Quality Assurance
Reliable Mold Makers conduct thorough inspections. This guarantees defect-free parts.
Advanced techniques in Automotive Injection Molds are revolutionizing safety. Expert Mold Makers ensure precision and quality. Their work saves lives by producing reliable safety components.
As vehicles evolve, so will molding techniques. Innovations will lead to stronger, lighter, and more sustainable parts.
The future of automotive safety relies on the expertise of skilled Mold Makers. Their contributions drive progress in this critical field.