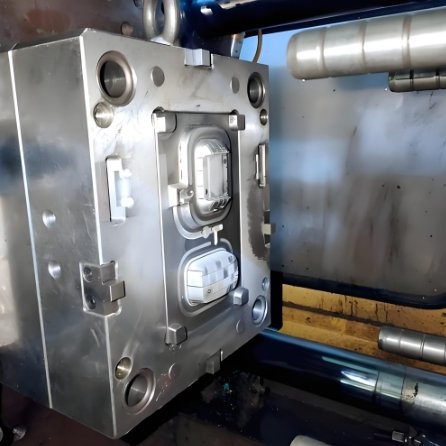
Electronic injection molding is essential in modern electronics manufacturing. It enables precise, high-volume production of components. Mold makers design and create molds that shape these parts. This process ensures consistency, durability, and cost efficiency. Advanced techniques improve accuracy and expand design possibilities.
1. What Is Advanced Electronic Injection Molding?
1.1 Understanding the Basics
Injection molding uses heated material injected into a mold. The material cools and takes the mold’s shape. This method produces strong, lightweight electronic parts.
1.2 Why Advanced Techniques Matter
As electronics become smaller, components must be more precise. Advanced electronic injection molding ensures accuracy and reliability. It also supports innovative designs.
2. The Role of Mold Makers in Advanced Injection Molding
2.1 Designing High-Precision Molds
Mold makers create molds with tight tolerances. These molds ensure consistency in electronic parts. High-quality molds reduce defects and enhance efficiency.
2.2 Selecting the Right Materials
Different materials serve various functions in electronic parts. Mold makers choose heat-resistant and conductive materials. Proper material selection ensures durability and performance.
2.3 Prototyping and Testing
Prototyping helps refine mold designs before full production. Mold makers test prototypes to ensure fit, function, and durability. This step reduces errors and saves costs.
3. Key Applications of Electronic Injection Molding
3.1 Circuit Board Housings
Injection molding creates protective housings for circuit boards. These housings shield components from damage and interference.
3.2 Connectors and Sockets
Precision-molded connectors ensure secure electrical connections. They must be durable and fit perfectly.
3.3 LED Components
LED casings require high transparency and heat resistance. Electronic injection molding meets these requirements effectively.
3.4 Switches and Buttons
Many electronic devices use injection-molded buttons. These parts must be sturdy and responsive.
4. Advanced Techniques in Electronic Injection Molding
4.1 Overmolding
Overmolding combines multiple materials in one part. This process enhances strength and functionality. It is useful for connectors and grips.
4.2 Insert Molding
Insert molding embeds metal or other components into plastic. It improves durability and electrical performance.
4.3 Micro Injection Molding
Micro molding produces extremely small parts. It is vital for compact electronic devices.
4.4 Liquid Silicone Rubber (LSR) Molding
LSR molding creates flexible, heat-resistant parts. It is useful in wearables and medical electronics.
5. Benefits of Advanced Electronic Injection Molding
5.1 High Precision
Advanced molding ensures accuracy down to microns. This precision is crucial for modern electronics.
5.2 Cost Efficiency
Injection molding lowers production costs by reducing material waste. It enables mass production at lower per-unit costs.
5.3 Design Flexibility
Innovative molding techniques allow for complex shapes and multi-material parts.
5.4 Improved Durability
Injection-molded electronic parts are resistant to heat, moisture, and wear.
6. Challenges in Advanced Injection Molding
6.1 Tight Tolerances
Meeting strict specifications requires highly skilled mold makers. Even minor deviations can cause failures.
6.2 Material Selection
Not all materials work for all applications. Choosing the right material is critical.
6.3 Tooling Costs
High-quality molds require a significant investment. However, they save costs in large-scale production.
7. Innovations in Electronic Injection Molding
7.1 Smart Molds
Sensors in molds monitor temperature and pressure in real time. This improves consistency and reduces defects.
7.2 AI in Quality Control
AI detects defects and optimizes production. This ensures higher efficiency and less waste.
7.3 Sustainable Manufacturing
New materials and recycling techniques reduce environmental impact.
8. The Future of Electronic Injection Molding
8.1 Miniaturization
Devices are getting smaller. Electronic injection molding will continue to support compact, high-performance parts.
8.2 Automation and Robotics
Robots will streamline molding processes, improving speed and accuracy.
8.3 Integration with 3D Printing
3D printing will help develop and test molds faster, reducing lead times.
Advanced electronic injection molding plays a crucial role in manufacturing. Mold makers ensure precision, durability, and cost efficiency. With evolving technologies, injection molding continues to shape the future of electronics.