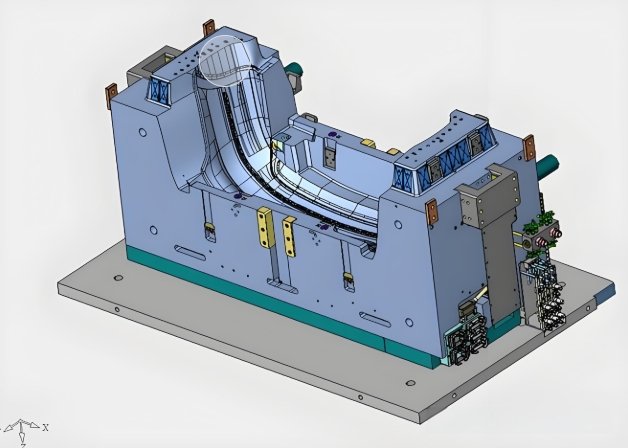
Plastic parts are crucial in cars. Automotive injection molds create these parts. A skilled mold maker ensures accuracy and durability. Advanced mold technology improves quality and efficiency.
Importance of Precision in Automotive Molds
1. High Safety Standards
Car parts must meet strict safety rules. Automotive injection molds ensure precision. A mold maker avoids defects.
2. Lightweight Components
Lighter cars improve fuel efficiency. Automotive injection molds produce strong yet light parts. A mold maker optimizes weight reduction.
3. Consistency in Mass Production
Each part must match perfectly. Automotive injection molds guarantee uniformity. A mold maker prevents variations.
Common Automotive Plastic Components
1. Dashboard Panels
Dashboards need durability. Automotive injection molds shape heat-resistant panels. A mold maker ensures smooth finishes.
2. Bumper Covers
Bumpers absorb impact. Automotive injection molds create strong covers. A mold maker chooses flexible materials.
3. Door Handles and Panels
Interior and exterior handles need precision. Automotive injection molds shape ergonomic designs. A mold maker ensures perfect fitting.
4. Air Vents and Grilles
Proper airflow needs precise molding. Automotive injection molds shape intricate vent designs. A mold maker ensures consistency.
5. Lighting Housings
Lights need protective casings. Automotive injection molds form impact-resistant housings. A mold maker ensures transparency and strength.
Types of Injection Molds for Automotive Plastics
1. Multi-Cavity Molds
More parts in less time. Automotive injection molds with multiple cavities boost efficiency. A mold maker ensures uniform results.
2. Hot Runner Molds
No wasted plastic. Automotive injection molds with hot runners improve material flow. A mold maker optimizes heating.
3. Gas-Assisted Injection Molding
Hollow parts need this technique. Automotive injection molds with gas assistance reduce weight. A mold maker controls airflow.
4. Overmolding for Multi-Layer Parts
Some parts need two materials. Automotive injection molds with overmolding combine them. A mold maker ensures seamless bonding.
Advanced Mold Materials for Automotive Plastics
1. High-Performance Polymers
Plastics must withstand heat and impact. Automotive injection molds use PEEK and PPS. A mold maker selects the best options.
2. Reinforced Nylon for Strength
Stronger than regular plastics. Automotive injection molds use nylon for durability. A mold maker ensures high resistance.
3. Polycarbonate for Transparent Parts
Clear parts need special plastics. Automotive injection molds use polycarbonate for lenses. A mold maker ensures clarity.
4. ABS for Impact Resistance
Bumpers and dashboards need toughness. Automotive injection molds use ABS. A mold maker enhances shock absorption.
Precision Techniques in Mold Manufacturing
1. CNC Machining for Accuracy
Machines cut with precision. Automotive injection molds need exact dimensions. A mold maker programs perfect cuts.
2. EDM for Complex Shapes
Some parts need fine details. Automotive injection molds use EDM for intricate designs. A mold maker ensures accuracy.
3. Polishing for Surface Perfection
Smooth surfaces improve function. Automotive injection molds get polished finishes. A mold maker removes defects.
4. Cooling Channels for Fast Cycles
Faster cooling means quicker production. Automotive injection molds use advanced cooling channels. A mold maker optimizes heat dissipation.
Automation in Automotive Injection Molding
1. Robotic Mold Handling
Machines reduce human errors. Automotive injection molds work with robotic systems. A mold maker ensures smooth operations.
2. AI-Powered Quality Control
AI finds tiny defects. Automotive injection molds use smart sensors for inspection. A mold maker ensures high precision.
3. Automated Injection Molding Machines
Less manual work speeds up production. Automotive injection molds run on automated machines. A mold maker fine-tunes settings.
Sustainability in Automotive Plastic Molding
1. Recycled Plastic Materials
Less waste means a greener process. Automotive injection molds now use recycled plastics. A mold maker reduces environmental impact.
2. Energy-Efficient Molding Machines
New machines save energy. Automotive injection molds work with eco-friendly equipment. A mold maker optimizes efficiency.
3. Reduced Scrap and Waste
Better designs mean fewer defects. Automotive injection molds minimize plastic waste. A mold maker ensures lean production.
4. Bio-Based Plastics for Future Cars
Sustainable materials matter. Automotive injection molds now explore bio-plastics. A mold maker adapts to new trends.
Challenges in Automotive Plastic Mold Manufacturing
1. Heat Resistance in Engine Parts
Car parts face high temperatures. Automotive injection molds must handle extreme heat. A mold maker selects heat-proof materials.
2. Complex Designs for Aerodynamics
Smoother shapes improve efficiency. Automotive injection molds must mold intricate designs. A mold maker ensures perfect shaping.
3. Cost Reduction in Production
Less cost, more profit. Automotive injection molds need optimized production. A mold maker balances cost and quality.
4. Faster Cycle Times for Mass Production
Speed matters in car manufacturing. Automotive injection molds need quick cooling and fast cycles. A mold maker refines every detail.
Future Trends in Automotive Plastic Molding
1. 3D Printing for Prototypes
Faster design testing. Automotive injection molds use 3D-printed prototypes. A mold maker validates designs quickly.
2. AI-Optimized Mold Designs
Smart technology enhances molding. Automotive injection molds now use AI simulations. A mold maker improves precision.
3. Lightweight Materials for Electric Vehicles
EVs need lighter parts. Automotive injection molds reduce plastic weight. A mold maker optimizes materials.
4. Smart Plastics for Connected Cars
New plastics integrate sensors. Automotive injection molds create high-tech parts. A mold maker innovates with new materials.
Advanced automotive injection molds shape high-quality plastic parts. A skilled mold maker ensures precision, efficiency, and durability. The future of automotive molding focuses on speed, accuracy, and sustainability.