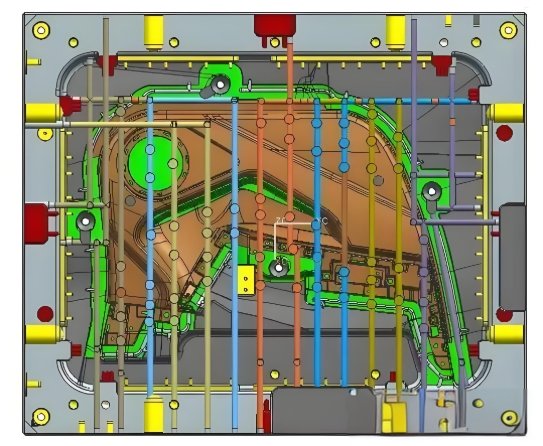
The automotive industry evolves fast. Automotive injection molds play a crucial role. A skilled mold maker ensures precision and efficiency. New trends improve quality, speed, and sustainability.
1. Lightweight Materials for Fuel Efficiency
Why Lighter Parts Matter
Fuel efficiency is a priority. Automotive injection molds now focus on lightweight plastics. A mold maker selects durable yet light materials.
Common Lightweight Plastics
- Polypropylene (PP)
- Polycarbonate (PC)
- Glass-filled Nylon (PA)
- Carbon-fiber-reinforced composites
2. Advanced Simulation Technologies
How Simulations Improve Molding
Predicting mold behavior saves time. Automotive injection molds now rely on advanced simulations. A mold maker analyzes material flow and cooling.
Simulation Benefits
- Detects defects before production
- Reduces material waste
- Improves mold longevity
3. Smart Injection Molding Machines
Automation in Mold Manufacturing
Technology enhances efficiency. Automotive injection molds now use smart machines. A mold maker programs precise controls.
Features of Smart Molding Machines
- Real-time monitoring
- AI-driven quality checks
- Automated temperature adjustments
4. Sustainable and Recycled Materials
Eco-Friendly Plastic Alternatives
Green solutions matter. Automotive injection molds now use biodegradable and recycled plastics. A mold maker ensures sustainability.
Sustainable Materials Used
- Bio-based Polyamides
- Recycled ABS
- Eco-friendly Polyesters
5. Multi-Material Molding Techniques
Why Use Multiple Materials?
Combining materials increases strength. Automotive injection molds now feature overmolding and insert molding. A mold maker ensures seamless bonding.
Applications of Multi-Material Molding
- Soft-touch dashboards
- Hybrid structural components
- Seals and gaskets
6. Electric Vehicle (EV) Component Molding
How EVs Change Mold Design
EVs need specialized parts. Automotive injection molds now focus on lightweight and heat-resistant plastics. A mold maker adjusts designs for battery enclosures.
Popular EV Molding Applications
- Battery casings
- Lightweight interior panels
- High-voltage cable insulation
7. High-Precision 3D-Printed Molds
How 3D Printing Helps Mold Makers
Rapid prototyping speeds up production. Automotive injection molds now use 3D-printed prototypes. A mold maker tests designs faster.
Advantages of 3D-Printed Molds
- Faster mold development
- Lower prototype costs
- Improved design flexibility
8. Gas-Assisted Injection Molding
Why Use Gas Assistance?
Hollow parts reduce weight. Automotive injection molds now use gas injection. A mold maker ensures smooth, defect-free parts.
Common Applications
- Door handles
- Instrument panels
- Air ducts
9. Improved Cooling Systems for Faster Cycles
How Cooling Affects Production
Faster cooling means quicker cycles. Automotive injection molds now use advanced cooling channels. A mold maker optimizes heat transfer.
Cooling Innovations
- Conformal cooling channels
- Beryllium copper inserts
- Water-assisted cooling
10. AI-Powered Quality Control
How AI Enhances Molding
Artificial intelligence improves precision. Automotive injection molds now include AI inspections. A mold maker ensures zero defects.
AI Applications in Injection Molding
- Automated defect detection
- Real-time production monitoring
- Predictive maintenance
11. Low-Volume and Custom Molding for Specialty Cars
Why Customization Matters
Luxury and specialty cars require unique parts. Automotive injection molds now cater to low-volume runs. A mold maker creates custom solutions.
Common Custom Molded Parts
- High-end interior trims
- Unique grille designs
- Specialty lighting components
12. Enhanced Mold Durability and Coatings
How Coatings Extend Mold Life
Wear resistance increases efficiency. Automotive injection molds now feature advanced coatings. A mold maker applies surface treatments.
Common Coatings Used
- Nickel plating
- Diamond-like carbon (DLC)
- Teflon coatings
13. Micro-Molding for Small Automotive Components
Why Smaller Parts Need Precision
Miniaturization improves vehicle efficiency. Automotive injection molds now create micro-components. A mold maker ensures high precision.
Examples of Micro-Molded Parts
- Sensor housings
- Small gears
- Electrical connectors
14. Faster Mold Development with Digital Twins
How Digital Twins Work
Virtual models reduce errors. Automotive injection molds now use digital twin technology. A mold maker refines designs before production.
Digital Twin Benefits
- Real-time mold performance monitoring
- Faster design validation
- Reduced development costs
15. Hot Runner Systems for Efficiency
Why Use Hot Runners?
Cold runners waste plastic. Automotive injection molds now favor hot runner systems. A mold maker minimizes material loss.
Hot Runner Benefits
- Faster cycle times
- Reduced waste
- Improved part consistency
The future of automotive injection molds looks promising. A skilled mold maker adapts to new trends. Advanced materials, smart technology, and sustainability drive innovation. Keeping up with these changes ensures top-quality vehicle components.