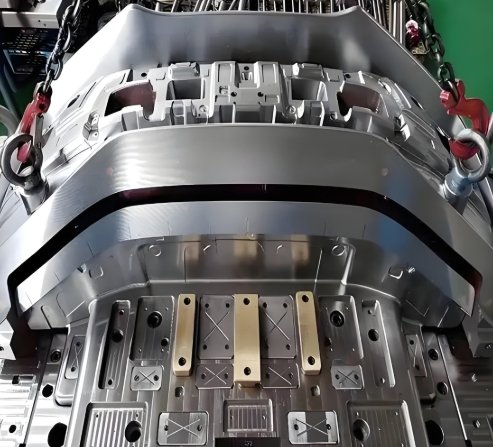
High-performance automotive parts require precision. Automotive Injection Molds deliver this precision. Expert Mold Makers ensure quality. These molds meet strict requirements. They produce durable, efficient, and complex components.
Why High-Performance Parts Need Precision
1. Exact Fit
High-performance parts demand accurate dimensions.
2. Durability
Molds produce parts that withstand stress.
3. Lightweight Construction
Precision molds reduce unnecessary weight.
4. Complex Designs
Molds create intricate shapes with ease.
Key Features of Automotive Injection Molds
1. High-Temperature Resistance
Molds handle tough materials like carbon fiber.
2. Smooth Surface Finish
Molds ensure parts look and perform flawlessly.
3. Durability Under Pressure
They produce components for extreme conditions.
4. Advanced Cooling Systems
Efficient cooling speeds up production.
Role of the Mold Maker
1. Material Selection
Mold Makers choose strong, durable materials.
2. Design Expertise
They create precise designs for each part.
3. Quality Control
Every mold undergoes rigorous testing.
4. Use of Advanced Tools
CNC and 3D printing ensure accuracy.
Applications of High-Performance Molds
1. Engine Components
Molds craft durable engine covers.
2. Transmission Parts
Injection molds ensure smooth operation.
3. Suspension Systems
Precision parts enhance vehicle stability.
4. Aerodynamic Features
Molds shape lightweight and efficient panels.
Innovations in High-Performance Mold Design
1. Multi-Material Molds
Combine different materials for stronger parts.
2. Hot Runner Systems
Reduce waste and improve efficiency.
3. Smart Molds
Sensors monitor molding in real time.
4. Eco-Friendly Solutions
Green molds reduce production waste.
Steps in Producing High-Performance Molds
1. Design Phase
Create digital models of the mold.
2. Prototype Testing
Build and test a sample mold.
3. Material Selection
Choose materials suited for high-performance parts.
4. Precision Machining
Use advanced tools to build the mold.
5. Final Testing
Ensure the mold meets performance standards.
Benefits of Using Injection Molds
1. Cost Efficiency
Molds reduce material waste.
2. Speed
They allow faster production times.
3. Accuracy
Molds produce consistent, reliable parts.
4. Customization
They meet specific performance needs.
Challenges in High-Performance Molding
1. Material Complexity
High-performance parts need advanced materials.
2. Design Accuracy
Precision is crucial for performance.
3. Cost of Innovation
Advanced molds require significant investment.
4. Production Scalability
Meeting large-scale demand can be challenging.
Trends in High-Performance Automotive Molds
1. Lightweight Materials
Focus on reducing vehicle weight.
2. Sustainability
Eco-friendly practices are on the rise.
3. Automation
Robots streamline mold production.
4. AI Integration
Artificial intelligence enhances mold accuracy.
Future of High-Performance Molding
1. Eco-Friendly Molds
Sustainability will lead innovation.
2. Advanced Materials
Stronger, lighter materials will emerge.
3. Smart Manufacturing
Real-time monitoring will improve efficiency.
4. Customization at Scale
Molds will adapt to diverse needs.
Automotive Injection Molds are essential for high-performance parts. Skilled Mold Makers ensure precision and quality. These molds meet strict automotive standards. With continuous innovation, they are shaping the future of high-performance vehicles.