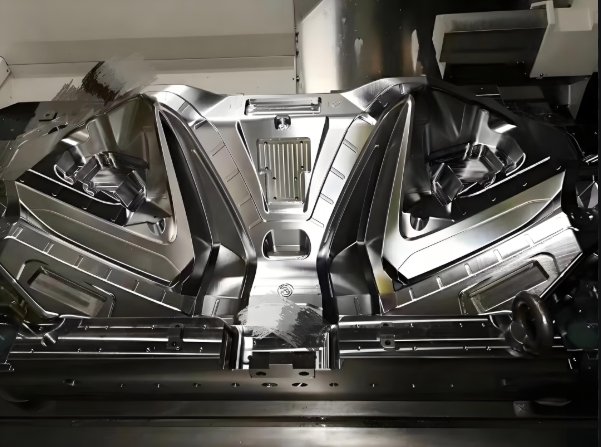
Hybrid vehicles demand innovative designs. Automotive Injection Molds meet these demands with precision. Skilled Mold Makers play a critical role. They craft molds for lightweight, durable, and efficient parts. These innovations drive the hybrid vehicle market forward.
Importance of Automotive Injection Molds
1. Precision for Hybrid Components
Accurate molds ensure perfect fit and function.
2. Lightweight Designs
Molds create parts with reduced weight.
3. Efficiency
Injection molds streamline mass production.
4. Durability
High-quality molds produce long-lasting parts.
Innovations in Mold Design
1. Lightweight Materials
Molds now use materials like carbon fiber.
2. Advanced Cooling Systems
Faster cooling improves production speed.
3. Complex Shapes
Molds handle intricate hybrid vehicle designs.
4. Sustainability
Eco-friendly molds reduce waste.
Key Applications for Hybrid Vehicles
1. Battery Housings
Custom molds ensure proper protection for batteries.
2. Powertrain Components
Molds produce lightweight engine covers.
3. Aerodynamic Parts
Injection molds create streamlined exterior designs.
4. Interior Features
Dashboard components and trim rely on precision molds.
Role of the Mold Maker
1. Design Expertise
Mold Makers develop accurate and efficient designs.
2. Material Selection
They choose materials for durability and weight reduction.
3. Advanced Tools
Using CNC and 3D printing ensures precision.
4. Quality Assurance
Testing guarantees performance and reliability.
Steps in Hybrid Vehicle Mold Production
1. Concept Development
Understand the unique part requirements.
2. 3D Modeling
Create a digital design of the mold.
3. Material Selection
Choose high-strength, lightweight materials.
4. Prototype Creation
Produce and test the mold prototype.
5. Production
Manufacture the final mold with advanced machinery.
6. Testing and Validation
Ensure molds meet all specifications.
Advantages of Advanced Injection Molds
1. Cost Savings
Efficient molds reduce material waste.
2. High Precision
Accurate molds improve product quality.
3. Sustainability
Eco-friendly designs support green initiatives.
4. Fast Production
Advanced molds shorten production times.
Challenges in Mold Innovations
1. Material Compatibility
Molds must match hybrid vehicle material needs.
2. Design Complexity
Creating molds for intricate parts is challenging.
3. Cost of Innovation
Advanced technology increases upfront costs.
4. High Accuracy Requirements
Precision is crucial for hybrid components.
Emerging Trends
1. Smart Molds
Sensors monitor the molding process.
2. 3D Printing Integration
Rapid prototyping accelerates production.
3. Sustainable Practices
Green mold designs reduce environmental impact.
4. Lightweight Technology
Focus on reducing vehicle weight.
Applications in Key Systems
1. Electric Motors
Molds create precise motor casings.
2. Cooling Systems
Injection molds shape efficient cooling channels.
3. Suspension Components
Custom molds craft durable suspension parts.
4. Energy Storage Units
Battery packs rely on lightweight molds.
Collaboration with Automakers
1. Understanding Needs
Mold makers work closely with automakers.
2. Customization
Every mold matches the vehicle’s unique design.
3. Prototyping
Testing ensures compatibility with hybrid systems.
4. Continuous Improvement
Feedback leads to better designs over time.
Future of Hybrid Vehicle Molds
1. Increased Automation
Robotic systems streamline mold production.
2. New Materials
Innovative composites improve durability and weight.
3. AI Design Tools
Artificial intelligence enhances mold accuracy.
4. Eco-Friendly Innovations
Focus on reducing carbon footprints.
Automotive Injection Molds revolutionize hybrid vehicle production. Skilled Mold Makers deliver precision and innovation. These molds enable lightweight, efficient, and sustainable designs. As technology evolves, molds will continue shaping the future of hybrid vehicles.