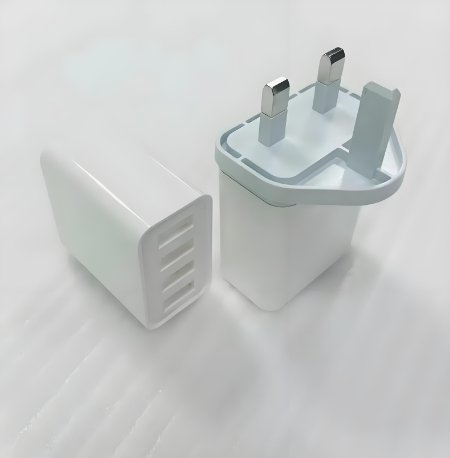
Sink marks are a common and frustrating problem in housing injection molding. These small, shallow depressions appear on the surface of molded plastic parts. Although they may seem minor, sink marks damage both the look and the function of plastic housings. For any mold maker or manufacturer producing high-quality enclosures, preventing sink marks must be a top priority.
In this article, we’ll explore what causes sink marks and how to avoid them. With smart design choices and expert molding practices, you can produce flawless housings without surface defects.
What Are Sink Marks?
Sink marks are surface dents that typically appear over thick areas of plastic. These defects form when the outer plastic cools faster than the inner plastic. As the inner plastic shrinks, it pulls the surface inward, creating a visible dimple.
In housing injection molding, sink marks usually occur above:
- Ribs
- Bosses
- Thick walls
- Insert locations
These areas cool slowly, especially if the mold is not designed properly. A skilled mold maker knows how to balance the mold design to avoid these marks.
Why Sink Marks Matter in Housing Injection Molding
Plastic housings must be smooth, strong, and visually appealing. A visible sink mark makes the part look defective, even if it functions well. Worse, a large sink mark may weaken the part or cause warping. In applications like electronics or consumer goods, appearance matters. So even a small defect is unacceptable.
This makes sink mark prevention a major concern for any project involving housing injection molding. It’s not just about looks—it’s about quality and customer trust.
Common Causes of Sink Marks
Understanding the causes of sink marks is the first step to preventing them. Some common causes include:
1. Thick Walls or Uneven Wall Thickness
Thicker areas cool slower and shrink more, leading to sink marks. If wall thickness varies, the thicker zones will cause problems.
2. Improper Rib and Boss Design
Ribs and bosses are often necessary for strength or assembly. But if they are too thick or too close to the wall, they can create sink marks on the outer surface.
3. Poor Packing Pressure
Packing pressure fills out the part after initial filling. If pressure is too low or packing time too short, the inner areas shrink more, creating sink marks.
4. Inadequate Cooling
Uneven or insufficient cooling can cause inner areas to stay hot and shrink later. A mold maker must ensure that cooling lines are placed correctly.
5. Resin Choice
Some plastics shrink more than others. Materials with high shrinkage rates are more likely to cause sink marks unless managed carefully.
How to Avoid Sink Marks in Plastic Housings
To prevent sink marks, designers and molders must work together. The mold maker plays a key role in adjusting the mold and process settings. Here are the top methods used to avoid sink marks in housing injection molding:
1. Keep Wall Thickness Uniform
Avoid sharp changes in wall thickness. Maintain uniform walls wherever possible. If a thicker area is needed for structural reasons, use internal ribs or hollow structures instead of solid mass.
A good mold maker will analyze your part and suggest changes to make wall thickness more even. This change alone prevents many sink mark issues.
2. Optimize Rib and Boss Design
Ribs and bosses must follow design rules to avoid sink marks. General tips include:
- Rib thickness should be 50–70% of the wall thickness
- Space ribs away from walls to reduce visible surface marks
- Taper ribs to allow easy molding and ejection
The mold maker will simulate how the ribs and bosses affect shrinkage and make needed adjustments.
3. Increase Packing Pressure and Time
The packing phase helps keep material inside the mold until it cools. Increase both pressure and packing time to reduce internal shrinkage.
Work with the mold maker to optimize these settings. Use pressure sensors in the mold if needed. Too little packing causes sink marks. Too much packing causes flash or stress. The right balance is key.
4. Improve Cooling System Design
A well-designed cooling system ensures even temperature throughout the mold. Uniform cooling prevents uneven shrinkage, which causes sink marks.
The mold maker should:
- Add cooling channels near thick areas
- Use baffles or bubblers to reach narrow areas
- Use mold materials with good thermal conductivity
Sometimes, adding conformal cooling (curved channels made by 3D printing) greatly improves temperature control.
5. Use Low-Shrinkage Materials
Select a material with low shrinkage and high dimensional stability. Some materials like ABS and PC/ABS blends shrink less than others like PP or PE.
Talk to your mold maker about material selection. They can guide you to the best option based on shrinkage, part function, and surface finish.
6. Redesign to Hide Thick Areas
If a thick boss or support is needed, move it away from visible surfaces. Alternatively, break the thick area into several smaller ribs. This keeps the function while reducing the chance of sink marks.
An experienced mold maker will suggest these design changes during the tool design phase.
7. Simulate the Molding Process
Use mold flow simulation software to predict sink marks before building the mold. This technology allows the mold maker to test design changes and process parameters virtually.
You can avoid costly mold rework by simulating:
- Cooling behavior
- Packing pressure
- Shrinkage
- Fill balance
Modern simulation tools help perfect the process before it begins.
When Sink Marks Still Happen
Sometimes, despite best efforts, small sink marks still appear. In these cases, the mold maker may apply a few finishing techniques:
- Texture the mold surface to hide small marks
- Use gas-assist molding to prevent thick areas
- Add small flow leaders or flow restrictors
These methods are useful for critical visual parts in housing injection molding.
Conclusion
Sink marks may be a small surface defect, but they cause big headaches in housing injection molding. Fortunately, with proper design, material selection, and the help of a skilled mold maker, they are easy to prevent.
Key steps include:
- Keeping walls thin and uniform
- Designing ribs and bosses correctly
- Controlling packing pressure
- Improving mold cooling
- Simulating mold behavior before production
With these best practices, your plastic housings will be smooth, reliable, and defect-free. And your customers will notice the difference.
The best way to avoid sink marks is to plan ahead—with a great team and a knowledgeable mold maker by your side.