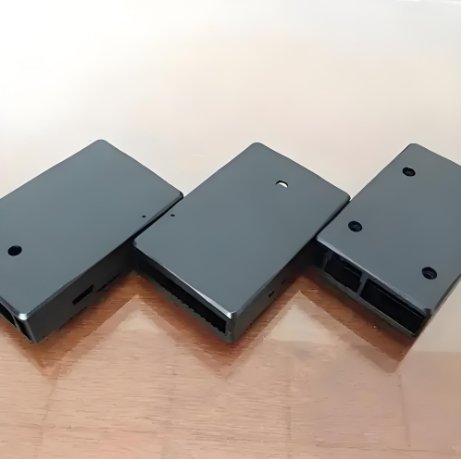
Plastic housings are critical in modern product design. Whether it’s for electronics, home appliances, medical devices, or industrial equipment, the outer shell protects the internal components and defines the product’s appearance. When you need quality plastic housings, housing Injection Molding is the most reliable process. Choosing the best factory with a skilled Mold Maker is essential for getting durable, accurate, and cost-effective results.
This article will guide you through what makes an injection molding factory the best choice for housing parts. It will explain how housing Injection Molding works, the role of the Mold Maker, and what to look for in a top-tier manufacturing partner.
What Is Housing Injection Molding?
Housing Injection Molding is a plastic manufacturing process used to create protective casings and enclosures. It involves injecting melted plastic into a specially designed mold. After cooling, the plastic forms a solid housing with the exact shape and features required.
Plastic housings are used in:
- Smart home devices
- Remote controls
- Medical monitoring equipment
- Battery packs
- Automotive control units
- Communication devices
With housing Injection Molding, manufacturers can produce thousands of identical, high-quality parts at a fast pace. This process is especially useful when the housing needs fine details, strong walls, and smooth finishes.
Why a Mold Maker Matters in Injection Molding
A Mold Maker is the professional who builds the mold used in the injection process. The mold is the heart of the entire production. It shapes the plastic and determines the accuracy, strength, and finish of every housing part.
A skilled Mold Maker:
- Understands material shrinkage and flow
- Designs proper cooling channels
- Ensures easy part release
- Builds molds that last for hundreds of thousands of cycles
Without a high-quality mold, even the best machine cannot produce a good part. That’s why a factory with expert Mold Makers offers a real advantage in housing Injection Molding.
Features of the Best Injection Molding Factory
When looking for the best factory for housing Injection Molding, you should focus on several important features.
1. In-House Mold Making
Factories that build their own molds have full control over the tooling. Their Mold Makers can adjust the design, fix issues, and reduce lead times. This saves you both time and money.
2. Precision Equipment
Top factories use high-precision CNC machines, EDM machines, and fully automatic injection molding equipment. This ensures your housings meet tight tolerances and deliver consistent quality.
3. Experienced Engineers
Technical knowledge is key. A factory with engineers who understand mold design, material science, and product function can give you the best results in housing Injection Molding.
4. Clean and Organized Facility
A clean factory often reflects high standards. Modern factories maintain strict cleanliness and follow ISO standards to ensure quality control at every step.
5. Strong Quality Control System
Quality must be checked regularly. Leading factories inspect raw materials, perform in-process checks, and test final products before shipping. This is especially important for critical housing parts.
6. Fast Turnaround and On-Time Delivery
A great factory delivers fast. Look for clear timelines for mold making, sampling, and mass production. A delay in housing Injection Molding can cost you sales and hurt your reputation.
Materials Used in Housing Injection Molding
Choosing the right plastic is a big part of the success. An experienced Mold Maker will help you pick a material based on your product’s needs. Common materials include:
- ABS: Tough, lightweight, and easy to mold. Great for electronics.
- PC: Strong and transparent. Often used for impact-resistant housings.
- PC+ABS: Combines strength and processability. A popular choice.
- PA (Nylon): High mechanical strength. Used for demanding environments.
- PP: Lightweight, chemical-resistant, and flexible. Good for consumer products.
Each of these materials behaves differently during molding. That’s why the Mold Maker must design the mold carefully to match the plastic used.
Advantages of Housing Injection Molding
The reason so many companies choose housing Injection Molding is because of its many benefits:
- Consistency: Every part comes out the same. Perfect for high-volume production.
- Detail and Complexity: Snap fits, bosses, and ribs can be molded into the housing.
- Low Cost Per Part: Once the mold is made, the unit cost drops fast.
- Speed: Molding cycles are short. You get your parts quickly.
- Strength and Durability: Molded parts can handle drops, pressure, and heat.
By working with a good Mold Maker, these advantages become even more reliable. You avoid errors, waste, and production delays.
Why China Is a Leading Location for Injection Molding
Many of the world’s top housing Injection Molding factories are based in China. Here’s why:
- High-Level Tooling Skills: Chinese Mold Makers have decades of experience and use the latest software and machines.
- Cost Savings: Lower labor costs and efficient systems keep pricing competitive.
- Global Shipping: Factories are well connected to ports and shipping hubs.
- Fast Mold Builds: Chinese factories can build complex molds in under 30 days.
- English Communication: Many engineers and managers speak English and understand global product standards.
If you’re launching a new product, a trusted Chinese factory with a top Mold Maker is often the smartest and most affordable choice.
Applications of Housing Injection Molding
Here are just a few examples where plastic housings are essential:
- Medical Devices: Durable housings protect electronics inside monitors, pumps, or diagnostic tools.
- Consumer Electronics: Sleek, lightweight housings improve the look and feel of phones, chargers, and remotes.
- Industrial Tools: Rugged casings handle dust, water, and impacts.
- Automotive: ECU covers, dashboard controls, and sensor enclosures all need precise housings.
- Smart Home Devices: Thermostats, security cameras, and assistants require attractive and functional housing parts.
In each of these industries, housing Injection Molding plays a key role, and the Mold Maker ensures long-term performance and consistent product quality.
How to Start Your Project with a Trusted Factory
Here’s how a project typically works:
- Send Your Design
Share your 3D model, material preferences, and estimated quantities. - Receive a DFM Report
The factory’s Mold Maker checks for design improvements and tooling suggestions. - Get a Quote and Lead Time
You’ll receive mold and part pricing, as well as expected delivery dates. - Approve the Mold Design
Once approved, the mold is built with full updates during the process. - Sample and Confirm
First molded parts are sent to you for testing and feedback. - Mass Production
After approval, the factory starts full production and prepares for shipment. - Shipping and Support
Parts are packed securely and delivered on time. Support continues after delivery.
This process ensures your housing Injection Molding project moves quickly and meets your quality expectations.
Final Thoughts
Finding the best factory for housing Injection Molding starts with one thing: trust. You need a partner with the right tools, experience, and team—especially a smart and capable Mold Maker. The mold is where your product begins, and only a skilled professional can deliver the performance you need.
Whether you’re a startup creating your first product or a global company launching a new model, your housing matters. It protects, defines, and delivers value. By choosing a top factory with expert Mold Makers, you guarantee success from the very first part.
With strong materials, accurate molds, and proven results, the best housing Injection Molding factory will take your project from idea to reality—on time, on budget, and with quality you can trust.