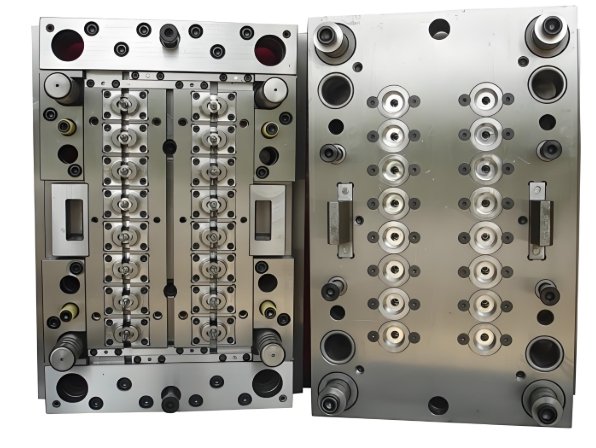
Medical devices need high precision. Medical injection molding makes reliable parts. A skilled mold maker selects the right materials. This ensures safety, durability, and compliance.
1. Importance of Material Selection
Why Materials Matter
Medical devices require biocompatibility. They must resist chemicals, heat, and wear. Choosing the right material improves performance.
Factors to Consider
- Biocompatibility – Must be safe for the human body.
- Sterilization Compatibility – Withstands heat, radiation, and chemicals.
- Durability – Resists stress and impact.
- Flexibility – Some applications need soft materials.
- Regulatory Compliance – Must meet FDA and ISO standards.
2. Common Plastics in Medical Injection Molding
1. Polypropylene (PP)
PP is lightweight and chemical-resistant. It is used in syringes and lab equipment.
2. Polyethylene (PE)
PE is flexible and tough. It is used in tubing and containers.
3. Polycarbonate (PC)
PC is strong and impact-resistant. It is used in surgical instruments and housings.
4. Polyether Ether Ketone (PEEK)
PEEK is highly durable. It is used in implants and orthopedic devices.
5. Polystyrene (PS)
PS is rigid and cost-effective. It is used in petri dishes and test tubes.
6. Acrylonitrile Butadiene Styrene (ABS)
ABS is tough and heat-resistant. It is used in device casings.
3. Medical-Grade Silicone
Silicone is soft and flexible. It is used for seals, catheters, and implants.
Benefits of Silicone
- Biocompatible – Safe for human contact.
- Flexible – Suitable for tubing and soft-touch components.
- Heat Resistant – Can withstand sterilization.
4. Biodegradable and Resorbable Polymers
Polylactic Acid (PLA)
PLA is used in temporary implants. It breaks down inside the body.
Polyglycolic Acid (PGA)
PGA dissolves after a certain time. It is used in sutures and stents.
Polycaprolactone (PCL)
PCL is used for drug delivery systems. It gradually dissolves.
5. Metal Injection Molding in Medical Devices
Metals are sometimes used in medical injection molding.
Common Medical-Grade Metals
- Titanium – Used in implants and prosthetics.
- Stainless Steel – Used in surgical tools.
- Cobalt-Chrome – Used in joint replacements.
6. The Role of a Mold Maker in Material Selection
Precision Mold Design
A skilled mold maker creates high-accuracy molds. This ensures quality and consistency.
Material Testing
Before production, materials are tested for durability and safety.
Optimizing Production Efficiency
Choosing the right material reduces defects and waste.
7. Ensuring Compliance in Medical Injection Molding
FDA Regulations
Medical materials must meet FDA standards for safety.
ISO 13485 Certification
This ensures strict quality control in medical injection molding.
Good Manufacturing Practices (GMP)
GMP ensures consistent and safe production.
8. Future Trends in Medical Injection Molding Materials
Smart Polymers
These materials change properties based on conditions.
Eco-Friendly Bioplastics
More medical devices will use sustainable materials.
Antimicrobial Plastics
New materials prevent bacterial growth.
Material selection is crucial in medical injection molding. A skilled mold maker ensures safety and precision. The right materials improve durability and compliance. Choosing the best option enhances healthcare solutions.