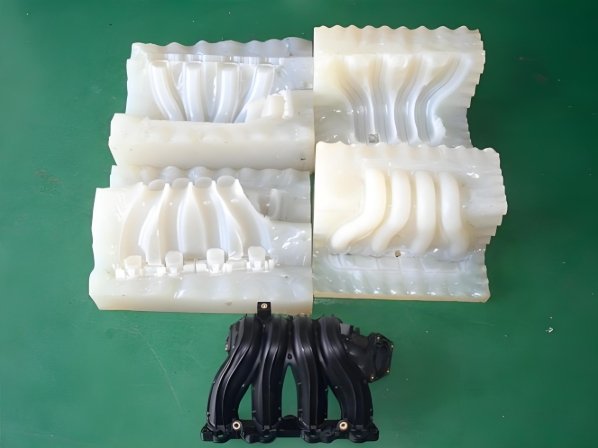
Rapid Prototyping is essential in modern manufacturing. It creates quick and accurate prototypes of products. An injection mould company relies heavily on this method. Prototypes help improve designs and reduce production risks.
This article highlights best practices for effective rapid prototyping.
Start with a Clear Objective
Define your goals before starting. Know what you want to achieve with the prototype. Goals may include testing shapes, fitting parts, or improving functionality. A clear objective saves time and avoids unnecessary work.
Use Suitable Materials
Choose the right material for the prototype. Material choice depends on the purpose of the prototype. For strength testing, use durable materials. For quick visual checks, cheaper materials work. In an injection mould company, matching materials to production needs is key.
Choose the Right Technology
Many technologies support rapid prototyping. Options include 3D printing, CNC machining, and injection molding. Select the technology that best fits your project. For precise molds, CNC machining is ideal. For visual models, 3D printing is faster.
Collaborate with the Team
Collaboration improves results. Engineers, designers, and technicians should work together. Everyone must understand the prototype’s purpose. This avoids communication gaps. In an injection mould company, teamwork ensures efficiency.
Test Early and Often
Testing prototypes early identifies flaws. Fixing these flaws before full production saves money. Frequent testing improves product quality. It also avoids costly mistakes during manufacturing.
Iterate Your Designs
Design improvement happens in stages. Create, test, and adjust repeatedly. Each iteration brings the design closer to perfection. An injection mould company benefits from small adjustments during mold design. This reduces scrap rates and production errors.
Optimize Design for Prototyping
Simplify designs to speed up prototyping. Avoid overly complex features at the prototype stage. Focus on the essential elements first. Complexity can be added later.
Document the Process
Record every step in the rapid prototyping process. Documentation helps track changes. It also ensures all team members stay informed. In an injection mould company, this prevents errors in mold development.
Focus on Functionality
A prototype should highlight the product’s core function. This ensures the final product meets performance requirements. Don’t waste resources on unnecessary features early on.
Balance Speed and Accuracy
Rapid Prototyping is about speed. However, accuracy is equally important. Fast prototypes should still meet quality standards. Find a balance between speed and precision.
Evaluate the Costs
Always monitor costs during rapid prototyping. Avoid overspending on unnecessary tools or materials. Set a budget and stick to it. An injection mould company should prioritize cost-effective solutions.
Use Advanced Tools
Invest in advanced tools for better results. Modern software helps improve design accuracy. 3D printing advancements offer faster and cheaper prototypes. In an injection mould company, technology upgrades boost production speed.
Train Your Team
Ensure your team has the skills needed for rapid prototyping. Training in new technologies improves efficiency. It also ensures better communication across departments.
Involve Stakeholders
Involve customers and stakeholders early in the process. Feedback from end-users helps improve the prototype. Customers can offer insights into practical use. This ensures the product meets their expectations.
Review Every Prototype
After creating a prototype, conduct a detailed review. Look for design flaws, material issues, or functional problems. Reviews improve the next iteration.
Use Digital Simulations
Digital tools allow simulations before creating physical prototypes. Simulations test performance in virtual environments. This saves time and materials.
Scale Gradually
Start with small-scale prototypes. Gradually move to larger, more detailed ones. Scaling ensures no flaws are overlooked. In an injection mould company, this helps avoid wasting large resources on faulty molds.
Adapt to Market Needs
Design requirements may change. Stay flexible to adapt prototypes to market trends. Rapid Prototyping allows quick adjustments. Flexibility keeps companies competitive.
Effective rapid prototyping ensures product success. It saves time, reduces errors, and improves designs. For an injection mould company, it ensures better molds and faster production. By following these best practices, companies can streamline development and remain competitive.