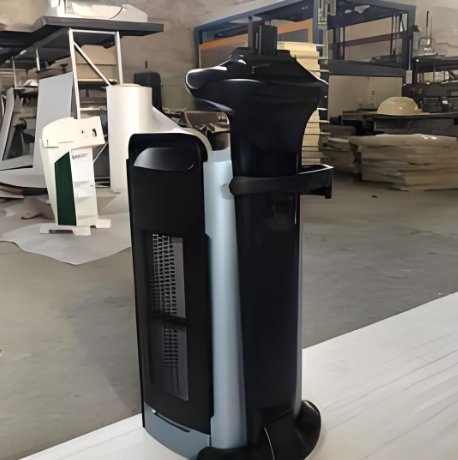
As global industries shift toward greener practices, the demand for sustainable manufacturing methods is higher than ever. Among these, bio-based plastics and eco-friendly molding practices stand out. A modern Injection Molding Company that embraces biodegradable and plant-based materials offers manufacturers an opportunity to reduce their carbon footprint while maintaining quality. At the heart of this transition is the skilled Mold Maker, who ensures tools are designed to handle these unique materials.
This article explores how bio-based injection molding works, the advantages it brings, and how a forward-thinking Injection Molding Company and expert Mold Maker can support eco-conscious brands.
What Is Bio-Based Injection Molding?
Bio-based injection molding uses plastics derived from renewable biological resources rather than fossil fuels. These plastics are typically made from corn starch, sugarcane, or cellulose, and many are biodegradable or compostable.
Popular bio-based materials include:
- PLA (Polylactic Acid) – Made from fermented corn starch
- PHA (Polyhydroxyalkanoates) – Produced by microbial fermentation
- PBS (Polybutylene Succinate) – Derived from sugar
- Bio-PE and Bio-PET – Identical to conventional plastics but made from plant-based sources
A qualified Injection Molding Company must understand the flow characteristics, drying requirements, and shrinkage rates of these materials. The Mold Maker must also adjust tooling to optimize part quality and reduce defects.
Why Choose a Bio-Based Injection Molding Company?
1. Environmental Responsibility
Choosing a bio-based Injection Molding Company helps reduce your environmental impact. These materials use less energy during production and emit fewer greenhouse gases.
2. Brand Value
Eco-friendly practices appeal to modern consumers. Brands working with green-certified Injection Molding Companies and professional Mold Makers often gain a competitive advantage.
3. Compliance with Green Regulations
More regions are mandating the use of sustainable materials. Using bio-based plastics ensures compliance and future-proofs your supply chain.
4. Compostability and Recyclability
Many bio-based plastics are industrially compostable. Others can be chemically recycled or reused, making them part of a closed-loop system.
Challenges with Bio-Based Molding
Working with bio-based plastics requires expertise. A typical Injection Molding Company may not be equipped for these materials.
Common challenges include:
- Low heat resistance (especially for PLA)
- Moisture sensitivity
- Shrinkage and warping risks
- Lower mechanical strength compared to conventional plastics
This is where the Mold Maker plays a critical role. Tools must be designed to accommodate faster cooling cycles, optimized flow channels, and proper venting to avoid burn marks or voids.
The Role of the Mold Maker
Every successful project begins with tooling. The Mold Maker must modify their approach when designing for bio-based materials. Here’s how:
1. Steel Selection
Some bio-based plastics are abrasive. The Mold Maker selects corrosion-resistant and wear-resistant steel.
2. Tool Coating
To extend mold life and reduce material adhesion, coatings like DLC (Diamond-Like Carbon) or nickel plating are used.
3. Optimized Venting
Bio-based plastics generate more gas during molding. Vents must be positioned precisely to avoid defects.
4. Shorter Cycle Time Management
Most bio-based materials cool faster. The Mold Maker designs tools that balance cooling speed with dimensional accuracy.
5. Gate Design Adjustments
The gate and runner system must allow smooth flow with minimal stress. This avoids shear degradation, which is more common in biodegradable resins.
A sustainable Injection Molding Company always works hand-in-hand with a skilled Mold Maker to ensure the success of green products.
Applications of Bio-Based Injection Molding
Eco-friendly plastics are no longer limited to disposable utensils. They are now used in a wide range of industries:
- Packaging – Food containers, cosmetic caps, blister packs
- Consumer Goods – Mobile phone cases, toys, homeware
- Medical Devices – Single-use items like pill trays, dental tools
- Agricultural Products – Seed trays, plant pots, irrigation tools
- Automotive Interiors – Panels and trims made from bio-composites
- Electronics – Housings, buttons, switches
An innovative Injection Molding Company can support product designers from concept to production with custom bio-material solutions.
Key Features of a Green Injection Molding Company
1. Material Expertise
Your Injection Molding Company should offer detailed guidance on the best bio-based material for your application.
2. In-House Mold Maker Team
Having a dedicated Mold Maker allows for quicker tool design and changes. It also reduces lead time.
3. Efficient Machines
Modern, energy-efficient injection molding machines reduce energy consumption and CO₂ output.
4. Waste Reduction Practices
Look for a company with closed-loop recycling, minimal scrap rates, and zero-waste production targets.
5. Certifications
Choose a Mold Maker and Injection Molding Company certified in ISO 14001 (Environmental Management) and ISO 9001 (Quality Management).
Future of Bio-Based Plastic Injection Molding
Sustainability is not just a trend—it’s the future. With growing demand from governments, businesses, and consumers, Injection Molding Companies are investing in greener methods. As material science evolves, new bio-based compounds will offer better heat resistance, strength, and cost-effectiveness.
Partnering with an eco-conscious Injection Molding Company and a technical Mold Maker today will help your business lead the way tomorrow.
Conclusion
Switching to bio-based plastics isn’t just good for the environment—it’s good for business. To ensure success, work with an experienced Injection Molding Company that understands sustainable materials and collaborates with a reliable Mold Maker.
From prototype to production, the right partner can guide you through material selection, tool design, and process optimization—all while meeting green standards and maintaining part quality.
Sustainability begins with smart decisions. Make yours today by choosing a forward-thinking Injection Molding Company and a skilled Mold Maker who believe in building a better future—one part at a time.