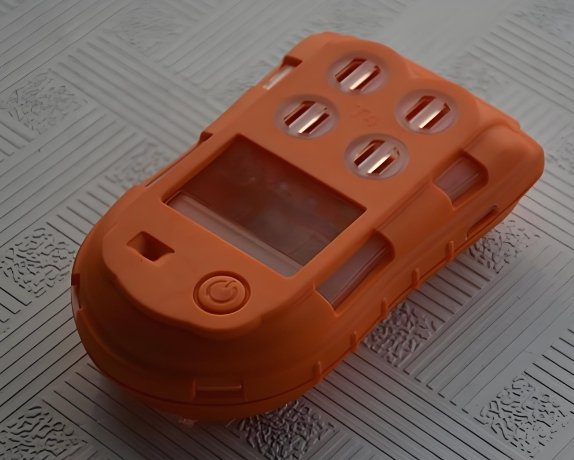
When it comes to manufacturing plastic housings, two popular molding processes often come into consideration: blow molding and housing injection molding. Both techniques serve different purposes and offer unique advantages. However, they are not always interchangeable, especially when product performance, strength, and dimensional accuracy are critical.
This article will dive deep into both processes and explain which one is the better choice for your plastic housing project. We’ll also explore the role of a skilled mold maker in delivering quality and precision.
Understanding the Basics
What Is Housing Injection Molding?
Housing injection molding is a process where molten plastic is injected into a custom-designed steel mold. Once the material cools, it forms a solid, high-precision part. The molds are engineered and built by a professional mold maker, ensuring exact shapes, consistent wall thicknesses, and strong mechanical properties.
What Is Blow Molding?
Blow molding involves inflating a heated plastic tube (called a parison) inside a mold cavity. As air fills the parison, it expands against the mold walls, forming a hollow part. This process is widely used for making bottles, containers, and other hollow objects.
Comparing the Two Methods
Let’s compare housing injection molding and blow molding across key categories to help identify the better solution for plastic housings.
1. Structural Strength and Function
Housing injection molding produces solid, high-strength parts. Since the plastic is injected under high pressure, it fills the mold completely and forms a dense, rigid structure. This is crucial for plastic housings that need to support internal components or withstand mechanical stress.
Blow-molded parts, on the other hand, are hollow and thin-walled. They are not designed to carry loads or protect internal electronics. Their strength is limited by wall thickness and material type.
✅ Winner: Housing Injection Molding
2. Design Complexity
A skilled mold maker can create intricate mold cavities for housing injection molding, allowing for precise features such as ribs, bosses, snap fits, and screw posts. These are essential for assembly and functionality.
Blow molding is limited in design. It’s mainly suitable for smooth, hollow shapes like bottles or tanks. Creating internal structures or detailed external features is very difficult or impossible.
✅ Winner: Housing Injection Molding
3. Surface Finish and Tolerances
Housing injection molding delivers excellent surface finishes straight from the mold. Textures, gloss levels, and even logos can be directly included in the tooling. Tight tolerances (±0.05–0.1 mm) are achievable, making this process ideal for enclosures that require assembly with other parts.
Blow-molded parts usually require post-processing to improve their appearance. Tolerances are also looser, making them unsuitable for precision fits.
✅ Winner: Housing Injection Molding
4. Material Options
Both processes can use similar thermoplastics. However, housing injection molding supports a wider range of engineering-grade plastics such as ABS, polycarbonate, nylon, and glass-filled composites. These offer better heat resistance, stiffness, and durability.
Blow molding typically uses materials like HDPE, LDPE, or PET. These are good for containers but lack the performance required for housing applications.
✅ Winner: Housing Injection Molding
5. Production Volume and Cost
Blow molding has a lower tooling cost and is great for producing high volumes of hollow parts quickly. It’s highly cost-efficient for containers and bottles.
Housing injection molding requires a higher initial investment in mold tooling. However, once the mold is made by a skilled mold maker, the process becomes very efficient. For high-volume, high-quality housing production, it remains cost-effective over time.
✅ Winner: Tie (Blow molding for hollow, high-volume items; housing injection molding for solid, functional housings)
6. Wall Thickness and Uniformity
Housing injection molding offers superior wall thickness control. A precise mold maker ensures even flow, consistent cooling, and uniform material distribution. This prevents weak points and enhances part performance.
Blow molding often results in non-uniform wall thickness. Variations can weaken the structure and create quality concerns, especially in parts that require stability and durability.
✅ Winner: Housing Injection Molding
7. Applications
Blow molding is best for producing:
- Plastic bottles
- Fuel tanks
- Hollow toys
- Containers
Housing injection molding is ideal for:
- Electronic device enclosures
- Automotive housings
- Consumer appliance covers
- Industrial control boxes
If your project involves protection, assembly, or structure, housing injection molding is the clear winner.
✅ Winner: Housing Injection Molding
Why Mold Maker Expertise Matters
A successful housing injection molding project depends heavily on the mold maker. The mold is the heart of the process. A skilled mold maker ensures:
- Tight tolerances
- Proper flow paths
- Correct venting
- Minimal defects
- Fast cycle times
- Long mold life
Poor mold design can lead to defects like warping, short shots, sink marks, and flash. That’s why investing in a qualified mold maker is critical to your housing project’s success.
Case Study: Choosing the Right Process
Let’s say you’re developing a plastic housing for a smart home controller. The housing needs to:
- Hold circuit boards
- Fit with a back cover
- Provide screw mounting points
- Offer sleek surface finish
- Resist heat and mechanical stress
Blow molding would fail here. It can’t create the internal structures or meet the precision required. On the other hand, housing injection molding, supported by a reliable mold maker, can meet all these needs efficiently.
When Is Blow Molding a Better Fit?
Blow molding is not without value. If your product is:
- Hollow
- Lightweight
- Produced in very large volumes
- Not structurally demanding
Then blow molding is an excellent choice. It’s perfect for containers, tanks, and packaging.
Final Verdict: Which One Is Better for Housings?
Without a doubt, housing injection molding is the better choice for plastic housings. It delivers better strength, precision, surface quality, and functionality. With the help of an experienced mold maker, you can achieve long-term durability, production efficiency, and product consistency.
Blow molding is limited in terms of design and structure. It’s not suitable for projects that involve mechanical support or assembly.
Conclusion
When comparing blow molding vs. housing injection molding, the answer is clear: For any project involving structural plastic housings, housing injection molding wins in nearly every category. It offers unmatched quality, repeatability, and strength—especially when guided by a professional mold maker.
If you need plastic housings that protect, support, and look great, don’t compromise. Invest in housing injection molding and choose a trusted mold maker who understands your product’s needs from concept to production.