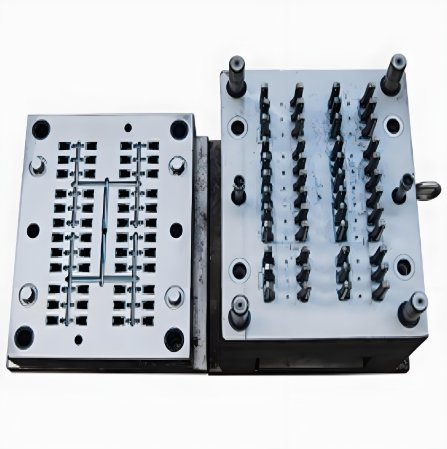
Medical products require high precision. Medical injection molding ensures accuracy. A skilled mold maker delivers consistent quality. Choosing the right partner is critical.
1. Why Medical Injection Molding Matters
High Precision Manufacturing
Medical devices need exact dimensions. Medical injection molding ensures precision.
Sterile and Safe Products
Contamination is dangerous. Cleanroom molding keeps parts sterile.
Cost-Effective Production
Mass production lowers costs. Medical injection molding improves efficiency.
2. Key Qualities of a Reliable Medical Injection Molding Partner
Experience in Medical Manufacturing
A partner must understand medical standards. Years of experience ensure reliability.
Advanced Equipment and Technology
Modern machines improve quality. Automated systems reduce errors.
Cleanroom Manufacturing Capability
A clean environment prevents contamination. Medical parts need strict hygiene.
Strong Quality Control Processes
Testing ensures accuracy. Reliable partners follow strict inspection protocols.
Regulatory Compliance
A good mold maker meets industry standards. Certifications prove quality.
3. Certifications to Look For
ISO 13485
Ensures quality in medical device production.
FDA Compliance
Required for medical products in the U.S.
USP Class VI Certification
Confirms biocompatibility for medical-grade plastics.
Good Manufacturing Practices (GMP)
Ensures consistency and safety.
4. Choosing a Mold Maker with Medical Expertise
Medical-Grade Material Knowledge
A skilled mold maker selects the right plastics. Material choice affects safety.
Tooling and Mold Design
The mold must meet precise tolerances. A good mold maker ensures accuracy.
Injection Molding Capabilities
Multi-shot molding, overmolding, and micro-molding improve medical devices.
5. Customization and Design Support
Prototyping Services
Rapid prototyping allows testing. A partner should offer small-batch production.
Collaborative Engineering
Experts refine designs. They improve efficiency and function.
Material Selection Assistance
Different applications need different plastics. A partner should guide choices.
6. Cleanroom Injection Molding for Medical Products
Why Cleanroom Molding is Essential
Medical parts must be free of contaminants. A cleanroom ensures sterility.
Cleanroom Manufacturing Levels
- Class 10,000 (ISO 7) – Low contamination risk
- Class 1,000 (ISO 6) – High-precision medical parts
Equipment and Automation in Cleanrooms
Robotics reduce human contact. Machines improve consistency.
7. Advanced Injection Molding Techniques
Micro-Molding for Small Parts
Tiny medical components require extreme precision. Medical injection molding achieves this.
Overmolding for Multi-Material Devices
Combining materials improves function. Soft-touch grips and seals are common.
Insert Molding for Enhanced Strength
Encapsulating metal parts increases durability. Used in surgical tools.
8. Quality Control in Medical Injection Molding
Inspection Methods
- Visual checks detect surface defects.
- Automated scanning ensures accuracy.
- Dimensional testing confirms precision.
Traceability and Documentation
Every batch must be trackable. Reliable partners provide full records.
Testing Procedures
- Biocompatibility Testing – Ensures safety for human contact.
- Mechanical Testing – Confirms strength and durability.
- Chemical Resistance Testing – Ensures compatibility with sterilization methods.
9. Scalability and Production Capacity
Small and Large-Scale Production
A good partner can handle any volume. From prototypes to mass production.
Flexible Manufacturing Options
- Custom batch sizes.
- Quick turnaround times.
- Capacity for urgent orders.
10. Sustainable Medical Injection Molding
Eco-Friendly Materials
Some medical-grade plastics are biodegradable. Recycled resins are also available.
Energy-Efficient Manufacturing
Modern machines reduce waste. Less material is discarded.
Waste Reduction Strategies
- Closed-loop recycling systems.
- Efficient mold design.
11. Industry Applications of Medical Injection Molding
Surgical Instruments
Scalpels, forceps, and clamps need high precision.
Implantable Devices
Pacemaker casings and joint replacements use biocompatible plastics.
Diagnostic Equipment
Test tubes, sample containers, and lab trays require accuracy.
Drug Delivery Systems
Syringes, inhalers, and insulin pens must be safe.
12. Partnering with a Trusted Medical Mold Maker
Reputation and Reviews
Check industry experience. Read client feedback.
Successful Case Studies
Reliable partners show past success. They demonstrate expertise.
On-Time Delivery Commitment
Medical products have strict deadlines. A reliable partner ensures timely supply.
13. Common Mistakes to Avoid When Choosing a Medical Injection Molding Partner
Ignoring Certifications
Regulatory compliance is essential. A partner must have proper credentials.
Overlooking Experience
Medical molding requires expertise. Choose an experienced mold maker.
Choosing Based on Cost Alone
Low prices may mean poor quality. Invest in a reliable partner.
Not Checking Quality Control Processes
Strict inspections are necessary. Weak quality control leads to defects.
14. Future Trends in Medical Injection Molding
AI-Powered Quality Control
Automated inspections improve accuracy. Reduces human error.
3D Printing for Prototyping
Speeds up product development. Reduces costs.
Smart Medical Materials
Self-healing plastics and antimicrobial surfaces improve device safety.
15. Final Steps in Choosing the Right Partner
Request Samples
Examine product quality before committing.
Tour the Facility
Visit the production site. Ensure cleanroom compliance.
Compare Multiple Suppliers
Evaluate different companies. Choose the best fit.
Choosing the right medical injection molding partner is crucial. A skilled mold maker ensures quality, precision, and safety. Look for experience, advanced technology, and strict quality control.