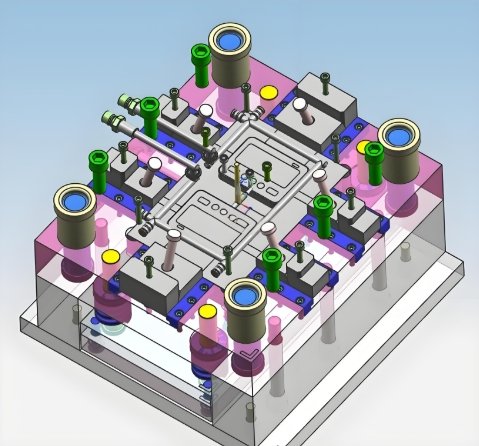
Electronic components require high-precision plastic parts. Electronic injection molding ensures accuracy and consistency. The choice of plastic is crucial. Mold makers must select materials that offer durability, heat resistance, and electrical insulation.
This guide explores the best plastics for electronic injection molding and their applications.
1. Why Material Selection Matters
1.1 Impact on Product Performance
- The wrong plastic can cause failures.
- Strength and flexibility must match application needs.
- Heat resistance prevents deformation.
1.2 Electrical Insulation Properties
- Electronics require non-conductive materials.
- Prevents short circuits and interference.
- Some plastics offer shielding against electromagnetic waves.
1.3 Chemical and Environmental Resistance
- Plastics must withstand chemicals and moisture.
- Some applications need UV and flame resistance.
2. Common Plastics in Electronic Injection Molding
2.1 Polybutylene Terephthalate (PBT)
- Excellent electrical insulation.
- High resistance to heat and moisture.
- Used in connectors, switches, and housings.
2.2 Polycarbonate (PC)
- Strong and impact-resistant.
- Can withstand high temperatures.
- Ideal for LED housings and protective covers.
2.3 Polyphenylene Sulfide (PPS)
- Heat and chemical resistant.
- Low moisture absorption.
- Used in high-performance electrical components.
2.4 Liquid Crystal Polymer (LCP)
- Excellent flow properties for thin-wall designs.
- High temperature and chemical resistance.
- Suitable for micro-electronic components.
2.5 Acrylonitrile Butadiene Styrene (ABS)
- Tough and lightweight.
- Easy to mold with precise details.
- Common in consumer electronics.
2.6 Nylon (Polyamide, PA)
- Strong and flexible.
- Good resistance to chemicals and wear.
- Used for cable ties and connectors.
2.7 Polyetherimide (PEI)
- High-performance thermoplastic.
- Exceptional heat and flame resistance.
- Ideal for aerospace and medical electronics.
3. Special Additives for Enhanced Properties
3.1 Flame Retardants
- Required for safety compliance.
- Prevents fire hazards in electronic devices.
3.2 Conductive and Anti-Static Additives
- Reduces static buildup.
- Protects sensitive electronic circuits.
3.3 Glass and Carbon Fiber Reinforcements
- Improves strength and rigidity.
- Reduces part shrinkage and warping.
3.4 UV Stabilizers
- Protects outdoor electronic components.
- Prevents discoloration and brittleness.
4. Selecting the Right Plastic for Your Application
4.1 High-Temperature Applications
- Use PPS, PEI, and LCP.
- Ensures durability in harsh conditions.
4.2 High-Strength Requirements
- PC, Nylon, and ABS provide toughness.
- Suitable for enclosures and protective covers.
4.3 Moisture-Resistant Parts
- PBT and PPS resist water absorption.
- Ideal for humid environments.
4.4 Thin-Walled Components
- LCP and PC allow precise molding.
- Suitable for micro-electronics.
5. The Role of the Mold Maker in Material Selection
5.1 Designing for Material Properties
- Mold makers must consider plastic shrinkage.
- Tooling adjustments ensure accurate dimensions.
5.2 Optimizing Mold Flow
- Poor flow causes defects like warping.
- Mold design improves plastic distribution.
5.3 Maintaining Mold Longevity
- Some plastics wear out molds faster.
- Hard coatings extend mold life.
6. Innovations in Electronic Injection Molding Materials
6.1 Biodegradable Plastics
- Eco-friendly alternatives for sustainability.
- Some still lack durability for electronics.
6.2 Smart Polymers
- Can change properties under specific conditions.
- Used for advanced applications.
6.3 Recycled Plastics
- Helps reduce environmental impact.
- Requires strict quality control.
7. Challenges in Material Selection
7.1 Balancing Cost and Performance
- High-performance plastics are expensive.
- Choosing the right material prevents unnecessary costs.
7.2 Meeting Industry Standards
- Materials must comply with UL94 and RoHS.
- Safety and environmental factors are critical.
7.3 Processing Challenges
- Some plastics require special handling.
- Drying and temperature control are essential.
8. Future Trends in Electronic Injection Molding Materials
8.1 Nanocomposites
- Offers extreme strength and lightweight properties.
- Can improve conductivity and durability.
8.2 AI in Material Selection
- Predicts the best plastic for each part.
- Reduces material waste and defects.
8.3 Fully Recyclable Electronics
- Advances in sustainable materials.
- Helps create a circular economy.
Material selection is critical in electronic injection molding. Mold makers must consider heat resistance, strength, and electrical properties. Choosing the right plastic ensures reliable and durable electronic components. As technology evolves, new materials will further improve performance and sustainability.