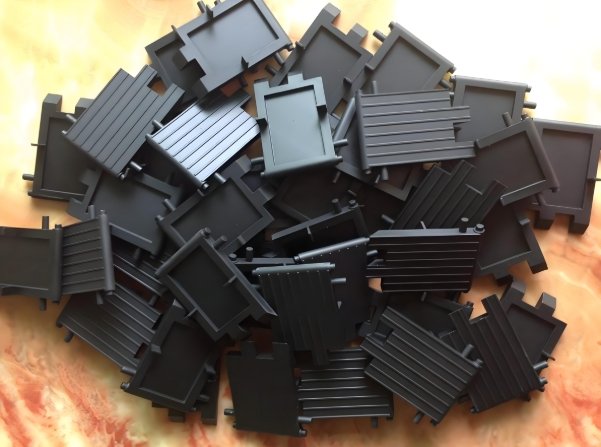
The combination of Rapid Prototyping and digital manufacturing is revolutionary. It speeds up production and cuts costs. Together, they create precise and efficient solutions. Working with an experienced Injection Mould Company makes this integration seamless. Let’s explore how these technologies complement each other.
What Is Rapid Prototyping?
Rapid Prototyping builds models quickly. It uses 3D printing, CNC machining, and other advanced tools. Prototypes test designs before mass production. This process saves time and identifies flaws early.
What Is Digital Manufacturing?
Digital manufacturing involves automated processes. Machines follow computer instructions to create products. This includes CAD designs and robotic systems. It ensures precision and repeatability.
Benefits of Combining the Two
Faster Development
The integration eliminates delays.
Cost Savings
Efficient use of materials reduces waste.
Better Accuracy
Digital tools ensure prototypes match designs.
Seamless Scaling
Prototypes transition smoothly to production.
How Rapid Prototyping Works with Digital Manufacturing
Step 1: Design Creation
CAD software designs the product.
Step 2: Prototype Development
Rapid Prototyping builds a model for testing.
Step 3: Digital Integration
Data from the prototype informs the manufacturing process.
Step 4: Automated Production
Machines use the refined design to produce at scale.
Why Work with an Injection Mould Company?
Design Expertise
They refine CAD models for production.
Material Selection
They recommend materials for durability and cost-efficiency.
Process Optimization
They streamline the transition from prototype to product.
Long-Term Collaboration
Their guidance supports future projects.
Key Technologies
1. 3D Printing
Creates detailed prototypes fast.
2. CNC Machining
Produces parts with high precision.
3. Laser Cutting
Shapes materials for fine details.
4. Robotics
Automates repetitive production tasks.
Applications in Industry
Medical Devices
Custom surgical tools benefit from precise prototyping.
Automotive Parts
Manufacturers test components for performance.
Consumer Products
Electronics enclosures are refined for mass production.
Aerospace
Lightweight materials enhance prototypes.
Challenges in Integration
Complex Designs
Complicated models take longer to process.
Material Limitations
Not all materials work for both stages.
Cost Management
Initial setup may seem expensive.
Technical Expertise
Inexperienced teams may face errors.
Overcoming Challenges
Simplify Designs
Focus on functionality over complexity.
Work with Experts
Collaborate with a skilled Injection Mould Company.
Use Advanced Tools
Invest in high-quality machines and software.
Test Frequently
Evaluate prototypes at every stage.
Case Study: Consumer Electronics
An electronics company needed faster production.
Problem
Their designs delayed scaling.
Solution
They adopted Rapid Prototyping and digital manufacturing.
Results
Production time dropped by 40%. Costs decreased by 25%.
Steps to Combine the Processes
Step 1: Choose a Reliable Partner
Select an experienced Injection Mould Company.
Step 2: Create Accurate CAD Designs
Ensure designs are clear and precise.
Step 3: Develop Functional Prototypes
Use Rapid Prototyping for testing.
Step 4: Transition to Digital Manufacturing
Automate the production process seamlessly.
Future Trends
AI Integration
AI will enhance design accuracy.
Advanced Materials
Innovative materials will improve prototypes.
Smart Factories
IoT will connect machines for better efficiency.
Faster Prototyping
New tools will reduce lead times further.
Combining Rapid Prototyping with digital manufacturing is transformative. It speeds up production, reduces costs, and ensures precision. Partnering with an Injection Mould Company simplifies the process. Embrace this integration to stay ahead in the industry.
Start combining these technologies today for smarter production!