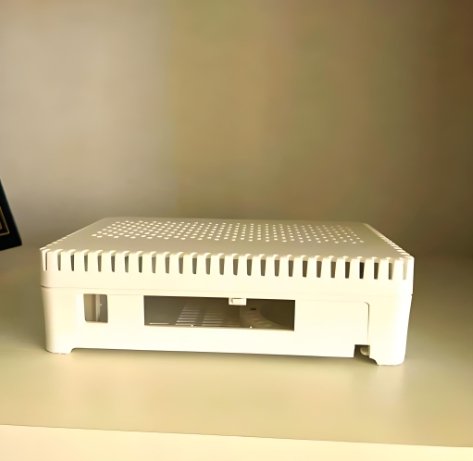
In the world of housing injection molding, precision and reliability are essential. Plastic housings protect electronics, devices, tools, and countless consumer products. However, mold-related problems often arise during production. These issues can lead to defective parts, wasted materials, machine downtime, and rising costs.
The good news? Each problem has a clear solution. With the help of a professional mold maker, manufacturers can prevent common mold issues and improve production quality. This article explores the most frequent problems in housing injection molding and how to fix them efficiently.
1. Warping and Deformation
Problem:
Plastic housings often warp or bend after molding. The part does not keep its intended shape, especially in flat surfaces or long sides. Warping ruins appearance, affects assembly, and weakens the housing.
Causes:
- Uneven cooling in the mold
- Improper gate placement
- Inconsistent wall thickness
- Residual stress in the part
Solutions:
- Use balanced cooling channels to ensure even temperature
- Adjust gate position and runner design
- Keep wall thickness uniform throughout the housing
- Allow for proper packing and cooling time before ejection
- A skilled mold maker can simulate and adjust the mold to prevent internal stress
2. Flash Formation
Problem:
Flash is thin plastic that leaks out along mold parting lines or ejector pins. It appears as extra material where it shouldn’t be. Flash affects the look and fit of the housing and may require manual trimming.
Causes:
- Poor mold fit or worn sealing surfaces
- Incorrect clamping pressure
- Debris on the mold surface
- Too much injection pressure
Solutions:
- Re-machine mold parting lines to improve sealing
- Use correct clamp force based on mold size and material
- Keep mold surfaces clean and polished
- Adjust injection settings with expert help from a mold maker
3. Sink Marks
Problem:
Sink marks are dents or dimples on the plastic surface. They happen when thicker areas cool slower than thinner ones. This causes uneven shrinkage.
Causes:
- Thick ribs or bosses near thin walls
- Inadequate packing pressure or time
- Poor mold cooling design
Solutions:
- Reduce the thickness of ribs or make them hollow
- Increase holding pressure and time during housing injection molding
- Use mold flow simulation to locate shrink-prone areas
- A mold maker can revise the core design to promote even cooling
4. Short Shots
Problem:
The molded housing is incomplete. Some parts are missing or unfilled. This is called a short shot. It often happens in thin sections or complex shapes.
Causes:
- Low injection pressure or speed
- Poor venting or blocked air traps
- Improper gate or runner design
- Material temperature too low
Solutions:
- Increase injection pressure and melt temperature
- Add or clean vents in trapped air zones
- Optimize gate location and size
- Let a mold maker redesign the runner system for better flow balance
5. Burn Marks
Problem:
Burn marks are black or brown spots on the housing surface. They are caused by trapped air that overheats during injection.
Causes:
- Poor venting in the mold
- High injection speed
- Small or blocked gates
- Narrow or long flow paths
Solutions:
- Improve venting in key areas
- Reduce injection speed to allow air escape
- Enlarge gates and optimize runner geometry
- Experienced mold makers always plan airflow carefully in housing injection molding
6. Ejector Pin Marks and Damage
Problem:
Visible marks or cracks near ejector pin areas. In severe cases, the housing may break during ejection.
Causes:
- Uneven force from ejector pins
- Pins placed too close to weak areas
- Improper pin size or shape
- Ejection started before full cooling
Solutions:
- Use more pins and distribute them evenly
- Select proper pin size and polished finish
- Wait longer for part to cool before ejecting
- A good mold maker will also use stripper plates or air ejection if needed
7. Cracking or Brittle Parts
Problem:
Housings may crack during use, assembly, or even during ejection from the mold. This affects performance and safety.
Causes:
- Incorrect plastic type for the application
- High internal stress from poor molding
- Sharp corners or stress concentrators in design
- Excessive pressure or poor mold temperature control
Solutions:
- Choose the right material with impact resistance
- Design rounded corners and gradual transitions
- Optimize the molding process and allow full cooling
- An expert mold maker understands how to combine part design with process needs
8. Mold Wear and Damage
Problem:
The mold itself becomes damaged or worn. This leads to poor part quality and requires costly repairs.
Causes:
- Low-quality steel or soft mold inserts
- Abrasive or high-temperature resins
- Lack of maintenance or cleaning
- Poor mold design under high cycle loads
Solutions:
- Use hardened tool steels like H13, S136, or P20
- Add surface coatings to reduce wear
- Clean and inspect the mold regularly
- Let an experienced mold maker design for long life and easy maintenance
9. Color Streaks or Contamination
Problem:
The molded housing shows streaks, black specks, or color mixing. This ruins appearance and quality.
Causes:
- Dirty mold or nozzle
- Poor resin mixing or colorant blending
- Long residence time of plastic in barrel
- Mold temperature too high or low
Solutions:
- Clean mold surfaces, hot runners, and screws
- Pre-mix colorants properly before molding
- Purge barrel regularly
- Monitor temperature zones with expert help from a mold maker
Conclusion
Every housing injection molding project faces challenges. From warping to cracking, each issue has technical causes—and practical solutions. But the real difference comes from planning and partnership.
By working closely with a trusted mold maker, you can:
- Prevent defects before they happen
- Choose the right materials and mold steels
- Optimize mold cooling, gating, and ejection
- Ensure your mold runs reliably for thousands of cycles
In short, the path to perfect plastic housings begins with knowledge and experience. With the right team, every problem has a solution. And every project can deliver strong, reliable, and high-quality molded housings.