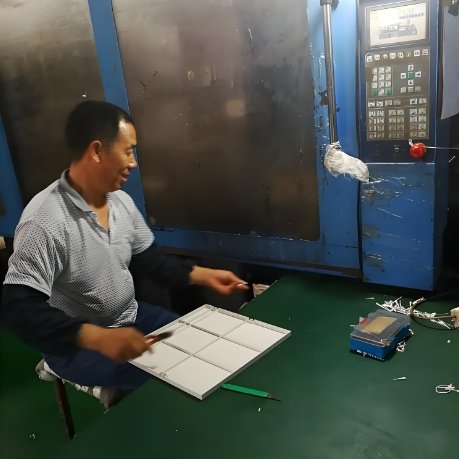
Housing Injection Molding is a powerful way to make durable and accurate plastic enclosures. It’s used in many industries—from electronics to medical devices and appliances. But this process also has challenges. Even small mistakes can lead to big problems in quality, time, and cost.
That’s why manufacturers work closely with a skilled Mold Maker. An expert Mold Maker understands the risks and knows how to avoid them. In this guide, we’ll explain the most common mistakes in Housing Injection Molding, how they affect production, and what steps a good Mold Maker takes to prevent them.
Let’s explore these issues in detail.
1. Poor Mold Design
Everything starts with the mold. If the design is wrong, every part it produces will be flawed. Poor mold design can lead to short shots, flash, warping, or weak structures.
Some common design problems include:
- Inadequate venting
- Improper gate placement
- Uneven wall thickness
- Lack of draft angles
An experienced Mold Maker will avoid these errors by carefully designing each mold to match the plastic material and housing function.
2. Incorrect Material Choice
Choosing the wrong material can ruin your entire project. Some plastics may shrink too much, warp easily, or crack under stress.
Each housing has different needs. For example:
- A medical housing may need biocompatible ABS
- An outdoor device needs UV-stable polycarbonate
- A flexible housing may need polypropylene
Housing Injection Molding requires matching the plastic type to the mold and the product’s use. A smart Mold Maker helps you choose the best material to avoid failures later.
3. Uneven Wall Thickness
Wall thickness must be even throughout the housing. Uneven walls cool at different speeds, which causes warping and internal stress. This weakens the housing and affects the fit of other components.
In Housing Injection Molding, the goal is a uniform wall thickness—ideally between 1.5 mm and 3 mm. The Mold Maker must adjust core and cavity geometry to make the walls consistent.
4. Lack of Draft Angles
Draft angles allow the part to release easily from the mold. Without them, the part sticks, scratches, or even breaks during ejection.
In Housing Injection Molding, even a 1- to 2-degree draft can make a big difference. A professional Mold Maker knows where and how much draft to apply without affecting the final look.
5. Improper Gate Placement
The gate is where molten plastic enters the mold. Poor gate location can cause air traps, weld lines, or sink marks.
If the gate is too far from the flow center, the plastic might not fill completely. If it’s in a visible area, it might leave an ugly mark.
A skilled Mold Maker uses simulation tools to choose the best gate type and location, so the part fills evenly and looks good.
6. Ignoring Cooling Design
Cooling time affects cycle time and part quality. A mold with poor cooling design can cause:
- Warping
- Long cycle times
- Inconsistent part strength
In Housing Injection Molding, cooling channels must be placed evenly around the mold. A smart Mold Maker will design proper water lines and use thermal analysis to make sure the mold cools uniformly.
7. Overlooking Tolerance and Fit
Housings often have snap fits, screw bosses, or mating surfaces. These require precise tolerances to work properly. If tolerances are too tight or too loose, parts won’t fit or will break during assembly.
A Mold Maker with experience in Housing Injection Molding understands how different materials shrink. They build this into the mold design to ensure perfect fits every time.
8. Using Worn or Dirty Molds
Over time, molds wear down. Dirt, rust, or damage can lead to defects like flash, voids, or poor surface finish.
That’s why regular maintenance is critical. A good Mold Maker provides mold cleaning, polishing, and inspection after every production run. This keeps molds in top shape and extends their lifespan.
9. Poor Quality Control
Without regular checks, problems go unnoticed until it’s too late. Defects might not show up until the product reaches the customer.
Housing Injection Molding must include inspections for:
- Size and shape
- Surface finish
- Warpage
- Fit and assembly
The Mold Maker can also build in-process quality features into the mold, like ejector pin marks or parting line designs that signal proper alignment.
10. Rushing Production Before Testing
Some companies skip proper testing to save time. But this often leads to bigger delays later.
Before full production, the mold should go through:
- T1 sampling
- First article inspection
- Trial runs under real conditions
An experienced Mold Maker will guide you through these steps. They ensure the mold works right before mass production begins.
11. Overpacking the Mold
Trying to force more plastic into the mold to improve fill may cause stress or flash. It can even damage the mold over time.
Housing Injection Molding should follow proper pressure, temperature, and fill time settings. These values are fine-tuned during mold trials with the help of the Mold Maker.
12. Lack of Collaboration
One of the biggest mistakes? Not involving the Mold Maker early enough.
Design engineers often create a part design first, then hand it off to a tool shop. But it’s better to work with the Mold Maker during the design phase. They can offer tips on:
- Draft angles
- Wall thickness
- Moldability
- Assembly features
Early feedback can save weeks of redesign later.
Housing Injection Molding is an excellent process for making plastic housings—fast, accurate, and repeatable. But like any process, it’s only as good as the design, materials, and teamwork behind it.
By avoiding common mistakes and working closely with a skilled Mold Maker, companies can improve product quality, cut costs, and speed up production.
The next time you start a new housing project, involve your Mold Maker early. Let their expertise guide your design choices. With the right approach, your Housing Injection Molding project will be a success—every time.