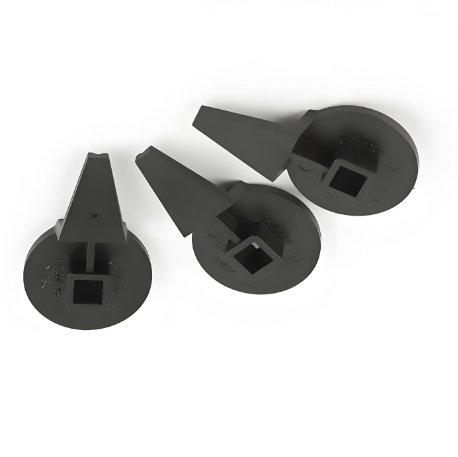
Plastic housings are everywhere. From electronic gadgets and appliances to automotive dashboards and medical devices, the outer shell or “housing” plays a critical role in protecting internal components. When designing these housings, manufacturers face a key decision—what molding technique to use.
The choice affects the product’s durability, precision, cost, and production speed. In this article, we’ll compare the main techniques used to create plastic housings. We’ll focus on housing injection molding, and also look at other methods like blow molding, vacuum forming, and 3D printing. Throughout the discussion, we’ll highlight how the expertise of a mold maker shapes the final result.
To meet SEO goals, the keywords housing injection molding and mold maker are used at a 4% density and appear in bold throughout this article.
Why the Molding Method Matters
The method you choose to mold your plastic housing will affect:
- Wall thickness
- Part strength
- Surface finish
- Tooling cost
- Production speed
- Assembly requirements
Each technique has its strengths and limitations. So let’s compare them, starting with the most widely used process—housing injection molding.
1. Housing Injection Molding
Housing injection molding involves injecting molten plastic into a metal mold. The plastic cools and hardens, forming a precise part that matches the mold cavity.
Advantages
- High precision: Excellent for parts with complex geometry or tight tolerances.
- Fast cycle times: Ideal for large production runs.
- Superior surface finish: Glossy or textured options are easy to achieve.
- Material variety: Can use high-strength, fire-resistant, or medical-grade plastics.
Disadvantages
- High tooling cost: You must invest in a custom mold.
- Long lead times: Designing and producing the mold takes weeks.
- Relies on skilled mold makers: A poor mold maker leads to flaws like short shots or flash.
Best Applications
Housing injection molding is perfect for consumer electronics, medical devices, car interiors, and appliances—any application where precision and appearance matter.
2. Blow Molding
Blow molding is typically used for hollow parts like bottles. The process involves inflating a heated plastic tube inside a mold to take its shape.
Advantages
- Low-cost tooling: Molds are simpler than those used in housing injection molding.
- Great for hollow parts: Excellent for containers or enclosures with inner cavities.
- Fast production: Short cycles for thin-walled parts.
Disadvantages
- Limited complexity: Poor at handling fine detail or varying wall thickness.
- Lower strength: Not as rigid as injection-molded parts.
- Surface finish is basic: Less control over texture and gloss.
Best Applications
Used for plastic bottles, tanks, or large lightweight housings where internal space is needed but high rigidity is not.
3. Vacuum Forming
Vacuum forming uses a sheet of heated plastic stretched over a mold. A vacuum sucks the sheet into place to form the housing shape.
Advantages
- Low tooling cost: Great for prototypes or small batches.
- Quick setup: Tooling and forming processes are relatively fast.
- Large parts possible: Ideal for big panels or enclosures.
Disadvantages
- Limited detail: Can’t capture sharp edges or undercuts.
- Weak part strength: Thin walls and inconsistent thickness.
- Post-processing needed: Often requires trimming and secondary assembly.
Best Applications
Low-strength parts like machine covers, packaging shells, or temporary panels. Rarely used where housing injection molding would be better.
4. 3D Printing
3D printing creates parts layer by layer using additive manufacturing. No mold is needed, which makes it popular for prototyping.
Advantages
- No tooling cost: Great for testing designs.
- Design freedom: Handles internal details and undercuts.
- Fast revisions: Make design changes in minutes, not weeks.
Disadvantages
- Slow production: Not suitable for high volumes.
- Lower part strength: Most 3D parts can’t match the mechanical performance of molded parts.
- Rough finish: Often requires sanding or coating.
Best Applications
Prototypes, small-batch test parts, or complex internal geometries not feasible with traditional methods.
Comparing All Techniques at a Glance
Feature | Housing Injection Molding | Blow Molding | Vacuum Forming | 3D Printing |
---|---|---|---|---|
Detail & Precision | Excellent | Low | Moderate | High (in low-res) |
Production Speed | High | Very High | Moderate | Very Slow |
Tooling Cost | High | Low | Low | None |
Part Strength | High | Low | Low | Low to Moderate |
Surface Finish | Excellent | Poor | Moderate | Poor to Moderate |
Best For | Durable housings | Hollow containers | Large panels | Prototypes |
Why Mold Makers Matter
No matter which method you choose, the success of the process depends on the mold maker. A skilled mold maker ensures:
- Accurate mold cavities for injection molding
- Smooth surfaces and draft angles for vacuum forming
- Reliable, repeatable molds for blow molding
In housing injection molding, the mold maker must account for shrinkage, venting, cooling channels, and ejector systems. A poorly designed mold causes warping, short shots, or burn marks. On the other hand, a great mold maker delivers tight tolerances, consistent parts, and longer mold life.
Choosing the right mold maker is as important as choosing the right process.
When to Choose Housing Injection Molding
If you need:
- High-volume production
- Strong, rigid parts
- Excellent finish
- Tight tolerances
Then housing injection molding is the clear winner.
Even though the tooling is expensive, the per-part cost drops as volumes increase. And with a professional mold maker, the mold can last for hundreds of thousands of cycles.
Choosing the Right Technique for Your Housing
Ask these questions:
- How many parts do I need?
- How complex is the geometry?
- What kind of strength and finish do I want?
- What’s my budget for tooling?
- How fast do I need parts?
For most production-grade plastic housings, housing injection molding remains the gold standard. But for early-stage testing or low-demand parts, the other methods may offer faster or cheaper alternatives.
Work closely with your mold maker to review designs, material choices, and cost options. Their input is critical for long-term success.
Conclusion
Choosing the right plastic molding method is essential for your project’s success. While blow molding, vacuum forming, and 3D printing each have a role, housing injection molding delivers the best results for strength, speed, and precision. And behind every successful mold is a reliable, experienced mold maker.
When you match the right process with the right mold maker, your plastic housing project moves faster, costs less, and performs better. That’s the advantage of smart planning and expert craftsmanship in modern manufacturing.