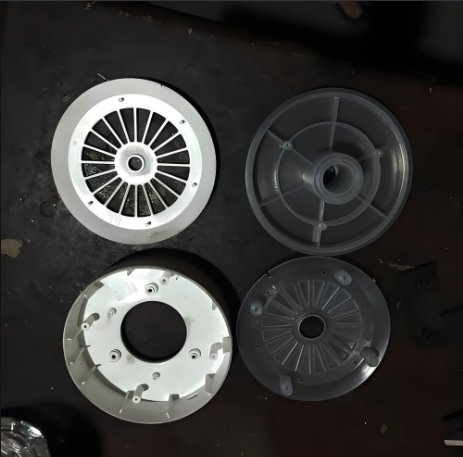
Consumer electronics have become a key part of our daily lives. From smartphones and laptops to smart speakers and tablets, we rely on them for work, play, and communication. But behind every sleek device is a sturdy, precisely shaped plastic housing. These enclosures are made using Housing Injection Molding, a reliable process that delivers both strength and beauty.
To get this right, skilled Mold Makers play a critical role. They design and build the molds that shape the plastic housings into perfect fits for the internal components. This article explains how Housing Injection Molding supports the consumer electronics industry and why an experienced Mold Maker is essential to success.
The Need for Plastic Housings in Consumer Electronics
Consumer electronics must be compact, lightweight, and stylish. At the same time, they need protection against drops, heat, dust, and water. The outer shell — or housing — must meet all these demands.
Here are some common housing types made through Housing Injection Molding:
- Smartphone casings
- Tablet and laptop covers
- TV remote shells
- Gaming console cases
- Speaker housings
- Smartwatch backs
Each item must be both functional and attractive. That’s where Housing Injection Molding excels. It allows the use of custom colors, textures, and finishes while keeping the product durable.
What Is Housing Injection Molding?
Housing Injection Molding is a manufacturing process where molten plastic is injected into a mold to form the exact shape of a housing. The plastic cools and hardens inside the mold, taking on all the design features — curves, textures, holes, and logos.
The benefits of this method include:
- High precision
- Fast production cycles
- Support for mass manufacturing
- Good surface finish
- Minimal waste
For consumer electronics, Housing Injection Molding makes it possible to create attractive, strong, and lightweight parts on a large scale.
The Role of the Mold Maker in Electronics Production
The Mold Maker is the person or team responsible for designing and creating the injection mold. This is the heart of the molding process. A poor mold results in poor housings. A good mold ensures every part meets the strict standards of modern electronics.
The Mold Maker must consider:
- Wall thickness and flow
- Shrinkage rates of plastic
- Positioning of gates and ejectors
- Surface finish requirements
- Tight tolerances
In the electronics industry, even a tiny error in the housing size can cause the internal circuit board not to fit. That’s why precision is vital. An expert Mold Maker will test, adjust, and rework the mold until it performs perfectly.
Plastics Used in Electronic Housings
Not every plastic is suitable for gadgets. Consumer electronics require plastics that are lightweight, durable, and safe. Many devices also need flame-retardant materials. Common choices include:
- ABS (Acrylonitrile Butadiene Styrene) – Strong, easy to mold, and good-looking
- PC (Polycarbonate) – Transparent and very tough
- PC/ABS Blends – Combines strength and surface finish
- PP (Polypropylene) – Resistant to chemicals and flexible
- Nylon (PA) – Heat-resistant and wear-resistant
A skilled Mold Maker understands how each plastic behaves. The mold must be designed with the right shrinkage, cooling, and flow properties for the chosen plastic.
Design Considerations in Housing Injection Molding
Designing a plastic housing involves more than just picking a shape. The engineer and Mold Maker work together to make sure the part is moldable and functional.
Key design points include:
- Uniform wall thickness to avoid warping
- Proper draft angles for easy part release
- Support ribs for added strength
- Snap-fit features for assembly
- Openings for buttons, screens, and ports
Housing Injection Molding allows for fine detail and tight tolerances. This is critical for consumer electronics where design, usability, and durability all matter.
How the Process Works
The Housing Injection Molding process typically follows these steps:
1. Design
CAD software is used to design the part. Simulations may be run to check for flow problems or weak points.
2. Mold Creation
The Mold Maker builds a metal mold, often using high-grade steel. The mold includes cooling channels, ejector pins, and a polished surface.
3. Injection Molding
Plastic pellets are melted and injected into the mold. Once filled, the mold is cooled, and the part is ejected.
4. Quality Check
Each part is inspected for defects like warping, sink marks, or short shots. If needed, the Mold Maker adjusts the mold or process.
This entire flow allows for fast, repeatable production — ideal for the competitive electronics market.
Advantages of Housing Injection Molding for Electronics
Using Housing Injection Molding in electronics offers many key benefits:
- Precision – Small tolerances are no problem
- Speed – Thousands of housings can be made quickly
- Style – Smooth finishes and textures are easy to achieve
- Durability – Parts resist heat, impact, and wear
- Customization – Colors and logos can be molded in
All these advantages depend on the quality of the mold. That’s why the Mold Maker is so important in this process.
Common Challenges and Mold Maker Solutions
Even with advanced machines, problems can occur. Common issues in Housing Injection Molding include:
- Warping – May be caused by uneven cooling
- Flash – Thin plastic leaking out of the mold seam
- Sink marks – Caused by thick areas cooling slowly
- Short shots – When plastic doesn’t fully fill the mold
An experienced Mold Maker can prevent or solve these problems by adjusting the mold design, the plastic material, or the molding settings.
Real-World Examples of Molded Electronic Housings
Here are a few examples of consumer devices that rely on Housing Injection Molding:
- Smartphone bodies with complex curves
- Wireless earbud cases with charging ports
- Game console shells with textured grips
- Router enclosures with venting designs
- Smart home devices with stylish forms
Each one requires perfect fit, finish, and strength — all made possible by precise molds created by expert Mold Makers.
Housing Injection Molding is essential to the consumer electronics industry. It provides the accuracy, repeatability, and design freedom needed to create high-quality housings. From phones to speakers, plastic housings protect internal parts and create the look and feel that users expect.
But none of this happens without a skilled Mold Maker. They are the ones who build the tools that shape each part. Their expertise ensures that the housing performs well in real-world use.
If you want to make reliable, attractive, and high-performance consumer electronics, invest in quality Housing Injection Molding — and work with a trusted Mold Maker who understands your needs.
Would you like this formatted as a downloadable PDF or turned into a brochure layout for marketing use?