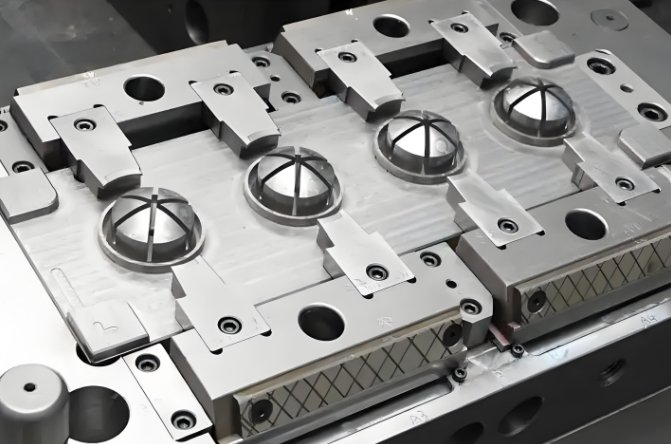
Electronic injection molding is essential for producing electronic components at scale. It ensures consistency, durability, and cost efficiency. However, high-volume production can be expensive. Mold makers play a crucial role in reducing costs while maintaining quality. This article explores cost-effective strategies in electronic injection molding.
1. The Importance of Cost-Effective Electronic Injection Molding
1.1 High-Volume Production Needs
Manufacturers must produce millions of identical parts. Cost control is essential to stay competitive.
1.2 The Role of Mold Makers
Mold makers design precision molds that reduce material waste and production time.
1.3 Impact on Electronics Manufacturing
Affordable production ensures lower prices for consumers while maintaining product reliability.
2. Challenges in High-Volume Electronic Injection Molding
2.1 Expensive Raw Materials
High-performance plastics can be costly. Selecting the right material is crucial.
2.2 Mold Tooling Costs
Creating high-precision molds requires advanced technology, which increases costs.
2.3 Production Efficiency
Slow cycles and defects can raise expenses. Efficient processes lower waste and improve output.
2.4 Energy Consumption
Injection molding machines require significant power. Optimizing energy use reduces costs.
2.5 Quality Control Demands
Defective parts result in losses. Maintaining consistency ensures fewer rejected components.
3. Strategies for Cost-Effective Production
3.1 Material Selection Optimization
Choosing the right plastic improves durability and lowers costs. Common materials include:
- ABS: Cost-effective and durable
- PBT: Ideal for electrical insulation
- LCP: Suitable for micro-components
3.2 Efficient Mold Design
Precision molds minimize material waste and improve cycle times. Mold makers use:
- Multi-cavity molds for higher output
- Hot runner systems to reduce plastic waste
- Optimized cooling for faster cycles
3.3 Automation and Robotics
Robotic systems reduce labor costs and improve efficiency. AI-driven monitoring detects defects early.
3.4 Lean Manufacturing Principles
Streamlining production eliminates unnecessary steps. This reduces costs and improves workflow.
3.5 Energy-Efficient Machines
Modern injection molding machines consume less power while maintaining high precision.
4. Key Applications of Cost-Effective Electronic Injection Molding
4.1 PCB Housings
Durable casings protect circuit boards from damage and environmental factors.
4.2 Connectors and Sockets
Precision molding ensures secure and reliable electrical connections.
4.3 LED Components
High-volume LED production requires efficient molding techniques.
4.4 Consumer Electronics Parts
Smartphone and laptop components demand high precision at low cost.
5. Innovations in Cost-Effective Electronic Injection Molding
5.1 AI-Driven Process Optimization
Machine learning analyzes data to improve efficiency and reduce waste.
5.2 Smart Mold Technology
Real-time sensors monitor mold conditions for better control.
5.3 Recycled Plastics in Injection Molding
Using eco-friendly materials lowers costs and reduces environmental impact.
5.4 3D Printing for Prototype Molds
Rapid prototyping speeds up development and lowers design costs.
6. The Future of Cost-Effective Electronic Injection Molding
6.1 Smaller and More Complex Parts
Miniaturization requires more precise molding techniques.
6.2 Increased Use of Automation
Fully automated factories will improve efficiency and lower labor costs.
6.3 Sustainable Manufacturing Practices
Recyclable materials and energy-saving processes will reduce overall costs.
Electronic injection molding ensures efficient, high-volume production. Mold makers develop advanced molds that reduce waste and improve precision. Cost-effective strategies such as automation, material optimization, and lean manufacturing help lower expenses. As technology evolves, electronic injection molding will continue to improve efficiency and affordability.