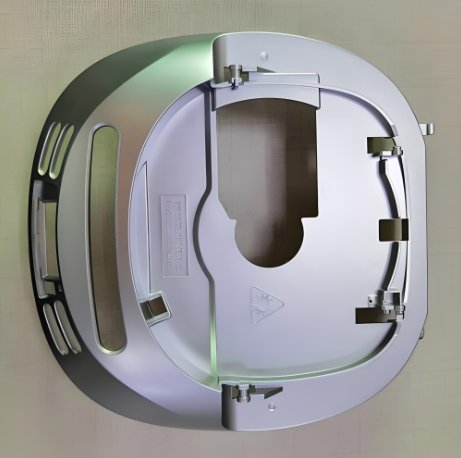
When designing a plastic housing for your product, price is always on your mind. Whether you’re launching an electronic device or packaging a medical tool, the final cost of production matters. Housing injection molding is a reliable and scalable method, but it has many cost factors you should understand. Knowing these details helps you budget smartly and avoid surprises.
A trusted mold maker can explain each stage of cost and help you balance quality, speed, and price. In this article, we’ll explore every key cost factor in housing injection molding. With this knowledge, you can plan your project with confidence.
1. Mold Cost: The First Big Investment
The largest upfront cost in housing injection molding is the mold. A high-quality steel mold can range from a few thousand to tens of thousands of dollars. The price depends on:
- Size and complexity of the housing
- Number of mold cavities
- Material of the mold (steel or aluminum)
- Mold life expectancy (prototype vs. production)
- Custom features like sliders or inserts
Your mold maker will design and machine this mold, usually from hardened steel like P20 or H13. These materials last long and offer precision, but cost more. Choosing the right mold maker ensures that the mold is reliable, accurate, and efficient in the long run.
2. Part Complexity and Design Features
The shape and features of your housing greatly affect the cost. Simple box shapes are cheaper to mold. However, the following features raise the price:
- Thin walls
- Complex undercuts
- Snap-fits or clip systems
- Cosmetic finishes
- Tight tolerances
Each added detail requires more time in design, machining, and molding. Your mold maker may need to add lifters, cores, or slides to produce these features, which increases both mold and cycle time.
Designing with manufacturing in mind is key. Ask your mold maker for DFM (Design for Manufacturing) feedback early. This helps reduce part cost without sacrificing quality.
3. Mold Cavities: Single or Multi?
How many parts will you need? A single-cavity mold makes one part per cycle. It’s cheaper to build but slower for large orders. A multi-cavity mold produces more parts per shot, which boosts efficiency.
For example:
- Single-cavity mold: lower tooling cost, slower output
- 4-cavity mold: higher tooling cost, faster production
Your mold maker can help balance upfront cost with production volume. If you expect high demand, multi-cavity molds offer better long-term savings for your housing injection molding project.
4. Material Selection
The type of plastic you choose also affects cost. Some resins are more expensive due to their properties or availability. Common choices for plastic housings include:
- ABS (cost-effective and easy to mold)
- PC (strong and impact-resistant)
- Nylon (durable but moisture-sensitive)
- PP (flexible and chemical-resistant)
- PC+ABS blends (best of both worlds)
High-performance materials for medical or automotive use will raise your cost. Your mold maker can help you pick a resin that meets both performance and budget goals. Also, don’t forget that color matching or UV resistance adds to the cost.
5. Cycle Time: Speed Matters
Cycle time means the time it takes to mold one shot of parts. In housing injection molding, cycle time depends on:
- Wall thickness
- Cooling time
- Part ejection speed
- Material flow characteristics
Faster cycles reduce cost per part. Your mold maker designs the mold and selects parameters to optimize this speed. Well-designed cooling channels and proper gate locations can shave seconds off each cycle, saving money across thousands of parts.
6. Quantity of Parts
Volume plays a huge role in total cost. As quantity increases, the per-part cost decreases. Here’s why:
- Fixed tooling cost gets spread over more parts
- Bulk raw materials are cheaper
- Setup and labor costs get divided among more units
If you’re ordering a small batch of 500–1,000 housings, your cost per part will be high. But if you order 100,000 units, the cost drops significantly. Talk to your mold maker about order size and whether batch production is a good option.
7. Tolerance and Quality Requirements
Some housings need to fit tightly with internal components. Others must look flawless on the outside. Tighter tolerances or cosmetic requirements raise the cost.
Your mold maker will use higher-precision equipment, slower machining, and possibly better mold materials to meet your specs. This means more time and cost. Be sure to define your tolerances clearly and only demand tight specs where truly necessary.
8. Secondary Operations
After molding, some parts require extra steps:
- Trimming or deburring
- Painting or coating
- Pad printing or laser marking
- Assembly or ultrasonic welding
- Surface texturing
Each adds time and labor, which affects the final price. In housing injection molding, keep designs simple and complete in one shot when possible. Discuss with your mold maker which operations can be avoided or streamlined.
9. Shipping and Packaging
If you’re working with a mold maker overseas, shipping cost becomes important. Heavy steel molds are expensive to ship. Molded parts may also need protective packaging to avoid damage.
Air freight is fast but costly. Sea freight is slower but cheaper. Make sure your project timeline includes shipping time and customs clearance. Your mold maker should guide you on the best shipping method based on your budget and urgency.
10. Mold Maintenance and Repair
Molds are an investment. Over time, they need cleaning, polishing, and repair. A good mold maker provides a maintenance plan to keep your mold running smoothly.
If your housing is in mass production, poor maintenance can cause defects or slow production. Always factor in the long-term care cost of your tooling. Some mold makers offer lifetime maintenance if the molding is done in-house.
How to Control Costs in Housing Injection Molding
Here are some smart ways to manage your budget:
- Choose experienced mold makers with in-house tooling and molding
- Approve DFM feedback early to avoid redesigns
- Avoid cosmetic features unless necessary
- Pick materials that match your part needs
- Order in higher volumes to lower unit cost
- Consider soft tooling for small runs or prototypes
- Use clear communication to avoid costly mistakes
Conclusion
Many factors affect the cost of housing injection molding, from mold design to final delivery. Working with a skilled mold maker gives you clarity, accuracy, and support through every step. Understanding what drives the cost helps you make better decisions and get the best value.
Whether you’re producing hundreds or millions of parts, balancing cost with quality is key. Don’t just look at the price tag—consider the full picture. A smart budget starts with a great mold maker who cares about your product as much as you do.