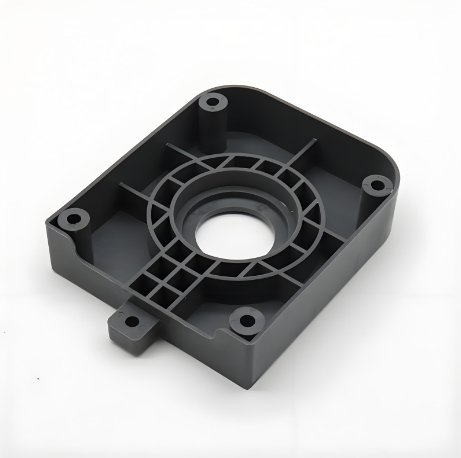
In today’s market, electronics are not just judged by how they work. Their appearance matters just as much. Sleek, stylish designs can make a device stand out from the competition. That is why creating aesthetic finishes for electronic housings is so important.
Using Electronic Injection Molding and the expertise of a skilled Mold Maker, manufacturers can achieve surfaces that are beautiful, durable, and functional. Let’s explore how this process shapes the look and feel of modern electronics.
The Role of Electronic Injection Molding in Surface Quality
Electronic Injection Molding is key when it comes to creating the outer shells of devices. It offers precise control over the shape, texture, and color of parts. The Mold Maker designs the mold carefully to capture every tiny detail.
From smooth high-gloss finishes to textured, matte looks, Electronic Injection Molding makes it possible to meet any design goal. With exact pressure and temperature control, parts come out looking sharp and professional every time.
How Mold Makers Shape the Final Appearance
The Mold Maker plays a huge role in the final finish of any molded part. They create the mold’s surface texture and polish, which transfers directly to the plastic part.
Here’s how a Mold Maker affects the finished product:
- Polished Surfaces: For glossy, mirror-like housings, molds are polished to a very fine level.
- Textured Surfaces: To create a soft-touch or rugged look, the mold surface is etched or sandblasted.
- Patterned Designs: Advanced molds can include patterns like leather, carbon fiber, or geometric shapes.
A well-trained Mold Maker knows how to balance beauty with function, ensuring the part also resists scratches, fingerprints, and wear.
Techniques for Achieving Aesthetic Finishes
There are several key techniques used during Electronic Injection Molding to create attractive finishes. Each depends on good materials, careful processing, and expert Mold Maker skills.
1. Mold Texturing
Mold texturing is a popular method. The Mold Maker treats the mold surface with chemical etching or laser engraving. This creates textures that hide fingerprints, improve grip, or just make the part look more appealing.
Textured finishes are widely used in:
- Smartphones
- Game controllers
- Remote controls
- Wearable devices
2. High-Gloss Finishing
For glossy products, the Mold Maker polishes the mold to a mirror finish. During Electronic Injection Molding, the plastic replicates this shine exactly.
This method is common for premium devices where a sleek, elegant look is needed.
3. Soft-Touch Coatings
Sometimes, after molding, a soft-touch coating is applied. These coatings feel smooth and rubbery, adding comfort and style.
Even though the coating happens later, the Electronic Injection Molding must produce a flawless base part first. A skilled Mold Maker ensures the surface is ready for coating without extra sanding or prep.
4. Color Integration
With Electronic Injection Molding, color can be built directly into the plastic. No painting needed!
This makes parts more durable because the color won’t chip or scratch off. Special effects like metallic looks, pearlescent finishes, or color gradients can also be molded in.
5. In-Mold Decoration (IMD)
In-Mold Decoration involves placing a printed film inside the mold before injecting the plastic. When the plastic forms, it bonds to the film.
This allows high-quality graphics, logos, or patterns to become part of the housing. The Mold Maker must prepare the mold carefully to position and bond the film correctly.
Material Choices Impact Finish Quality
Choosing the right material is critical for both appearance and durability. Popular plastics for attractive housings include:
- ABS: Easy to mold, polish, and color. Great for consumer electronics.
- Polycarbonate (PC): High strength and clarity. Used in premium devices.
- PC/ABS Blends: Combine beauty and toughness.
- Liquid Silicone Rubber (LSR): Used for soft, flexible parts.
The Mold Maker must design the mold to suit the chosen material’s flow, shrinkage, and cooling needs during Electronic Injection Molding.
Challenges in Creating Beautiful Electronic Housings
Achieving perfect finishes is not easy. Many challenges can appear, including:
- Flow Lines: Visible streaks where plastic flows meet.
- Sink Marks: Small dents caused by uneven cooling.
- Weld Lines: Thin lines where two flows of plastic join.
- Color Variation: Differences in shade from part to part.
An experienced Mold Maker helps solve these problems through smart mold design. Proper gate placement, balanced flow paths, and fine temperature control during Electronic Injection Molding are critical.
Applications of Aesthetic Electronic Housings
Beautiful finishes are needed across many markets:
- Smartphones and tablets
- Laptops and keyboards
- Gaming consoles
- Medical devices
- Smart home products
In each case, the combination of Electronic Injection Molding technology and skilled Mold Maker work ensures the final product looks and feels just right.
Future Trends in Aesthetic Finishes
The future of device housings is even more exciting. New trends include:
- Self-healing materials: Plastics that repair small scratches on their own.
- Color-Shifting Effects: Parts that change color with light or temperature.
- Sustainable Materials: Beautiful finishes made from recycled plastics.
- Micro-Textures: Ultra-fine patterns for unique looks and enhanced feel.
Mold Makers will continue to be at the center of these trends, using their skills to craft molds that enable these futuristic finishes through Electronic Injection Molding.
In today’s competitive electronics world, looks matter just as much as performance. Creating aesthetic finishes for electronic housings requires the perfect blend of advanced Electronic Injection Molding techniques and the expertise of a talented Mold Maker.
From high-gloss surfaces to rugged textures, from bright colors to in-mold decorations, the possibilities are endless. With good material selection, careful mold design, and precise control of the molding process, beautiful and durable housings become reality.
As new trends emerge, manufacturers who invest in excellent Electronic Injection Molding and experienced Mold Maker services will continue to lead the market, delighting customers with products that look as good as they perform.