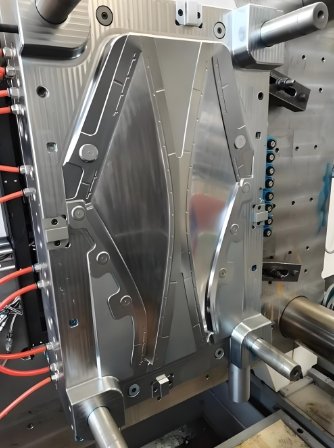
Every vehicle is unique. Custom automotive injection molds help manufacturers create precise parts. A skilled mold maker ensures accuracy and durability. Customization improves design, function, and aesthetics.
Why Custom Automotive Injection Molds Matter
1. Enhancing Vehicle Design
Custom automotive injection molds allow for unique designs. A mold maker ensures every detail is perfect.
2. Improving Functionality
Cars need precise parts. Custom automotive injection molds enhance performance. A mold maker guarantees quality.
3. Increasing Production Efficiency
Tailored molds improve production speed. Automotive injection molds reduce defects. A mold maker optimizes designs.
4. Reducing Manufacturing Costs
Custom molds minimize waste. Automotive injection molds save material. A mold maker improves efficiency.
Key Features of Custom Automotive Injection Molds
1. High-Precision Engineering
Small errors cause big problems. Automotive injection molds require accuracy. A mold maker ensures flawless production.
2. Advanced Cooling Systems
Faster cooling reduces cycle time. Automotive injection molds with optimized cooling improve efficiency. A mold maker designs better channels.
3. Multi-Cavity Configurations
More cavities mean higher output. Automotive injection molds increase production. A mold maker creates efficient layouts.
4. Strong and Durable Materials
Molds must withstand high pressure. Automotive injection molds use steel or aluminum. A mold maker selects the best material.
Types of Custom Automotive Injection Molds
1. Single-Cavity Molds
These molds create one part per cycle. Automotive injection molds for prototypes use this. A mold maker ensures accuracy.
2. Multi-Cavity Molds
These molds produce multiple parts at once. Automotive injection molds improve efficiency. A mold maker reduces costs.
3. Family Molds
Different parts come from one mold. Automotive injection molds save resources. A mold maker ensures compatibility.
4. Insert Molds
Metal and plastic combine in these molds. Automotive injection molds create hybrid parts. A mold maker enhances durability.
Materials Used in Custom Automotive Molds
1. Hardened Steel
This material lasts the longest. Automotive injection molds need durability. A mold maker selects hardened steel for longevity.
2. Aluminum
Aluminum molds cool fast. Automotive injection molds for prototypes benefit from speed. A mold maker chooses aluminum for testing.
3. High-Performance Polymers
Plastic molds work for some applications. Automotive injection molds sometimes use composite materials. A mold maker balances cost and strength.
Advanced Technologies in Custom Automotive Injection Molding
1. CNC Machining for Precision
CNC machines cut with accuracy. Automotive injection molds achieve perfect detail. A mold maker programs machines for efficiency.
2. 3D Printing for Rapid Prototyping
3D printing speeds up testing. Automotive injection molds improve with rapid iteration. A mold maker verifies designs before production.
3. Hot Runner Systems
Hot runners reduce waste. Automotive injection molds use them for efficiency. A mold maker optimizes material flow.
4. AI-Driven Mold Optimization
AI improves mold design. Automotive injection molds become more efficient. A mold maker uses data-driven enhancements.
The Role of a Mold Maker in Custom Automotive Manufacturing
1. Designing Custom Solutions
Each project needs specific molds. Automotive injection molds require precision. A mold maker tailors designs to fit needs.
2. Optimizing Mold Performance
Molds wear down over time. Automotive injection molds need regular maintenance. A mold maker extends lifespan with improvements.
3. Ensuring Consistent Quality
Every part must be identical. Automotive injection molds guarantee accuracy. A mold maker ensures defect-free production.
4. Reducing Production Costs
Better designs lower expenses. Automotive injection molds optimize resource use. A mold maker saves time and money.
Applications of Custom Automotive Injection Molds
1. Interior Components
Seats, dashboards, and panels use plastic. Automotive injection molds shape these. A mold maker ensures precision.
2. Exterior Parts
Bumpers, grilles, and trims need strong molds. Automotive injection molds handle large components. A mold maker ensures durability.
3. Engine and Under-the-Hood Parts
Heat-resistant plastics are essential. Automotive injection molds create air ducts and covers. A mold maker selects high-performance materials.
4. Lighting and Electrical Components
Headlights and electrical housings need clarity. Automotive injection molds shape these parts. A mold maker ensures accuracy.
Future Trends in Custom Automotive Injection Molding
1. Lightweighting for EVs
Electric cars need lighter parts. Automotive injection molds produce thin-walled components. A mold maker balances weight and strength.
2. Sustainable Materials
Recycled plastics will grow. Automotive injection molds will use more eco-friendly materials. A mold maker will reduce waste.
3. Fully Automated Manufacturing
Automation increases efficiency. Automotive injection molds will rely on robotics. A mold maker will integrate smart systems.
4. AI-Driven Mold Design
AI helps detect flaws. Automotive injection molds will improve with predictive analysis. A mold maker will enhance precision.
Custom automotive injection molds shape modern vehicles. A skilled mold maker ensures accuracy, efficiency, and cost savings. Future advancements will make molds even better.