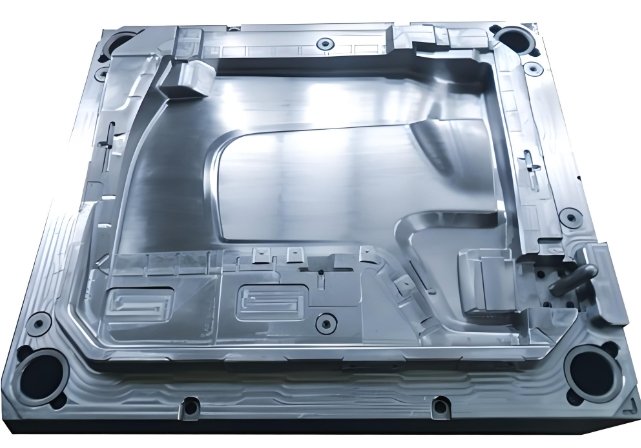
Every vehicle has unique design needs. Automotive Injection Molds play a vital role in achieving those needs. They produce precise parts for customized designs. Skilled Mold Makers craft these molds for quality and efficiency. This process supports creative freedom in the automotive industry.
Why Choose Custom Automotive Injection Molds
1. Tailored Solutions
Custom molds meet specific design requirements.
2. Enhanced Aesthetics
Unique designs improve vehicle appearance.
3. Perfect Fit
Custom molds ensure accurate dimensions.
4. Durable Components
High-quality molds create lasting parts.
Applications of Custom Molds
1. Interior Panels
Custom molds shape door panels and dashboards.
2. Exterior Parts
Grilles, bumpers, and trims require unique designs.
3. Lighting Housings
Custom molds ensure sleek headlight designs.
4. Engine Covers
Precise molds improve engine component alignment.
The Role of the Mold Maker
1. Design Expertise
Mold Makers create designs to match client needs.
2. Material Knowledge
Selecting the right material ensures durability.
3. Advanced Tools
High-precision machines deliver accurate results.
4. Prototyping and Testing
Every mold undergoes thorough testing.
Advantages of Custom Automotive Injection Molds
1. Design Freedom
Custom molds support creativity.
2. Consistency
Parts maintain uniformity across production.
3. Cost Savings
Durable molds reduce long-term expenses.
4. Sustainability
Custom designs minimize material waste.
Challenges in Custom Mold Production
1. Complex Designs
Unique shapes require advanced molding techniques.
2. Material Compatibility
The mold must match the part’s material.
3. Time Constraints
Custom molds may take longer to produce.
4. High Precision Needs
Molds must meet tight tolerances.
Steps in Crafting Custom Molds
1. Initial Consultation
Understand the client’s vision.
2. Design Development
Create 3D models of the mold.
3. Material Selection
Choose materials for durability and efficiency.
4. Prototyping
Produce and test a prototype mold.
5. Production
Manufacture the final mold using advanced tools.
6. Quality Assurance
Test the mold to ensure it meets all requirements.
Innovations in Custom Mold Technology
1. 3D Printing
Speeds up prototyping.
2. Smart Sensors
Enhance mold monitoring.
3. Sustainable Materials
Eco-friendly mold options are now available.
4. Advanced Cooling Systems
Improves production efficiency.
Custom Molds for Key Automotive Systems
1. Infotainment Frames
Molds create bezels for screens and control panels.
2. Safety Equipment
Custom molds shape airbag components and crash pads.
3. Energy Solutions
Battery casings and EV chargers rely on custom designs.
4. Comfort Features
Switch panels and cup holders require precision.
Trends in Custom Mold Manufacturing
1. AI Integration
Optimizes mold designs.
2. Eco-Friendly Processes
Supports sustainable production.
3. Miniaturization
Smaller parts need precise molds.
4. Automation
Speeds up mold production.
Custom Automotive Injection Molds revolutionize automotive design. They ensure precision, quality, and creativity. Skilled Mold Makers bring unique designs to life. Investing in custom molds enhances vehicle aesthetics and functionality. This drives innovation in the automotive industry.