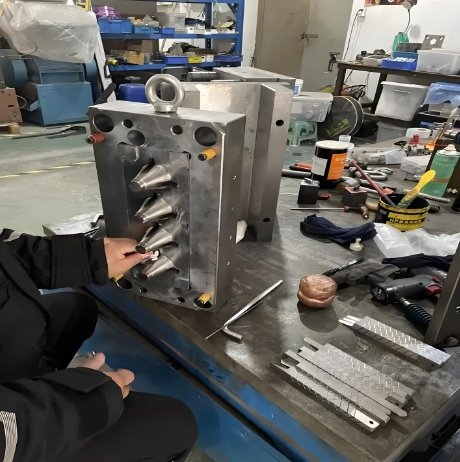
In Electronic Injection Molding, every product is different.
Every design has its own challenges.
Some electronic products need special molds.
A custom mold ensures precision and quality.
A good Mold Maker knows how to create molds that meet these needs.
Let’s look at the role of custom molds in Electronic Injection Molding.
Why Custom Molds Are Essential for Electronics
Electronic products come in many shapes and sizes.
Each one needs a specific mold to work right.
Standard molds often don’t fit.
They can’t handle the complexity of some parts.
A custom mold is built to match the unique needs of the product.
1. Precision and Accuracy
Electronic Injection Molding demands high precision.
Parts like connectors and sensors need tight tolerances.
A custom mold is designed to meet these requirements.
It ensures parts are made to exact specifications.
2. Complex Geometries
Many electronic parts have intricate shapes.
A standard mold may not work.
Custom molds are designed for complex geometries.
They can handle thin walls, deep cavities, and small details.
3. Material Compatibility
Electronics often use special materials.
These materials require specific molding techniques.
A custom mold can be adjusted to work with these materials.
It helps avoid defects like warping or poor finish.
The Role of the Mold Maker in Custom Design
A skilled Mold Maker plays a big part in custom mold designs.
They take the product design and translate it into a functional mold.
The Mold Maker works closely with engineers.
They also work with material scientists to find the best options.
1. Design Considerations
The Mold Maker considers many factors.
They think about part geometry, material flow, and cooling.
They also look at mold durability and ease of maintenance.
These factors ensure long-lasting, high-quality molds.
2. Precision Engineering
The Mold Maker uses advanced tools and software.
They create detailed designs using CAD (Computer-Aided Design).
These designs allow for accurate mold creation.
It ensures that every part is produced to specification.
3. Prototyping and Testing
Before finalizing the mold, the Mold Maker creates prototypes.
These prototypes are tested for fit, function, and quality.
Any issues are fixed before moving to full production.
Custom Molds for Different Electronic Products
1. Connectors and Terminals
Connectors are small but crucial in electronics.
They need precise dimensions to fit well.
A custom mold ensures these connectors work perfectly.
The mold also helps avoid defects like flash or sink marks.
2. Enclosures and Housings
Electronic devices need strong, protective enclosures.
A custom mold creates these parts with high accuracy.
It also ensures that the plastic flows properly, especially in complex shapes.
3. Displays and Lens Covers
Displays, buttons, and lens covers require smooth finishes.
A custom mold is designed to create smooth surfaces.
This helps in making transparent parts or parts with high gloss.
4. Small Components and Sensors
Tiny parts like sensors need high precision.
They also need strong materials that can withstand heat.
A custom mold is used to create these sensitive components.
It ensures minimal distortion during production.
Benefits of Custom Molds in Electronic Injection Molding
1. Higher Quality Parts
Custom molds ensure every part meets exact specifications.
This leads to better fitting, stronger, and more reliable products.
In Electronic Injection Molding, quality is key.
2. Reduced Defects
Custom molds reduce defects like warping or short shots.
They also minimize waste by controlling material flow.
This results in fewer rejects and reworks.
3. Increased Efficiency
With a custom mold, the molding process is more efficient.
The mold is designed to minimize cycle time and reduce downtime.
This makes the entire production process faster.
4. Cost Savings in the Long Run
Though custom molds may cost more upfront, they save money over time.
They produce more parts per cycle and reduce waste.
In high-volume runs, these savings add up.
5. Better Material Control
Custom molds allow for better material flow control.
This is especially important for high-performance plastics.
It helps achieve consistent product quality.
How Custom Mold Design Impacts Production Time
Custom molds can help reduce production time.
This is because they are designed specifically for the part.
With better mold flow and temperature control, parts are made faster.
There is less cooling time, and no extra material waste.
A Mold Maker also ensures that the mold is easy to maintain.
This reduces downtime for cleaning and repairs.
The Process of Creating a Custom Mold
The process starts with understanding the part design.
Engineers and the Mold Maker discuss the material and production needs.
They consider part geometry, volume, and tolerance levels.
Once the design is understood, CAD models are made.
These models show the mold’s features and part cavities.
The Mold Maker uses these models to build the mold.
After the mold is built, a prototype is tested.
The prototype is inspected for quality, fit, and functionality.
Any issues found are corrected before full-scale production.
Mold Materials for Custom Designs
Molds for Electronic Injection Molding are often made from high-strength steel.
This material ensures durability and resistance to wear.
Mold Makers may use materials like H13 or S136.
These materials are tough and can handle high temperatures.
Sometimes, other materials like aluminum are used for lower-volume jobs.
These are less expensive but may not last as long.
The Mold Maker decides based on your needs and budget.
Challenges in Custom Mold Design
Creating custom molds is not always easy.
The Mold Maker faces challenges like:
- Complex part shapes
- Material compatibility
- Tight tolerance requirements
- High-volume production needs
Each challenge must be handled carefully.
The Mold Maker must plan for these issues during the design phase.
They use simulations and testing to predict potential problems.
In Electronic Injection Molding, custom molds are essential.
They ensure precision, reduce defects, and improve efficiency.
A skilled Mold Maker plays a critical role in creating these molds.
They design and build molds that meet the specific needs of each electronic part.
Whether it’s a connector, housing, or small sensor, custom molds ensure high-quality products.
They also help in saving time and reducing costs in the long run.
If you need custom mold designs, working with an experienced Mold Maker is key.
They will deliver molds that perform perfectly, every time.