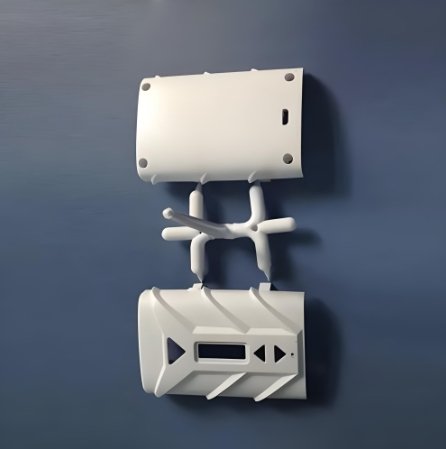
In Electronic Injection Molding, accuracy is everything. Parts must fit perfectly. Small errors can cause big problems. That’s why precision mold design is so important. A skilled Mold Maker makes it possible.
Why Precision Matters in Electronics
Electronic parts are small. Very small. Even tiny size errors can cause failure. Precision ensures that each molded part works as it should. That’s the goal of Electronic Injection Molding. And it all starts with the mold.
Role of the Mold Maker
The Mold Maker builds the mold. But they do much more than that. They design, test, and refine it. They study the product needs. They understand how plastic flows. They choose the right steel. And they make sure the mold lasts long and works well.
Understanding Part Design
Before designing the mold, the part design must be clear. Wall thickness. Sharp corners. Tolerances. Mounting holes. All of these must be reviewed. The Mold Maker works with the design team. They find problems early. They fix them before the mold is made.
Material Selection
Material choice is key in Electronic Injection Molding. Some plastics shrink more. Others are heat-sensitive. Some offer better stability. The Mold Maker chooses the best match. This helps control size, shape, and performance. It also helps meet ESD, flame, and strength needs.
Choosing the Right Mold Material
Molds must be strong and stable. For high-precision parts, tool steel is often best. It resists wear. It holds tight tolerances. Sometimes aluminum is used for faster prototyping. The Mold Maker chooses based on life, cost, and part requirements.
Mold Design Basics
Every mold has key parts: cavity, core, runner, and gate. For precise molding, each must be exact. The Mold Maker controls size, shape, and location. They prevent warping, short shots, or flash.
Parting Line Accuracy
The parting line is where the mold splits. If this is off, the part will have flash or misalignment. A good Mold Maker designs this line carefully. They make sure it seals tightly. This keeps the molded part accurate and clean.
Gate Design
The gate controls how plastic enters the mold. Gate size and location affect flow. Poor gate design causes voids, stress, or warping. The Mold Maker selects the right gate type. Hot tip, submarine, edge, or pinpoint — each has a role in Electronic Injection Molding.
Runner Design for Uniform Flow
Runners guide the molten plastic to each cavity. Uneven runners cause poor fill or part defects. A balanced runner system keeps flow steady. The Mold Maker uses software and skill to make it right.
Cooling System Precision
Cooling affects the size and quality of molded parts. Poor cooling causes warping or shrinkage. A good Mold Maker adds channels to cool evenly. Baffles, bubblers, and inserts can help. Precision cooling helps with dimensional control.
Venting for Defect-Free Parts
Air must escape as plastic enters the mold. If it doesn’t, it creates bubbles or burn marks. The Mold Maker adds tiny vents. These let air out without leaking plastic. Proper venting is vital in Electronic Injection Molding.
Tolerance Control
Electronic parts need tight tolerances. Often within microns. The Mold Maker uses fine EDM tools and grinding. CNC machines hold size closely. Surface finish also matters. A smooth surface ensures parts fit and seal properly.
Mold Flow Analysis
Before cutting steel, the mold design is tested. Mold flow software simulates how plastic will move. The Mold Maker checks fill time, pressure, and cooling. This reduces risk. It saves time and money. It’s a smart step in Electronic Injection Molding.
Testing with Prototypes
Sometimes a prototype mold is made first. This mold may be aluminum or soft steel. It helps test fit and function. The Mold Maker uses these trials to improve the final mold. This ensures better performance later.
Mold Alignment
A precision mold must close perfectly. The Mold Maker uses guide pins, bushings, and locks. These keep the mold aligned. Poor alignment causes flash or wear. Alignment helps each shot stay perfect.
Mold Maintenance Planning
Even a perfect mold will wear over time. The Mold Maker plans for easy maintenance. Inserts can be changed. Slides can be cleaned. This keeps the mold working well during long production runs.
Overmolding Designs
Some electronic parts have more than one material. Like a soft grip over a hard body. This is called overmolding. The Mold Maker designs two-stage molds. These molds fit together perfectly. They allow one part to mold over the other.
Insert Molding Features
Insert molding adds metal or pre-made parts inside the plastic. Like connectors or pins. The Mold Maker designs special slots or guides. These hold the insert in place. Insert molding is common in Electronic Injection Molding.
Reducing Shrinkage
All plastics shrink as they cool. Shrinkage affects part size. The Mold Maker studies the material’s shrink rate. They adjust the mold size. This ensures the part stays accurate after cooling.
Preventing Warpage
Warping happens when parts cool unevenly. The Mold Maker designs the mold to cool evenly. They avoid sharp corners. They balance wall thickness. This helps parts come out flat and true.
Quality Inspection and Trial Runs
Once the mold is built, it goes through trial runs. The Mold Maker checks sample parts. They look for flash, short shots, sink marks, and warpage. Any problems are fixed before full production.
Collaboration with Engineers
The Mold Maker works closely with engineers. They discuss design, function, and materials. They review drawings and goals. This teamwork ensures that the mold meets every need.
Final Validation
Before final use, the mold goes through validation. This includes multiple test runs. Dimensions, strength, and fit are all checked. Only after passing tests does production begin. The Mold Maker ensures the mold is ready.
In Electronic Injection Molding, the mold makes the difference. High-precision components need perfect molds. A skilled Mold Maker designs with care. They control every detail. From material choice to mold alignment, their work ensures success.
By focusing on quality, accuracy, and planning, they help create electronic parts that last longer and perform better. Precision molding starts with a precise mold. And that’s what a good Mold Maker delivers.