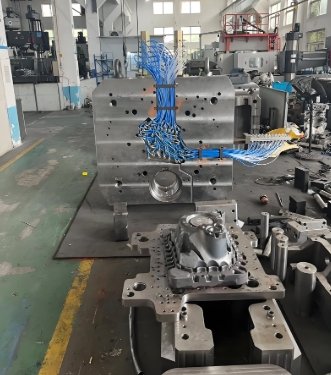
Durability is essential for automotive components. Automotive Injection Molds must withstand long production cycles. Skilled Mold Makers ensure molds last. They design molds for efficiency and strength. High-quality molds reduce downtime and costs.
The Importance of Durability in Injection Molds
1. High-Volume Production
Automotive manufacturing requires large quantities. Durable molds handle repeated use.
2. Cost Savings
Long-lasting molds reduce replacement costs.
3. Consistent Quality
Durable molds ensure every part meets standards.
4. Reduced Downtime
Reliable molds minimize maintenance interruptions.
Materials for Durable Automotive Injection Molds
1. Hardened Steel
Best for long production runs. Resistant to wear and tear.
2. Stainless Steel
Combines strength and corrosion resistance.
3. Aluminum
Lightweight and cost-effective. Ideal for prototyping.
4. Beryllium Copper
Excellent for heat transfer. Enhances mold cooling.
Design Features That Improve Mold Durability
1. Reinforced Cavities
Prevents deformation under pressure.
2. Optimized Cooling Channels
Keeps molds from overheating.
3. Surface Treatments
Coatings reduce wear and extend lifespan.
4. Precision Engineering
Reduces stress on critical components.
The Role of the Mold Maker in Ensuring Durability
1. Material Selection
Mold Makers choose materials suited to production needs.
2. Advanced Techniques
Skilled Mold Makers use precision machining.
3. Regular Testing
Ensures molds meet durability standards.
4. Continuous Improvement
Feedback helps Mold Makers refine designs.
Benefits of Durable Automotive Injection Molds
1. Increased Efficiency
Long-lasting molds run for extended periods.
2. Lower Costs
Fewer replacements save money over time.
3. Improved Reliability
Durable molds produce consistent parts.
4. Sustainability
Fewer discarded molds reduce environmental impact.
Applications of Durable Molds in Automotive Manufacturing
1. Engine Components
Molds create strong, heat-resistant parts.
2. Interior Panels
Durable molds handle detailed designs.
3. Exterior Features
Bumpers and grilles need robust molds.
4. Lighting Systems
Precision molds shape durable housings.
Challenges in Creating Durable Molds
1. Material Costs
High-quality materials are expensive.
2. Complex Designs
Durability must not compromise part design.
3. Production Demands
Intense use can strain even durable molds.
Innovations for Long-Lasting Automotive Injection Molds
1. 3D Printing for Prototypes
Speeds up testing and refinement.
2. Advanced Coatings
Increases resistance to wear and heat.
3. Smart Monitoring Systems
Sensors detect stress in real-time.
4. Hybrid Mold Designs
Combines multiple materials for better performance.
Steps to Prolong Mold Life
1. Regular Maintenance
Clean and inspect molds after each use.
2. Proper Storage
Protects molds from damage during downtime.
3. Operator Training
Ensures proper use to prevent damage.
4. Scheduled Repairs
Addresses minor issues before they escalate.
Cost Analysis of Durable Molds
1. Initial Investment
High-quality molds cost more upfront.
2. Long-Term Savings
Durable molds reduce replacement frequency.
3. Productivity Gains
Reliable molds keep production running smoothly.
4. Environmental Impact
Fewer discarded molds mean less waste.
Future Trends in Durable Mold Design
1. Sustainable Materials
More manufacturers are using recycled metals.
2. Automation Integration
Advanced machines build more precise molds.
3. Custom Solutions
Tailored designs meet specific production needs.
4. Data-Driven Improvements
AI helps optimize durability and performance.
Durable Automotive Injection Molds are crucial. They ensure efficient, cost-effective production. Skilled Mold Makers use advanced techniques to build long-lasting molds. These molds support high-volume manufacturing with consistent quality. Investing in durable molds saves money and boosts reliability. As technology evolves, molds will become even more durable and sustainable. Reliable molds are the backbone of automotive innovation.