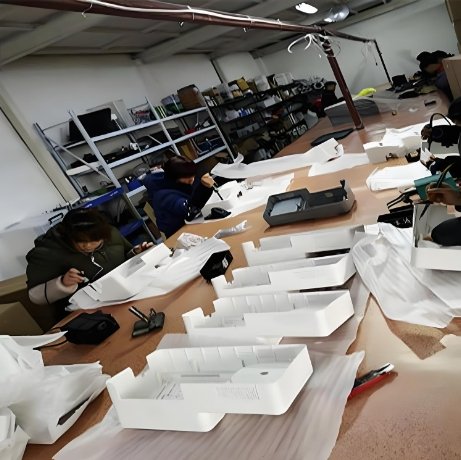
The world is changing.
More people care about the planet.
Factories must change too.
Electronic Injection Molding is no different.
It needs to go green.
That means using eco-friendly plastics.
And working with a smart Mold Maker.
What Are Eco-Friendly Plastics?
Eco-friendly plastics are better for nature.
They break down faster.
They release fewer toxins.
They use less fossil fuel.
Some come from plants.
Some are recycled.
Some are made to degrade over time.
In Electronic Injection Molding, that’s a big deal.
Because electronic parts often get thrown out.
Using greener plastics helps reduce waste.
Why Go Green in Electronic Injection Molding?
Electronic waste is growing fast.
Old phones, computers, and gadgets pile up.
Many end up in landfills.
Using eco plastics reduces harm.
It makes products safer.
And shows responsibility.
Buyers care too.
They want green products.
They ask companies to act.
That’s why smart Mold Makers are changing.
They support eco-friendly projects.
They test new materials.
And build better molds.
Common Types of Green Plastics
Many types of eco plastics are available now.
Each works for different needs.
A skilled Mold Maker chooses the right one.
1. PLA (Polylactic Acid)
Made from corn or sugarcane.
Biodegradable.
Works well for light parts.
2. Bio-PE (Bio-Polyethylene)
Comes from sugarcane.
Strong like regular PE.
Used in housings and cases.
3. Recycled ABS
Made from old plastics.
Saves resources.
Used in large electronic parts.
4. PHA (Polyhydroxyalkanoates)
Biodegradable.
Good for disposable items.
Still expensive.
5. Biodegradable PC or PET Blends
Used in strong, clear parts.
Some blends now offer greener versions.
Role of the Mold Maker
A Mold Maker plays a big part.
They make the tools.
They shape the parts.
Eco plastics behave differently.
They may flow slower.
They may shrink more.
They may need lower heat.
The Mold Maker adjusts for that.
They change gate sizes.
They tweak cooling systems.
They test and refine.
Without their work, green molding fails.
Challenges with Eco-Friendly Plastics
Eco plastics are not perfect.
They can be weak.
They can cost more.
They may not last long.
Some are not heat resistant.
Others are hard to mold.
The Mold Maker solves these problems.
They use tests and experience.
They find the right mold design.
They help balance cost and quality.
Mold Design for Green Materials
Mold design must change too.
Eco plastics need better flow.
They cool at different speeds.
They may stick to mold walls.
The Mold Maker adds coatings.
They improve mold surfaces.
They test gate placement.
They try new venting paths.
These changes make green molding work.
They cut down waste.
They boost yield.
And they save energy.
Green Manufacturing Practices
Eco-friendly plastics are just the start.
Electronic Injection Molding must go further.
Many smart factories also:
- Use electric molding machines
- Recycle scrap plastic
- Reuse water in cooling
- Use low-energy heaters
The Mold Maker can design molds for fast cycles.
That saves power.
And cuts costs.
Green doesn’t mean slow.
It means smart.
Recycled Plastic in Electronic Parts
Recycled plastic is popular now.
It’s cheaper.
And greener.
But it’s not always easy.
It may contain dirt.
It may have uneven flow.
A good Mold Maker plans for this.
They allow wider tolerances.
They test mix quality.
They build stronger molds.
Some brands use 100% recycled casings now.
And customers love it.
The Future of Green Molding
More change is coming.
Governments push for green laws.
Markets demand green choices.
Electronic Injection Molding must evolve.
Eco plastics will grow.
Better recycling will help.
Mold Makers must lead the way.
They must test new plastics.
They must design smarter molds.
And they must train others.
Soon, green will be the standard.
Not the trend.
Success Stories
Many companies already went green.
They used eco plastics.
They teamed with skilled Mold Makers.
They made parts with PLA.
They switched to bio-PE.
They used recycled ABS.
They lowered emissions.
They saved money.
And they made users happy.
What Buyers Can Do
Buyers also play a role.
They can ask for eco options.
They can choose green vendors.
They can reward clean production.
The more they ask, the more change happens.
Mold Makers and brands will follow.
Together, they create better parts.
And a better world.
How to Start Using Eco Plastics
Want to go green?
Start simple.
- Talk to your Mold Maker
- Ask what eco plastics they support.
- Learn the limits and benefits.
- Pick the right material
- PLA for low strength
- Bio-PE for toughness
- Recycled blends for cost-saving
- Test samples
- Check flow and finish
- Run life tests
- Adjust mold if needed
- Scale slowly
- Start with one product
- Monitor results
- Expand over time
Eco-friendly plastics are the future.
They help the planet.
They meet customer needs.
They make brands stronger.
Electronic Injection Molding must adapt.
It must use greener plastics.
And smarter mold designs.
The Mold Maker is key.
They know how to shape eco materials.
They design for quality and speed.
Work with a skilled Mold Maker.
Choose the right plastic.
And help build a cleaner world.