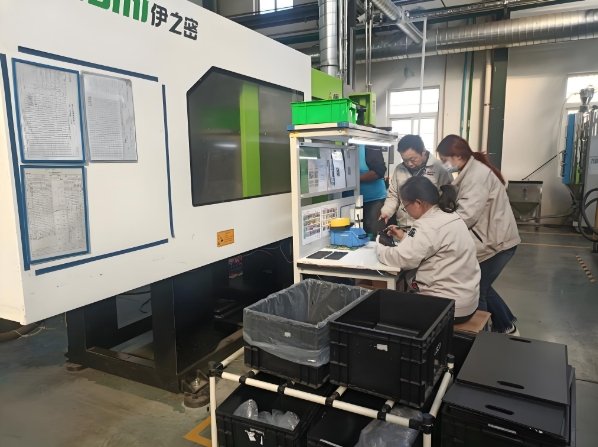
Electronic injection molding produces high-precision components for electronic devices. It ensures accuracy, durability, and efficiency. However, the process has challenges. Mold makers must overcome material selection issues, precision demands, and defect risks. This article explores common problems and their solutions.
1. The Importance of Electronic Injection Molding
1.1 Why Precision Matters
Electronic components require extreme accuracy. Even small defects can cause failure.
1.2 High-Volume Production Needs
Millions of electronic parts must be identical. Inconsistent molding leads to rejection and waste.
1.3 The Role of Mold Makers
Mold makers design high-precision molds. These molds determine the accuracy of final products.
2. Common Challenges in Electronic Injection Molding
2.1 Material Selection Issues
Electronics need heat-resistant and durable materials. Choosing the wrong plastic leads to cracks, warping, or poor conductivity.
2.2 Tight Tolerances
Electronic parts are often microscopic. Meeting tolerances within microns is difficult.
2.3 Defects in Molded Parts
Bubbles, warping, and sink marks reduce product quality. These defects result from poor molding conditions.
2.4 High Tooling Costs
Precision molds require expensive materials and machinery. Initial costs can be high.
2.5 Manufacturing Speed and Efficiency
Fast production must not compromise quality. Slow cycles increase costs, while fast cycles risk defects.
3. Solutions to Common Challenges
3.1 Choosing the Right Materials
Mold makers select high-performance plastics like:
- PEEK (for heat resistance)
- LCP (for micro components)
- ABS (for durability)
3.2 Advanced Mold Design
Computer simulations predict molding issues before production. This reduces defects.
3.3 Quality Control Systems
Automated inspection ensures precision. AI detects defects in real time.
3.4 Efficient Cooling Systems
Optimized cooling prevents warping. Uniform temperature control improves accuracy.
3.5 High-Precision Machinery
Modern injection molding machines have tighter controls. They maintain consistency at micro-levels.
4. Key Applications of Electronic Injection Molding
4.1 Circuit Board Housings
These protect delicate components. They must be precise and durable.
4.2 Micro Connectors
Tiny connectors ensure proper electrical contact. Precision is critical.
4.3 LED Components
Light-transmitting plastics require defect-free molding.
4.4 Switches and Buttons
Responsive buttons need exact molding for reliability.
5. Innovations in Electronic Injection Molding
5.1 AI-Driven Monitoring
AI detects defects and adjusts molding conditions automatically.
5.2 Smart Molds
Sensors in molds monitor temperature, pressure, and material flow.
5.3 Sustainable Materials
Eco-friendly plastics reduce waste without sacrificing performance.
5.4 3D Printing for Prototyping
3D-printed molds speed up testing and design improvements.
6. The Future of Electronic Injection Molding
6.1 Miniaturization Trends
Devices are getting smaller. Molding will meet these precision demands.
6.2 Automation in Mold Making
Robots and AI will improve speed and accuracy.
6.3 Cost-Effective Solutions
New materials and techniques will lower production costs.
Electronic injection molding faces many challenges. However, mold makers develop solutions using advanced techniques. Precision, efficiency, and quality control ensure reliable electronic components. As technology evolves, molding will continue to improve.