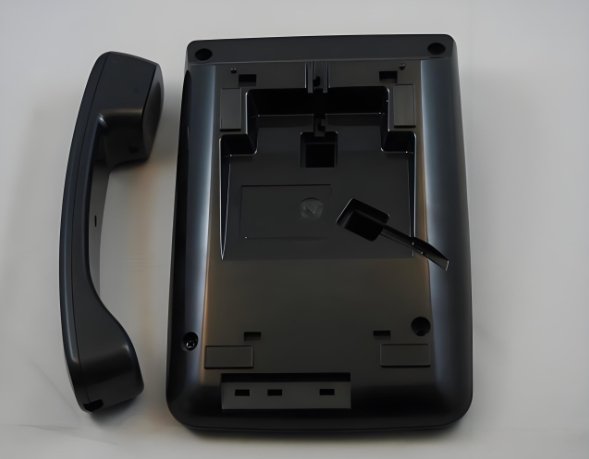
Energy is not free.
And factories use a lot of it.
Especially in Electronic Injection Molding.
Every shot.
Every cycle.
Every second matters.
Saving energy is key.
It lowers costs.
It reduces waste.
It helps the planet.
The Mold Maker plays a big part.
They design smarter molds.
They help reduce energy use.
Let’s explore how.
Why Energy Efficiency Matters
Electronic Injection Molding runs non-stop.
Machines heat.
They inject.
They cool.
Then do it all again.
This cycle burns energy.
Electricity.
Heat.
Water.
Cutting energy use saves money.
It also cuts carbon.
And builds a greener brand.
Where the Energy Goes
To save energy, we must know where it’s used.
Heating
The barrel needs heat to melt plastic.
Heaters work hard.
Injection
The screw pushes melted plastic fast.
That takes power.
Clamping
The mold must close tight.
Clamps use motors.
Cooling
Plastic cools before ejection.
Chillers and fans run.
Ejection
The part pops out.
More movement.
More energy.
The Mold Maker helps improve all of this.
The Role of the Mold Maker
A good Mold Maker makes a big difference.
They design efficient molds.
They cut down cycle times.
They make flow better.
Their design affects:
- Filling pressure
- Cooling time
- Venting
- Part ejection
Good design = less energy used.
Ways to Improve Energy Efficiency
1. Use Electric Injection Machines
All-electric machines use less power.
They run clean.
They start fast.
They waste less.
Good for precision.
Great for electronics.
2. Shorter Cycle Times
Long cycles waste energy.
Cooling takes too long.
Bad ejection slows things down.
The Mold Maker helps fix that.
With better designs.
And better materials.
3. Optimize Mold Cooling
Cooling eats the most energy.
Poor cooling means long waits.
Smart cooling saves time.
The Mold Maker adds more cooling lines.
They make sure water flows right.
They keep mold temps stable.
4. Reduce Waste
Scrap needs rework.
Or it gets dumped.
Both cost energy.
Smart gating.
Even filling.
And better part designs reduce scrap.
The Mold Maker leads this effort.
Use of Hot Runners
Hot runners help.
They keep plastic hot in the runner.
No cold scrap.
Less waste.
Less regrind.
More energy saved.
But hot runners need skill.
The Mold Maker must design them right.
Material Choice and Energy
Some plastics need more heat.
Others melt easy.
The Mold Maker suggests the best match.
They pick materials that flow well.
And cool fast.
This lowers heat needs.
And speeds up molding.
Advanced Monitoring Systems
Modern machines have sensors.
They track energy use.
In real time.
They show spikes.
And waste.
This helps improve settings.
And find leaks.
The Mold Maker works with techs.
To fine-tune each setup.
Smart Design = Less Energy
Design affects energy.
Thick parts cool slow.
Sharp corners trap heat.
Uneven walls cause defects.
The Mold Maker avoids this.
They create even walls.
Balanced flow.
And smooth ejection.
That keeps the cycle tight.
And energy low.
Automation and Robotics
Robots help save power.
They work fast.
They don’t rest.
They move parts.
They trim gates.
They pack products.
Less labor.
Less delay.
More savings.
The Mold Maker plans for automation.
They fit ejectors.
Slides.
Sensors.
Servo Motors and Drives
Older hydraulic machines use more power.
Newer servo motors save up to 70%.
They only run when needed.
They stop when not.
The Mold Maker helps adapt molds to these systems.
So energy savings increase.
Maintenance Saves Energy
Dirty molds run slow.
Worn parts overheat.
Blocked vents trap pressure.
Regular care fixes that.
The Mold Maker provides service plans.
And keeps the mold in top shape.
That protects the machine.
And reduces power use.
Energy Audits in Molding Plants
Energy checks find waste.
They show what uses the most.
And what to fix.
Audits check:
- Heating systems
- Cooling setups
- Mold design
- Material handling
The Mold Maker joins the review.
They suggest upgrades.
And apply better mold solutions.
Government and Green Standards
Some regions offer help.
Tax breaks.
Energy grants.
Factories that use green tech get rewards.
But they must prove savings.
A smart Mold Maker helps meet these rules.
With efficient mold systems.
And clean part design.
Case Study: Real Energy Savings
A factory made USB housings.
Old molds.
Long cycles.
High waste.
They called a new Mold Maker.
He redesigned the mold.
He added better cooling.
He trimmed the wall thickness.
He improved gating.
Result?
Cycle time dropped by 30%.
Energy use fell 25%.
Scrap cut in half.
All from better design.
The Future: Smart and Green
The future is smart.
And green.
Electronic Injection Molding must evolve.
So must every Mold Maker.
They must learn:
- Simulation tools
- Eco design
- IoT machine data
- Smart mold controls
They must lead.
Not follow.
Final Words
Saving energy is not just smart.
It’s vital.
For cost.
For speed.
For the planet.
Electronic Injection Molding can do it.
With help from a skilled Mold Maker.
They design better molds.
They cut cycle times.
They support green goals.
Together, they mold a better future.