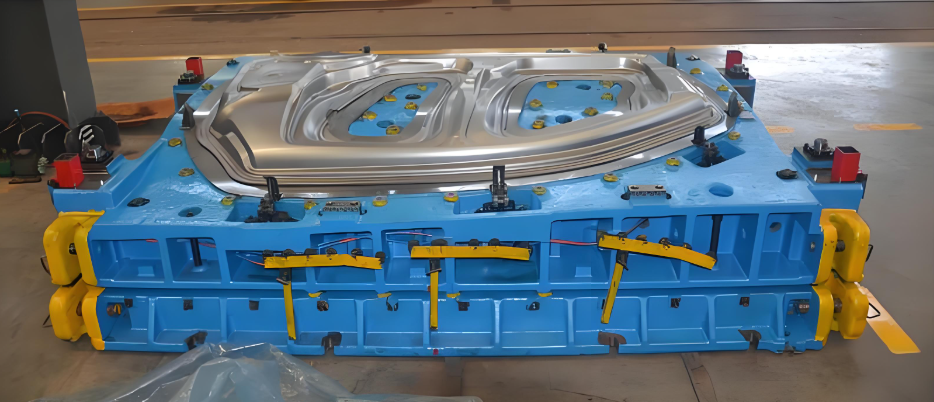
Modern vehicles require high-quality components. Custom Automotive Injection Molds provide precision and durability. A skilled Mold Maker designs molds to meet exact specifications. This ensures efficiency and reliability in manufacturing.
What Are Automotive Injection Molds?
Automotive Injection Molds shape melted plastic into vehicle parts. These molds create items like dashboards, bumpers, and air vents. A Mold Maker ensures the molds meet industry standards.
Why Custom Molds Are Essential
1. Tailored Designs
Custom molds fit specific vehicle needs. They allow complex shapes and features.
2. Consistency
Every part from a custom mold matches perfectly. This improves assembly.
3. Cost Savings
Durable molds reduce replacement and repair costs.
Components Made with Custom Molds
1. Exterior Parts
- Bumpers
- Grills
- Side mirrors
2. Interior Features
- Consoles
- Door panels
- Seat frames
3. Functional Components
- Engine covers
- Battery holders
- Air ducts
The Role of the Mold Maker
1. Design Expertise
A Mold Maker turns ideas into workable designs. Their expertise ensures proper material flow and part strength.
2. Material Knowledge
They select materials like steel or aluminum for durability.
3. Problem Solving
The Mold Maker addresses design challenges, such as thin walls or sharp angles.
Advantages of Custom Automotive Injection Molds
1. Precision
Custom molds create exact shapes and sizes.
2. Speed
Injection molding produces parts quickly, reducing lead times.
3. Durability
High-quality molds handle thousands of production cycles.
Key Steps in Developing Custom Molds
1. Understanding Requirements
Engineers collaborate with the Mold Maker to define part specifications.
2. Prototyping
Prototypes test the design before full-scale production.
3. Machining and Finishing
CNC machines carve the mold. Polishing ensures a smooth surface.
4. Testing
Every mold undergoes testing for accuracy and performance.
Challenges in Custom Mold Development
1. Complex Designs
Unique designs require innovative mold solutions.
2. Material Compatibility
Molds must accommodate different plastics.
3. High Initial Costs
Custom molds are costly but offer long-term savings.
Innovations in Custom Automotive Injection Molds
1. Lightweight Materials
Using lightweight plastics reduces vehicle weight and boosts fuel efficiency.
2. Advanced Technologies
Sensors in molds improve the injection process.
3. Sustainability
Recyclable materials and eco-friendly production methods are gaining traction.
Applications of Custom Molds
1. Luxury Vehicles
High-end cars need intricate interior and exterior designs.
2. Electric Vehicles (EVs)
Molds for EVs focus on lightweight and heat-resistant components.
3. Mass-Produced Vehicles
Custom molds ensure efficiency and consistency in large-scale production.
Benefits of Working with an Experienced Mold Maker
1. Quality Assurance
An experienced Mold Maker guarantees precision and durability.
2. Faster Development
Their expertise speeds up mold creation.
3. Long-Term Support
Good Mold Makers provide maintenance and updates for molds.
How Custom Molds Enhance Vehicle Performance
1. Improved Fit and Function
Parts fit perfectly, ensuring better vehicle performance.
2. Durable Materials
Injection-molded parts resist wear and tear.
3. Aesthetic Appeal
Custom molds enable sleek and modern designs.
Future of Custom Automotive Injection Molds
1. AI-Driven Design
Artificial intelligence will optimize mold designs.
2. Eco-Friendly Practices
Sustainability will shape future molds.
3. Personalization
Custom molds will allow more personalized vehicle components.
Custom Automotive Injection Molds are transforming the automotive industry. A skilled Mold Maker ensures every mold delivers precision and durability. These molds help create innovative and efficient vehicle components.
Choose the right partner to meet your custom mold needs. Their expertise will ensure your success in a competitive market.