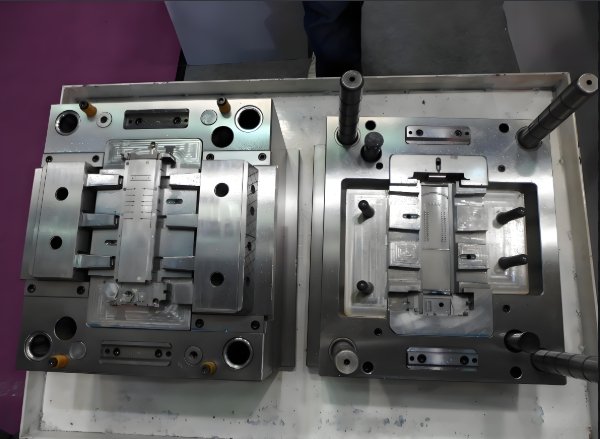
FDA compliance is essential for manufacturers in the medical device industry. For medical injection molding, meeting FDA standards ensures that products are safe and effective. Mold makers must follow strict guidelines during the production process. This article explains how to ensure FDA compliance in medical injection molding.
What is FDA Compliance?
1. The Role of the FDA
The U.S. Food and Drug Administration (FDA) regulates medical devices to ensure they meet safety and quality standards. The FDA ensures that medical devices do not harm patients and are effective in treating conditions.
2. FDA Requirements for Medical Injection Molding
For medical injection molding, FDA compliance means following standards that govern the production of medical devices. This includes ensuring the materials, processes, and final products meet FDA specifications. Mold makers must adhere to these guidelines to produce safe and reliable products.
Key FDA Regulations for Medical Injection Molding
1. FDA 21 CFR Part 820
FDA 21 CFR Part 820 outlines the quality system regulations (QSR) for medical device manufacturers. It specifies how companies should manage their production processes, design controls, and quality systems to ensure product safety. Mold makers must follow these regulations to ensure their molds produce parts that meet FDA requirements.
2. FDA 21 CFR Part 807
This regulation deals with the establishment registration and device listing for medical devices. Companies must register their facilities and list their devices with the FDA. Mold makers who are involved in manufacturing medical devices must ensure they are properly registered.
3. FDA 21 CFR Part 11
Part 11 addresses the use of electronic records and signatures. It ensures that digital documentation is secure and trustworthy. For medical injection molding, this means that all electronic records, such as quality control tests, must be maintained in a compliant manner.
4. GMP (Good Manufacturing Practices)
GMP is essential in medical injection molding. It ensures that manufacturing processes are consistent and produce products that are safe and effective. Mold makers must implement GMP in their molding processes, including regular testing and quality checks, to meet FDA compliance.
FDA Compliance Process for Mold Makers
1. Quality Management System (QMS)
A robust quality management system is a fundamental requirement for FDA compliance. Mold makers must develop a QMS that aligns with FDA regulations. This system should document every aspect of the molding process, from design to production, and ensure that the products meet safety and quality standards.
2. Documentation and Traceability
FDA compliance demands strict documentation and traceability. Mold makers need to keep detailed records of their processes, material sourcing, production methods, and inspections. This ensures that every component can be traced back to its source and that any issues can be identified and corrected quickly.
3. Process Validation
Process validation is a critical part of FDA compliance. Mold makers must prove that their injection molding process consistently produces parts that meet quality specifications. This involves documenting and validating the process under a variety of conditions to ensure consistency and reliability.
4. Regular Audits
FDA compliance requires regular audits of the production process. Mold makers must perform internal audits to identify and fix any non-conformance with FDA guidelines. Audits also help ensure that the production process remains consistent and compliant over time.
FDA Compliance Challenges for Mold Makers
1. Complexity of Regulations
FDA regulations can be complex and difficult to navigate. Mold makers must stay up to date on the latest requirements and ensure that their production processes align with these standards. This may require additional training and resources to ensure compliance.
2. Documentation Requirements
Maintaining proper documentation can be time-consuming. Mold makers must document every step of the production process, from design to quality control. This includes recording batch numbers, material specifications, and test results for each part.
3. Cost of Compliance
Achieving and maintaining FDA compliance can be costly. Mold makers may need to invest in new equipment, software for documentation, or staff training. These costs, however, are necessary to ensure the production of safe, high-quality medical devices.
4. Changes in Regulations
FDA regulations are subject to change, which means mold makers must continuously monitor and adapt to these changes. Failure to comply with new or updated guidelines can result in fines, recalls, or other legal issues.
How Mold Makers Can Ensure FDA Compliance
1. Develop a Comprehensive Quality Management System
The foundation of FDA compliance is a well-documented quality management system. Mold makers should develop a QMS that includes detailed documentation of every stage of the production process. This ensures that every part is made according to FDA standards.
2. Conduct Thorough Process Validation
Mold makers must validate their injection molding process to prove that it consistently produces parts that meet FDA specifications. This includes conducting trials under various conditions and performing tests to confirm that the parts are safe and reliable.
3. Implement Regular Quality Control Inspections
Quality control is vital for FDA compliance. Mold makers should implement regular inspections throughout the manufacturing process to ensure that parts meet required standards. Inspections should include visual checks, dimensional measurements, and material testing.
4. Train Staff on FDA Requirements
Employees involved in medical injection molding must be well-trained on FDA compliance requirements. Mold makers should provide ongoing training to ensure that staff understand the latest regulations and are aware of their responsibilities.
5. Keep Detailed Records
FDA compliance requires meticulous record-keeping. Mold makers should maintain detailed documentation of each production run, including test results, inspections, and material certifications. These records must be easily accessible for FDA audits and inspections.
6. Work with FDA-Approved Materials
To comply with FDA standards, mold makers must use FDA-approved materials for medical injection molding. These materials must be proven safe for use in medical devices. Mold makers should ensure that all materials used in production meet FDA standards.
The Benefits of FDA Compliance for Mold Makers
1. Increased Product Safety
FDA compliance ensures that the medical devices produced are safe for use. By following the required guidelines, mold makers help prevent defects, contamination, and other issues that could affect product safety.
2. Expanded Market Access
FDA certification is required to sell medical devices in the U.S. market. Mold makers who comply with FDA regulations can access a larger market and expand their business opportunities.
3. Improved Quality Control
By adhering to FDA standards, mold makers can improve their overall quality control processes. Consistent quality checks and validation ensure that every part produced meets the required specifications.
4. Reduced Risk of Recalls
FDA compliance helps minimize the risk of product recalls. If a product is not made according to FDA guidelines, it may be subject to a recall. Compliance helps ensure that the products are safe and reliable, reducing the likelihood of recalls.
5. Stronger Reputation
Being FDA-compliant gives mold makers a competitive edge. It demonstrates to customers and stakeholders that the company follows strict safety and quality standards, which enhances the company’s reputation in the industry.
FDA compliance is essential for any mold maker involved in medical injection molding. By following the FDA’s regulations and standards, mold makers can ensure the production of safe, high-quality medical devices. Compliance requires careful documentation, process validation, and regular inspections, but the benefits include better safety, expanded market access, and reduced risks. By maintaining FDA compliance, mold makers help create products that meet the highest standards of quality and safety.