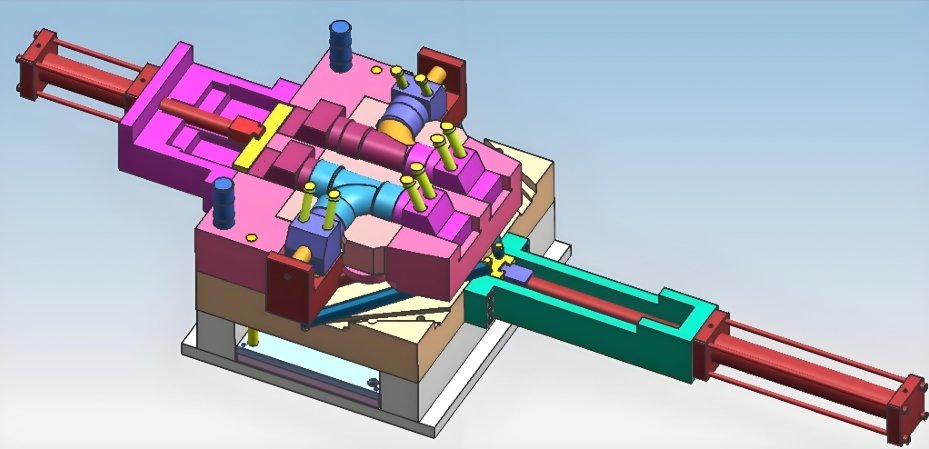
Car parts need strong materials. Automotive injection molds create durable components. A skilled mold maker selects the best materials for strength and efficiency.
Why Material Choice Matters
1. Strength and Durability
Tough materials make long-lasting parts. Automotive injection molds use strong plastics. A mold maker ensures durability.
2. Heat Resistance
Engines produce high temperatures. Automotive injection molds need heat-resistant materials. A mold maker selects the right polymers.
3. Chemical Resistance
Fuel and oil can damage weak plastics. Automotive injection molds use chemical-resistant materials. A mold maker prevents part degradation.
4. Lightweight Design
Lighter cars improve fuel efficiency. Automotive injection molds use advanced plastics. A mold maker reduces weight without losing strength.
Common Materials in Automotive Injection Molding
1. Polypropylene (PP)
PP is strong and flexible. Automotive injection molds use PP for interior parts. A mold maker ensures impact resistance.
2. Acrylonitrile Butadiene Styrene (ABS)
ABS is tough and heat-resistant. Automotive injection molds use ABS for dashboards. A mold maker improves durability.
3. Polycarbonate (PC)
PC is transparent and strong. Automotive injection molds use PC for headlights. A mold maker ensures optical clarity.
4. Nylon (PA)
Nylon resists wear and chemicals. Automotive injection molds use PA for fuel systems. A mold maker ensures long-lasting performance.
5. Polyethylene (PE)
PE resists impact and moisture. Automotive injection molds use PE for fluid containers. A mold maker ensures leak-proof designs.
6. Polyoxymethylene (POM)
POM is low-friction and tough. Automotive injection molds use POM for gears. A mold maker improves precision.
High-Performance Advanced Materials
1. Thermoplastic Polyurethane (TPU)
TPU is elastic and strong. Automotive injection molds use TPU for seals. A mold maker ensures flexibility.
2. Polyether Ether Ketone (PEEK)
PEEK withstands high temperatures. Automotive injection molds use PEEK for engine parts. A mold maker ensures heat resistance.
3. Liquid Crystal Polymer (LCP)
LCP is rigid and lightweight. Automotive injection molds use LCP for electrical components. A mold maker ensures high stability.
4. Carbon Fiber-Reinforced Plastics (CFRP)
CFRP is ultra-strong. Automotive injection molds use CFRP for structural parts. A mold maker reduces weight while increasing strength.
5. Glass-Filled Nylon
Glass fibers boost durability. Automotive injection molds use this material for under-hood parts. A mold maker ensures impact resistance.
Choosing the Right Material
1. Temperature Resistance
Engine parts need heat-resistant materials. Automotive injection molds must handle extreme heat. A mold maker selects polymers that withstand high temperatures.
2. Impact Strength
Bumpers and panels need toughness. Automotive injection molds use high-strength plastics. A mold maker ensures shock absorption.
3. Wear Resistance
Moving parts require durability. Automotive injection molds use low-friction plastics. A mold maker reduces wear.
4. Weight Reduction
Lighter cars save fuel. Automotive injection molds use advanced composites. A mold maker optimizes weight without losing strength.
Manufacturing Techniques for High-Performance Materials
1. Multi-Layer Molding
Different layers improve strength. Automotive injection molds use multi-layer designs. A mold maker ensures proper bonding.
2. Gas-Assisted Injection Molding
Gas creates hollow parts. Automotive injection molds reduce weight while keeping strength. A mold maker optimizes wall thickness.
3. Overmolding
Overmolding combines materials. Automotive injection molds improve part performance. A mold maker enhances durability.
4. High-Precision Tooling
Accurate molds improve quality. Automotive injection molds need tight tolerances. A mold maker ensures precision.
Challenges in Material Selection
1. Cost vs. Performance
High-quality materials are expensive. Automotive injection molds must balance cost and performance. A mold maker finds the best solution.
2. Processing Complexity
Some materials need special handling. Automotive injection molds require precise settings. A mold maker adjusts parameters for efficiency.
3. Environmental Regulations
Sustainability is important. Automotive injection molds use eco-friendly materials. A mold maker follows green manufacturing practices.
Future of High-Performance Automotive Injection Molds
1. Biodegradable Plastics
Eco-friendly plastics reduce waste. Automotive injection molds will use bioplastics. A mold maker focuses on sustainability.
2. Nanocomposite Materials
Nanotechnology improves strength. Automotive injection molds will use nano-enhanced plastics. A mold maker enhances material properties.
3. Smart Polymers
Smart materials respond to conditions. Automotive injection molds will feature adaptive plastics. A mold maker ensures innovation.
4. Additive Manufacturing for Molds
3D printing speeds up production. Automotive injection molds will integrate printed inserts. A mold maker reduces lead time.
Material selection is key to durability. Automotive injection molds require high-performance materials. A skilled mold maker ensures strength, precision, and efficiency. The future promises even more advanced materials for better performance.