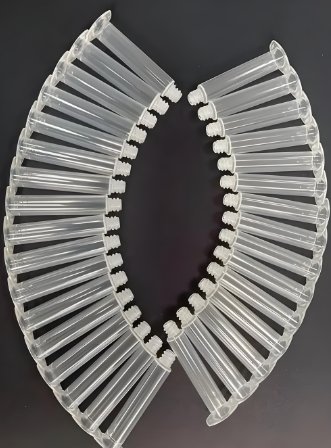
Medical devices require precision and durability. Medical injection molding ensures high-quality production. A skilled mold maker selects the best materials. High-performance polymers offer strength, heat resistance, and biocompatibility. They improve safety and functionality in medical applications.
1. Why Use High-Performance Polymers?
Superior Strength
These materials resist stress and impact. They prevent device failure.
High Heat Resistance
They withstand autoclave sterilization. Some endure temperatures above 300°C.
Chemical and Radiation Resistance
They resist harsh chemicals. They also survive gamma and EtO sterilization.
Biocompatibility
They are safe for contact with human tissues. They meet FDA and ISO 10993 standards.
Long-Term Stability
They do not degrade over time. They remain effective for years.
2. Key Properties of High-Performance Polymers
1. Mechanical Strength
Strong materials ensure device durability. A mold maker selects polymers with high impact resistance.
2. Thermal Stability
Polymers must handle sterilization heat. Some resist continuous exposure to high temperatures.
3. Chemical Resistance
Medical devices encounter disinfectants and drugs. The right plastic must not react.
4. Biocompatibility
Materials must be safe for the body. Some are suitable for implants.
5. Wear Resistance
Friction can degrade parts over time. High-performance polymers resist wear.
3. Common High-Performance Polymers for Medical Injection Molding
1. Polyether Ether Ketone (PEEK)
- Extreme strength and heat resistance.
- Withstands autoclave, gamma, and chemical sterilization.
- Used in orthopedic implants and surgical tools.
2. Polyphenylsulfone (PPSU)
- Superior impact resistance.
- Withstands repeated sterilization.
- Used in dental and surgical instruments.
3. Polyetherimide (PEI – Ultem®)
- High mechanical strength.
- Withstands high temperatures and chemicals.
- Used in sterilization trays and surgical handles.
4. Liquid Crystal Polymers (LCPs)
- High dimensional stability.
- Suitable for micro-molding applications.
- Used in electronic medical devices.
5. Polytetrafluoroethylene (PTFE – Teflon®)
- Extreme chemical resistance.
- Low friction and biocompatible.
- Used in tubing and catheters.
6. Polyarylamide (PARA)
- High strength and rigidity.
- Excellent chemical resistance.
- Used in diagnostic equipment.
4. Applications of High-Performance Polymers in Medical Injection Molding
1. Surgical Instruments
- Handles and grips require strong plastics.
- PPSU and PEI provide durability.
2. Implants and Prosthetics
- Materials must be biocompatible.
- PEEK is ideal for long-term implants.
3. Medical Device Housings
- Casings must resist impact and chemicals.
- LCPs offer precision and durability.
4. Drug Delivery Systems
- Materials must be safe for drug contact.
- PTFE resists chemical reactions.
5. Diagnostic Equipment
- Strong, lightweight plastics improve performance.
- PARA is commonly used in diagnostic tools.
5. Choosing the Right Polymer for Medical Injection Molding
Consider Sterilization Methods
Some plastics degrade under heat or radiation. A mold maker selects the best option.
Assess Chemical Exposure
Medical devices interact with drugs and disinfectants. Polymers must resist these chemicals.
Analyze Mechanical Requirements
Durability, flexibility, and impact resistance are crucial. Strong polymers ensure longevity.
Regulatory Compliance
Materials must meet FDA, ISO 10993, and USP Class VI standards. Compliance ensures safety.
6. Role of a Mold Maker in Medical Injection Molding
Material Selection
A mold maker tests and selects the best polymer for each application.
Precision Mold Design
Molds must be accurate for complex medical parts.
Process Optimization
Injection molding parameters affect material performance. A mold maker ensures quality.
Quality Control and Compliance
Medical parts must meet strict regulations. Testing ensures high standards.
7. Challenges in Using High-Performance Polymers
High Material Costs
Advanced polymers are expensive. Efficient molding reduces waste.
Processing Complexity
Some materials require precise temperature control. A skilled mold maker ensures success.
Regulatory Approval
Medical devices must pass strict tests. Compliance is time-consuming.
8. Future of High-Performance Polymers in Medical Injection Molding
1. Biodegradable Polymers
Eco-friendly options reduce medical waste.
2. Smart Polymers
Self-healing and drug-releasing plastics improve healthcare.
3. Nanotechnology Integration
Nanomaterials enhance strength and antimicrobial properties.
High-performance polymers improve medical injection molding. A skilled mold maker ensures material selection, precision, and compliance. Advanced plastics enhance safety, durability, and innovation in medical devices.