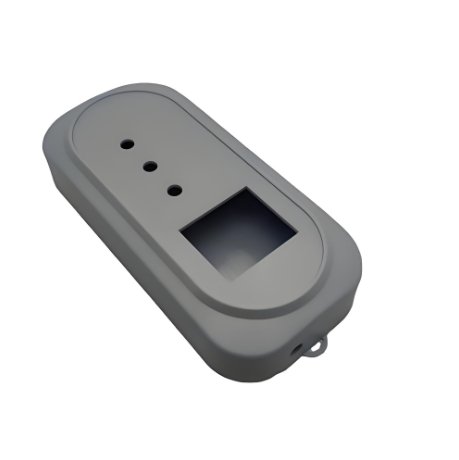
Modern home appliances rely not only on internal functionality but also on strong, attractive outer shells. These outer shells, known as plastic housings, protect the device and give it a finished look. The method that makes these housings both practical and cost-effective is Housing Injection Molding. When combined with the work of a skilled Mold Maker, this process delivers strong, smooth, and stylish plastic parts for everything from coffee machines to washing machines.
In this article, we explore how Housing Injection Molding helps create plastic housings for home appliances. We’ll also explain the key role of a Mold Maker in making the process smooth and successful.
What Is Housing Injection Molding?
Housing Injection Molding is a process that shapes molten plastic into a precise form using a metal mold. This method is widely used to produce the outer shells of home appliances. These housings need to be tough, smooth, and attractive. The injection molding process makes this possible.
Here’s how the process works in simple steps:
- Plastic pellets are heated until they melt.
- The molten plastic is injected into a steel mold under high pressure.
- The plastic cools and hardens inside the mold.
- The mold opens, and the finished plastic housing is ejected.
This method is perfect for making parts in large numbers, with each one looking exactly like the last.
Why Home Appliance Brands Use Housing Injection Molding
Many well-known brands use Housing Injection Molding to make the outer shells of their products. That’s because this method offers several key benefits:
- Speed and Volume: It allows fast production of thousands of identical parts.
- Detail and Precision: Complex designs, such as vents or logos, can be molded right into the housing.
- Surface Finish: Smooth or textured finishes can be added in the mold.
- Color Options: Pigments can be added to the plastic, removing the need for painting.
When you pick up your blender or turn on your microwave, you’re probably touching a part made by Housing Injection Molding.
The Role of the Mold Maker
A mold is the metal tool that shapes the plastic in the injection molding process. A skilled Mold Maker designs and builds this mold. This step is just as important as the molding process itself.
The Mold Maker begins with a drawing or 3D model of the housing part. They choose the right steel, cut the mold with CNC machines, and polish it to the right surface finish. Vents, gates, and cooling lines are also added to control how plastic flows and cools.
A good Mold Maker makes sure that:
- The housing comes out with the right shape every time.
- The surface is free from marks or defects.
- The mold lasts for many thousands of uses.
Without a well-made mold, the final product can have warps, uneven thickness, or a poor fit.
Common Home Appliances Using Plastic Housings
Let’s look at a few everyday items that use Housing Injection Molding:
- Coffee Makers: The outer shell and water reservoir are often made from ABS or polycarbonate using injection molding.
- Vacuum Cleaners: Strong and lightweight plastic parts protect the motor and electronics.
- Washing Machines: The control panel and lid use injection molded plastic.
- Microwaves: Buttons, front panels, and inner trays often come from injection molds.
- Toasters and Blenders: Housings need to resist heat and impacts, which plastic can handle when molded well.
Each of these uses a mold created by a Mold Maker who understands how to balance strength, cost, and appearance.
Choosing the Right Material for Appliance Housings
Not all plastics are the same. The choice of material affects how the housing looks and performs. Here are some popular plastics used in Housing Injection Molding for home appliances:
- ABS (Acrylonitrile Butadiene Styrene): Tough and glossy. Great for parts that need strength and good looks.
- Polycarbonate (PC): Very strong and clear. Ideal for lids or see-through covers.
- Polypropylene (PP): Good for parts exposed to steam or chemicals, like rice cookers.
- Nylon (PA): Used in parts that need extra wear resistance.
The Mold Maker must design the mold to fit the plastic being used. Different plastics shrink and flow in different ways, so this step is key.
Making the Process Cost-Effective
Although the mold can be expensive to build, the cost per part is very low once production starts. That’s why Housing Injection Molding is perfect for large runs of home appliance housings.
To make the process even more efficient:
- The Mold Maker uses durable materials so the mold lasts longer.
- The mold includes multiple cavities to produce more than one part per cycle.
- Automated systems eject the part and prepare the mold for the next shot.
This keeps labor costs down and speeds up production.
Quality Control in Appliance Housings
Quality control is important. Appliance housings must look clean and work well. Here’s how quality is maintained:
- Visual Checks: Parts are checked for scratches, bubbles, or flow lines.
- Fit Testing: Parts are tested to make sure they connect or screw onto other parts.
- Color Matching: The molded parts are compared to color samples to ensure consistency.
The Mold Maker and the molding technician work together to fix any problems that arise during production.
The Future of Home Appliance Housings
More appliance brands are now using eco-friendly plastics. These materials still work well in Housing Injection Molding but reduce environmental impact. Recycled plastics and biodegradable options are becoming more common.
Another growing trend is two-shot molding. This allows two different plastics (like hard and soft plastic) to be molded in one cycle. For example, a control knob might have a soft grip made right into it.
Both trends show how flexible Housing Injection Molding can be with the help of a skilled Mold Maker.
Housing Injection Molding makes it easy to produce durable, stylish plastic housings for home appliances. With the help of a trained Mold Maker, manufacturers can create molds that deliver clean, strong parts over and over again. From blenders to washing machines, many of the products in your home depend on this technology.
If you’re in the business of making home appliances, choosing Housing Injection Molding and working with a reliable Mold Maker is the smart path to consistent quality and efficient production.