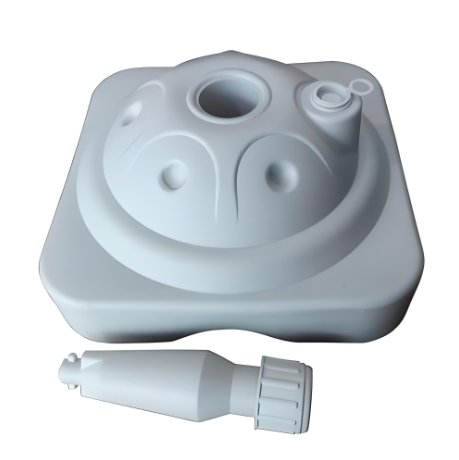
The manufacturing industry is stepping into a new era—one powered by artificial intelligence (AI). This transformation is deeply affecting many fields, including Electronic Injection Molding. For every Mold Maker, understanding the role of AI is now more important than ever. It’s no longer just about cutting steel and shaping plastic. The future is about using data, algorithms, and automation to improve quality, reduce waste, and speed up production.
This article explores how AI is revolutionizing Electronic Injection Molding and helping every Mold Maker reach new levels of precision and efficiency.
Smarter Molding Starts with Data
AI relies on data. In Electronic Injection Molding, machines now come with sensors that track temperature, pressure, cycle time, and more. These sensors collect real-time data from each production run. With AI, this information becomes a powerful tool.
AI algorithms analyze this data to spot problems before they happen. For example, if the temperature starts to drift or the injection pressure changes, AI can alert operators or even make adjustments automatically. For the Mold Maker, this means fewer defective parts and smoother operations. It also means more predictable mold wear, allowing for better maintenance planning.
Predictive Maintenance Protects Mold Investments
A Mold Maker knows how expensive and complex molds can be. Replacing or repairing a damaged mold is costly and time-consuming. AI helps protect these investments through predictive maintenance.
By monitoring equipment and mold performance over time, AI can predict when a part is likely to fail. It uses patterns from previous cycles to understand when issues will arise. Instead of waiting for a mold to break, companies can fix small issues before they turn into big problems.
In Electronic Injection Molding, this reduces downtime and ensures that production continues smoothly. The Mold Maker can also use this data to make smarter design improvements in the next version of the mold.
Faster Mold Design with AI-Powered Simulation
AI is also speeding up the mold design process. Simulation software powered by AI helps engineers and Mold Maker teams test different designs virtually before creating the actual mold. These tools can simulate how plastic will flow, where air pockets may form, and where shrinkage might occur.
This process used to take days or even weeks. Now, with AI, mold flow simulation is faster and more accurate. For Electronic Injection Molding, where tiny parts must meet strict specifications, this technology is critical. The Mold Maker can deliver high-quality molds in less time, saving money and reducing the number of trial runs.
Improved Quality Control Through Machine Learning
Machine learning is a branch of AI that helps machines “learn” from experience. In Electronic Injection Molding, machine learning tools can inspect parts automatically. Cameras and sensors scan molded parts for defects like warping, short shots, or burn marks.
The system learns what a perfect part looks like and compares each new part to that standard. If there’s a problem, it flags the part and alerts the team. Over time, the AI becomes more accurate at spotting even tiny flaws.
For the Mold Maker, this feedback is gold. It helps identify whether the problem came from the mold design or the process settings. It also supports continuous improvement.
AI-Driven Optimization of Process Parameters
In traditional Electronic Injection Molding, technicians adjust machine settings by trial and error. AI changes this. It can analyze the full set of parameters—such as melt temperature, injection speed, and cooling time—and find the ideal combination for each part.
This is especially important for electronics, where small deviations can cause big issues. AI ensures each cycle runs under the best conditions. For the Mold Maker, that means fewer customer complaints and longer-lasting molds. The AI can also suggest mold design improvements to make the process more stable.
Customization and Low-Volume Production
Today’s customers often demand custom electronic products in small batches. This trend creates challenges for traditional manufacturing methods. However, AI makes it easier to adjust settings quickly for each new batch.
With adaptive learning, the AI system remembers the best process settings for each product. When the next batch comes in, it applies the ideal parameters instantly. This reduces setup time and makes Electronic Injection Molding suitable for both large and small runs.
For the Mold Maker, this opens up new business opportunities. Designing flexible and adaptable molds becomes a competitive advantage.
Sustainability and Waste Reduction
Sustainability is now a top priority for manufacturers. AI helps reduce waste by minimizing material usage and energy consumption. It can detect issues that lead to scrap, like overpacking or flashing, and adjust machine settings to prevent them.
In Electronic Injection Molding, material waste can be expensive. AI tools make it possible to produce more parts with less plastic. The Mold Maker also benefits, as better process control reduces wear and tear on the mold.
These improvements contribute to a greener manufacturing process—something customers increasingly demand.
Digital Twins and Virtual Monitoring
Digital twins are virtual versions of physical objects. In Electronic Injection Molding, AI uses digital twins to simulate how a mold will behave under different conditions. This lets engineers test mold designs in a virtual space before real-world production begins.
These digital models can also be linked to real-time sensors. This allows the system to compare real performance against predicted behavior. If something is wrong, the AI system can make corrections on the fly.
For the Mold Maker, digital twins help reduce the number of revisions needed after the first mold trial. They also make remote collaboration easier, especially with global teams.
Training the Next Generation of Mold Makers
AI also plays a role in training. New software platforms can simulate molding scenarios and teach users how to respond. These systems give feedback and track progress. For new Mold Maker trainees, this provides hands-on learning without the cost of actual production.
As AI becomes more common, mold shops will need staff who can work with these tools. Understanding data, software, and simulation will be just as important as knowing how to use a CNC machine.
AI is not just a trend—it’s a powerful tool reshaping the entire Electronic Injection Molding industry. From faster design to better quality control, from predictive maintenance to reduced waste, AI is changing how parts are made and how molds are built.
For the Mold Maker, this transformation is full of opportunity. Embracing AI means better molds, happier customers, and more efficient operations. The role of the Mold Maker will evolve, combining traditional skills with modern data and technology expertise.
Those who adapt will lead the way. Those who resist may fall behind. The future of Electronic Injection Molding belongs to those who are ready to work smarter—with AI as their strongest ally.
Would you like a PowerPoint version of this article for presentations or training?