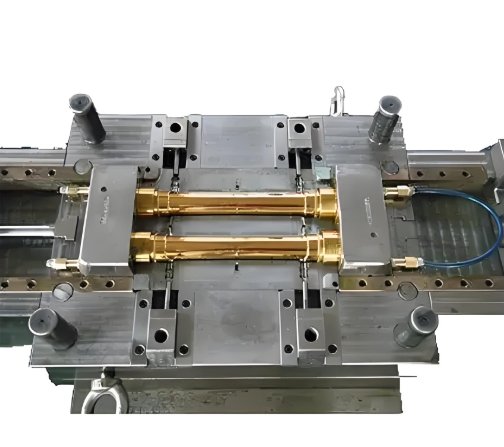
Automation is revolutionizing medical injection molding. Advanced robotics, AI, and smart systems improve precision, efficiency, and compliance. Mold makers are integrating automation to reduce costs and increase product quality. This shift ensures faster production and better consistency in medical device manufacturing.
Why Automation Matters in Medical Injection Molding
1. Enhancing Precision
Automated systems reduce human error. This ensures medical components meet strict tolerance levels.
2. Increasing Production Speed
Automation allows continuous 24/7 production. This speeds up manufacturing without compromising quality.
3. Improving Consistency
Every part produced follows the same exact specifications. This eliminates variations in medical components.
4. Reducing Costs
Automation lowers labor costs and material waste. This makes medical injection molding more cost-effective.
5. Ensuring Compliance
AI-powered monitoring ensures every part meets FDA and ISO regulations.
Types of Automation in Medical Injection Molding
1. Robotic Systems
- Handle mold loading and unloading.
- Reduce contamination by minimizing human contact.
- Improve speed and efficiency.
2. AI and Machine Learning
- Detect defects in real-time.
- Optimize molding parameters for better quality.
- Predict maintenance needs before failures occur.
3. IoT-Connected Machines
- Monitor temperature, pressure, and cycle time remotely.
- Provide instant feedback for process adjustments.
- Reduce downtime by predicting errors early.
4. Automated Quality Control
- Vision inspection systems detect microscopic defects.
- AI-powered scanners measure dimensions with high accuracy.
- Reduces reliance on manual inspections.
5. Smart Mold Maintenance
- Sensors track mold wear and tear.
- Automated alerts notify mold makers when maintenance is needed.
- Extends mold lifespan and reduces downtime.
How Automation Improves Medical Injection Molding
1. Faster Production Cycles
- Automated machines work at high speeds.
- Reduces cycle times without affecting quality.
- Enables mass production of medical devices.
2. Higher Sterility and Contamination Control
- Robots eliminate human touchpoints.
- Cleanroom-compatible automation maintains a sterile environment.
- Meets ISO 14644 cleanroom standards.
3. Real-Time Process Monitoring
- IoT sensors provide instant production data.
- AI analyzes trends to improve efficiency.
- Reduces waste and optimizes material usage.
4. Reduced Material Waste
- Automated systems ensure precise material usage.
- Less scrap and rework saves costs.
- Supports sustainability efforts in medical manufacturing.
5. Improved Traceability and Compliance
- Blockchain and digital tracking systems store production data.
- Ensures every part is traceable from raw material to final product.
- Meets FDA 21 CFR Part 820 and ISO 13485 requirements.
The Role of Mold Makers in Automation
1. Designing Smart Molds
- Mold makers create molds compatible with automated systems.
- Ensure proper cooling, flow, and ejection for efficient production.
2. Implementing Conformal Cooling Systems
- 3D-printed cooling channels reduce cycle times.
- Improves mold efficiency and part quality.
3. Enhancing Tool Durability
- Automated lubrication systems extend mold life.
- Sensors monitor wear to prevent unexpected failures.
4. Supporting AI-Driven Process Optimization
- Mold makers work with AI software to refine designs.
- Smart molds adjust to real-time feedback for better performance.
Challenges of Automation in Medical Injection Molding
1. High Initial Investment
- Advanced robotics and AI require significant upfront costs.
- Long-term savings offset the expense.
2. Skilled Workforce Requirement
- Employees need training to manage automated systems.
- AI and robotics expertise is essential.
3. Integration with Existing Systems
- Legacy equipment may need upgrades.
- New systems must align with current production lines.
4. Data Security Concerns
- IoT-connected machines require cybersecurity measures.
- Protecting patient and production data is crucial.
5. Regulatory Compliance Adjustments
- Automated processes must still meet strict medical standards.
- AI-driven decisions must be documented for regulatory approval.
Latest Innovations in Automation for Medical Injection Molding
1. AI-Powered Defect Detection
- Uses deep learning to identify defects in milliseconds.
- Reduces human error and speeds up quality checks.
2. Collaborative Robots (Cobots)
- Work alongside human operators.
- Improve safety and efficiency in cleanroom environments.
3. Predictive Maintenance Systems
- Sensors monitor mold conditions continuously.
- Prevents breakdowns before they happen.
4. Digital Twin Technology
- Creates a virtual replica of the molding process.
- Simulates improvements before applying them in production.
5. Autonomous Injection Molding Cells
- Fully automated systems from material feeding to packaging.
- Requires minimal human intervention.
Future Trends in Automation for Medical Injection Molding
1. Fully Autonomous Manufacturing Plants
- AI and robotics will manage entire production lines.
- Human intervention will be minimal.
2. 3D Printing Combined with Automation
- Hybrid manufacturing will merge medical injection molding with additive manufacturing.
- Enables faster prototyping and production.
3. Sustainable Automated Systems
- Energy-efficient robotics will lower carbon footprints.
- Smart recycling systems will reduce waste.
4. AI-Driven Customization
- Personalized medical devices will be mass-produced using smart automation.
- AI will adjust molding parameters based on real-time patient needs.
5. Enhanced Regulatory Compliance Through Automation
- Blockchain and digital record-keeping will simplify compliance.
- Automated reporting will ensure FDA and ISO adherence.
Automation is transforming medical injection molding. AI, robotics, and IoT are improving precision, reducing costs, and increasing efficiency. Mold makers are adapting by designing smarter, more durable molds. As automation advances, the industry will move toward fully autonomous manufacturing. The future of medical molding will be faster, safer, and more precise than ever.