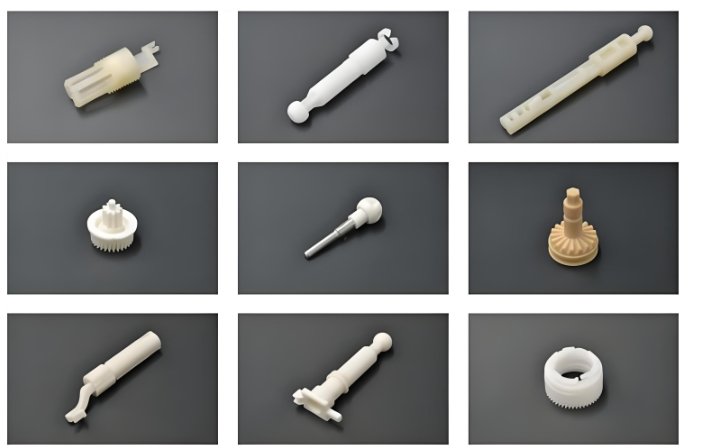
The COVID-19 pandemic changed global industries. Medical injection molding faced new challenges and opportunities. Demand for medical supplies surged. Mold makers had to adapt quickly. This article explores how the industry evolved during the pandemic.
1. The Surge in Demand for Medical Injection Molding
1.1 Increased Need for Medical Supplies
Hospitals needed more syringes, ventilator parts, and test kits. Medical injection molding played a key role in mass production.
1.2 Demand for PPE Components
Personal protective equipment (PPE) became essential. Injection-molded face shields, mask components, and respirator parts were in high demand.
1.3 Growth in Diagnostic Equipment Production
Testing for COVID-19 required new diagnostic tools. Mold makers produced millions of plastic components for testing kits.
2. Supply Chain Disruptions in Medical Injection Molding
2.1 Shortages of Raw Materials
Lockdowns disrupted global supply chains. Many manufacturers struggled to get medical-grade plastics.
2.2 Rising Costs of Resin and Other Materials
Limited supplies led to higher prices. Mold makers had to find alternative materials without compromising quality.
2.3 Delays in Shipping and Logistics
Border restrictions slowed the transportation of essential components. Companies had to plan better and find local suppliers.
3. Automation and Innovation in Response to COVID-19
3.1 Increased Use of Robotics
Companies turned to automation. Robotic arms helped maintain production while reducing human contact.
3.2 Smart Manufacturing with AI
AI improved efficiency by detecting defects and optimizing molding parameters. Medical injection molding became smarter and faster.
3.3 3D Printing for Prototyping
3D printing helped speed up mold development. Mold makers quickly adjusted designs to meet urgent needs.
4. Changes in Manufacturing Standards and Regulations
4.1 Faster FDA Approvals
Regulators sped up approval processes for essential medical products. Mold makers had to meet strict guidelines quickly.
4.2 More Stringent Cleanroom Requirements
Cleanroom manufacturing became a priority. Medical injection molding facilities improved hygiene and contamination controls.
4.3 New Quality Control Measures
Strict quality inspections ensured safety. Automated systems helped detect defects in real time.
5. Reshoring and Localization Trends
5.1 Reduced Dependence on Overseas Manufacturing
Many companies shifted production back to domestic suppliers. This reduced shipping delays and improved reliability.
5.2 Growth of Regional Mold Makers
Local mold makers gained more business. Governments encouraged domestic production for medical supplies.
5.3 Investments in Local Supply Chains
Companies invested in domestic resin production and molding facilities. This helped stabilize supply chains.
6. Long-Term Industry Changes Post-Pandemic
6.1 Continued Demand for Medical Injection Molding
Healthcare systems stockpile medical products to prepare for future crises. Mold makers continue producing at high volumes.
6.2 More Investment in Automation
Companies now prioritize automated production. AI and robotics improve efficiency and reduce labor shortages.
6.3 Stronger Focus on Sustainability
The pandemic highlighted the need for eco-friendly manufacturing. Recyclable plastics and energy-efficient machines are now a priority.
6.4 Hybrid Manufacturing Models
Companies use both medical injection molding and 3D printing. This allows flexibility in production.
COVID-19 reshaped medical injection molding. Demand skyrocketed, supply chains faced disruptions, and automation became essential. Mold makers adapted by innovating and improving efficiency. The industry continues to evolve, ensuring preparedness for future healthcare challenges.