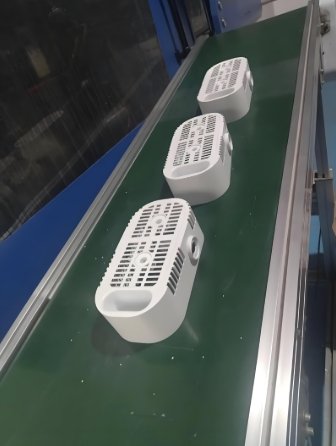
Electronic devices require precise, durable parts. Electronic injection molding is revolutionizing the industry by offering a cost-effective, efficient way to produce these parts. Mold makers play a key role in ensuring that the components meet exact specifications. This article explores how this technology is transforming the electronic manufacturing sector.
1. What Is Electronic Injection Molding?
1.1 The Basics of Injection Molding
Injection molding is a process where molten material is injected into a mold cavity. It hardens and takes the shape of the mold. This method has been used for years in many industries.
1.2 Why It’s Important for Electronics
For electronics, electronic injection molding ensures parts like casings, connectors, and circuit boards are made with precision. The technology can create parts in large quantities while maintaining high-quality standards.
1.3 The Role of Mold Makers
Mold makers design and create the molds used in the injection molding process. Their role is crucial in ensuring parts fit perfectly and function as intended.
2. Advantages of Electronic Injection Molding
2.1 High Precision
One of the main benefits of electronic injection molding is its ability to produce parts with high precision. Even the smallest tolerance issues can affect the performance of electronic devices. Molding ensures that every component meets tight specifications.
2.2 Cost-Effective Production
The process is highly cost-effective when producing large volumes. It reduces material waste and minimizes the cost of manufacturing.
2.3 Durability and Strength
Molding allows for the use of high-performance plastics. These materials are durable, heat-resistant, and able to handle the demands of electronic components.
2.4 Fast Turnaround Time
Electronic injection molding speeds up production times. This is important for industries that need products on a tight schedule.
3. Key Applications of Electronic Injection Molding
3.1 Consumer Electronics
From smartphones to laptops, electronic injection molding produces casings, buttons, and connectors. These parts are essential for both the aesthetics and functionality of devices.
3.2 Automotive Industry
The automotive industry relies on molded electronic components for safety systems, navigation systems, and more. Electronic injection molding provides the durability needed for these parts.
3.3 Telecommunications
For telecommunication equipment, electronic injection molding is used for making housings, connectors, and cables that need to withstand harsh environments.
3.4 Medical Devices
In the medical field, electronic injection molding creates precision components for wearable devices, diagnostic tools, and monitoring systems. The high accuracy ensures the reliability of life-saving devices.
4. Challenges in Electronic Injection Molding
4.1 Complex Component Designs
As electronics become smaller, components become more intricate. Mold makers must create molds that accommodate these tiny, complex designs.
4.2 Material Selection
Not all plastics are suitable for every electronic component. Mold makers must choose materials that balance strength, flexibility, and electrical properties.
4.3 Meeting Strict Standards
The electronics industry is highly regulated. Manufacturers must adhere to strict safety and quality standards, making precision in molding even more important.
5. Innovations in Electronic Injection Molding
5.1 Micro Injection Molding
Micro injection molding allows for the production of extremely small parts, which is ideal for components in wearable devices and smartphones. This innovation has opened new doors for miniaturization in electronics.
5.2 Overmolding
Overmolding combines two or more materials in one mold. This technique creates multi-material parts, such as soft-touch grips on a hard plastic case, which are common in electronics.
5.3 Insert Molding
Insert molding allows for the combination of metal and plastic in one piece. This is used in electronics to create connectors that require both strength and electrical conductivity.
6. The Role of Automation in Electronic Injection Molding
6.1 Robotics in Molding
Automation, including robotic arms, improves efficiency in electronic injection molding. Robots handle tasks like placing components into molds, reducing human error and increasing production speeds.
6.2 AI in Quality Control
Artificial intelligence is revolutionizing quality control in electronic injection molding. AI systems can inspect parts for defects in real time, ensuring that only high-quality components reach the market.
6.3 3D Printing for Molds
3D printing allows for faster prototyping of molds. Mold makers can now test designs quickly and make adjustments before full-scale production begins.
7. The Future of Electronic Injection Molding
7.1 Sustainability in Molding
As environmental concerns grow, the industry is looking for ways to use more sustainable materials. Recycling and biodegradable plastics may become common in electronic injection molding.
7.2 The Rise of Smart Factories
The future of electronic injection molding is closely linked to smart factories. These factories will use connected machines to improve efficiency, reduce waste, and enhance production quality.
7.3 Miniaturization of Electronics
As electronics continue to shrink, electronic injection molding will evolve to produce even smaller, more complex parts. This trend is likely to drive innovation in materials and design.
8. The Importance of Mold Makers in the Future of Electronic Injection Molding
8.1 Design Expertise
Mold makers will continue to play an important role in ensuring the success of electronic injection molding. Their expertise in designing and creating molds will remain crucial as electronic components become smaller and more complex.
8.2 Customization and Innovation
The future of electronic injection molding will demand even more customization. Mold makers will need to innovate to meet the unique demands of industries like healthcare, automotive, and telecommunications.
Electronic injection molding is changing the landscape of manufacturing. From consumer electronics to medical devices, this technology provides precision, efficiency, and cost savings. As industries continue to innovate, the role of mold makers will be essential in shaping the future of electronic injection molding. The advancements in materials, automation, and design will drive the next generation of electronic products.