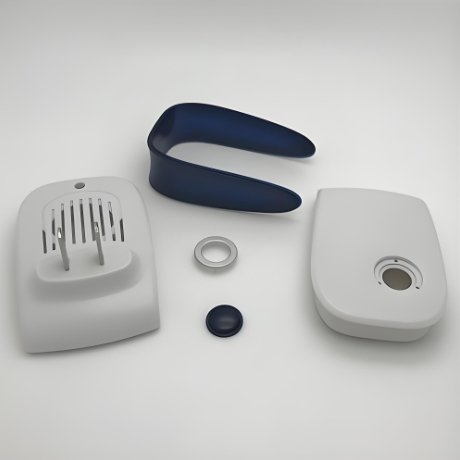
High-speed injection molding is redefining how electronic components are manufactured. It enables faster production, tighter tolerances, and reduced energy usage. For the Electronic Injection Molding sector, this technology delivers enormous value. From smartphones to automotive electronics, industries are now depending on faster cycles and more precise parts.
Every Mold Maker needs to understand this shift. As demands for smaller, more complex electronic parts grow, so does the need for speed and precision. High-speed injection molding is now a key competitive factor.
What Is High-Speed Injection Molding?
High-speed injection molding uses machines that can inject molten plastic into molds in a fraction of a second. These machines have faster cycles, often under 10 seconds, and are equipped with high-velocity injection units and powerful clamping systems.
In Electronic Injection Molding, these machines are used to make thin-wall parts, micro components, and detailed enclosures. These parts must be strong, lightweight, and consistent. A high-speed machine helps deliver that performance.
Benefits of High-Speed Injection Molding for Electronics
1. Faster Production
Speed matters in electronics. Markets move fast, and time-to-market is crucial. High-speed molding allows for rapid manufacturing of electronic housings, connectors, and circuit support structures. It means quicker prototyping and faster delivery for mass production.
A Mold Maker working with high-speed molding must adapt molds for these fast cycles. Mold cooling, gate design, and part ejection systems must be optimized to match machine speed.
2. High Precision
Electronics need parts with tight tolerances. Even small dimensional errors can cause performance issues. High-speed machines offer consistent repeatability. They reduce fluctuations in filling, pressure, and temperature.
This makes high-speed molding perfect for Electronic Injection Molding. It produces perfect parts with fewer defects. For a Mold Maker, that means less rework and fewer mold adjustments.
3. Energy Efficiency
Although high-speed machines seem more powerful, they are also energy-smart. Many use all-electric or hybrid drive systems. These save energy compared to hydraulic machines.
In a high-volume Electronic Injection Molding setup, energy savings can be significant. Less energy per part helps lower production costs and supports sustainability.
Applications in the Electronics Industry
Consumer Electronics
Phones, tablets, smart watches, and Bluetooth devices all rely on tiny, lightweight, plastic enclosures. These need thin walls and smooth finishes. High-speed injection molding can meet these demands better than traditional molding.
Automotive Electronics
Vehicles now include a large number of sensors and electronic control units. These parts must be durable, precise, and resistant to heat and vibration. High-speed molding enables cost-effective production of these parts at scale.
Medical Devices
Medical electronics like monitors, pumps, and wearable devices require precision and cleanliness. High-speed molding machines are compatible with cleanroom environments. They produce tight-tolerance parts quickly, ideal for the growing medical market.
Data and Networking
Electronic connectors, switch casings, and cable assemblies must be manufactured in high volumes. High-speed molding helps meet demand while keeping quality consistent.
How High-Speed Molding Affects the Mold Maker
1. Mold Design Challenges
Speed puts pressure on tooling. A Mold Maker must design molds that can handle rapid filling without damage or wear. This includes:
- Optimizing gate size and location
- Using high-strength steels
- Designing for fast cooling
- Ensuring fast and clean part ejection
A mistake in any of these areas could result in flash, short shots, or part warping.
2. Advanced Cooling Systems
To keep up with fast cycles, the mold needs to cool parts quickly. Cooling channels must be well-designed and balanced. Some Mold Maker teams now use conformal cooling with 3D-printed inserts to improve cooling speed and uniformity.
3. Precision Machining
Molds for high-speed machines require extreme precision. CNC machining and EDM processes must meet tight tolerances. There’s little room for error in high-speed production.
4. Material Selection
Not all resins can withstand the shear stress of high-speed molding. The Mold Maker must work closely with clients to choose materials with the right flow properties and thermal stability.
Quality Control in High-Speed Production
When parts are molded in seconds, there’s no time for manual checks. Electronic Injection Molding facilities often use inline inspection tools, like:
- Vision systems
- Pressure sensors
- Laser micrometers
These tools help catch defects early. For the Mold Maker, this means molds must be designed with access points for sensors and vision tools.
Automation Integration
High-speed molding works best with automation. Robots pick parts, inspect quality, and stack components for assembly. Automation helps keep up with machine speed and reduces labor cost.
The Mold Maker must design molds that integrate smoothly with robots. This includes ejector pin design, part orientation, and cavity layout.
Challenges in High-Speed Injection Molding
While high-speed molding offers many benefits, it also introduces risks:
- Tool wear happens faster
- Resin choices become limited
- Cycle optimization becomes complex
- Higher upfront investment is required
Still, for those focused on Electronic Injection Molding, the benefits often outweigh the challenges.
The Future of High-Speed Molding in Electronics
As electronics continue to shrink and become smarter, Electronic Injection Molding must keep up. High-speed molding will be a driving force behind this evolution.
Here’s what we can expect:
- More molders will shift to all-electric machines
- Mold Maker teams will adopt advanced simulation tools to validate mold designs
- Thin-wall molding will become more common
- AI-based process control will support real-time adjustments
Innovation in electronics requires speed and accuracy. High-speed molding delivers both.
High-speed injection molding is changing the way electronics are made. It offers faster cycles, better accuracy, and improved energy efficiency. These benefits are transforming Electronic Injection Molding into a more scalable and reliable process.
For the modern Mold Maker, this shift means rethinking how molds are designed, built, and tested. Success now depends on understanding fast-flowing materials, rapid cooling needs, and advanced automation.
The demand for compact, complex electronic parts is only going to rise. High-speed injection molding is no longer a luxury—it’s becoming a necessity. And the Mold Maker who can master this process will lead the way into the next generation of electronics manufacturing.