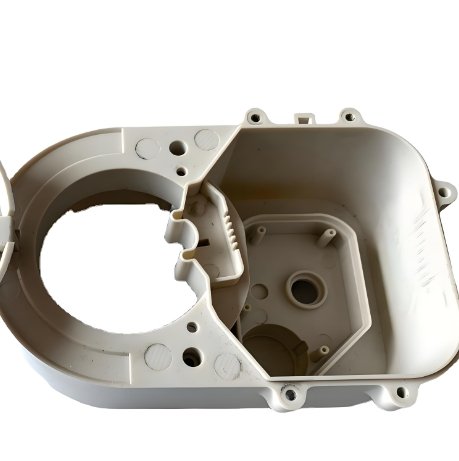
Housing Injection Molding is one of the most efficient and precise manufacturing methods for producing plastic housings. These housings are essential for protecting electronic components, mechanical systems, and various consumer products. Whether for smartphones, routers, or medical equipment, the quality of these housings matters. Behind every successful part is a skilled Mold Maker who brings the design to life with exact molds and precision.
Let’s explore how Housing Injection Molding works, step by step, and see how the role of the Mold Maker is crucial at every stage.
Step 1: Product Design
Every Housing Injection Molding project begins with a product design. Engineers and designers create a 3D model of the housing part using CAD software. This model must include all technical details like wall thickness, ribs, slots, and screw bosses.
Design for injection molding means the part should be manufacturable. It must allow for proper material flow and easy ejection. A good Mold Maker often gets involved at this early stage to help the customer fine-tune the design for the molding process.
Step 2: Mold Design
Once the part design is finalized, the Mold Maker starts designing the mold itself. The mold is the tool that shapes the molten plastic into the final housing form. It must match the 3D design perfectly, down to the smallest detail.
The mold design includes:
- Core and cavity
- Cooling channels
- Ejector pins
- Sprue and runner systems
Each feature ensures that the plastic flows smoothly and cools evenly. For complex housings with undercuts or intricate features, side actions or sliders may be added.
Step 3: Mold Fabrication
After the mold design is approved, the Mold Maker fabricates the tool. Most molds are made from steel or aluminum, chosen for durability and thermal stability.
Mold fabrication involves:
- CNC machining
- EDM (Electrical Discharge Machining)
- Polishing and surface finishing
- Heat treatment (for steel molds)
Precision is key. A slight error can ruin thousands of molded parts. That’s why the Mold Maker must be highly skilled and use advanced equipment.
Step 4: Material Selection
The next step in Housing Injection Molding is choosing the right plastic material. The housing may need to be:
- Strong
- Heat resistant
- UV stable
- Chemical resistant
- Flame retardant
Common materials include ABS, PC, PP, and blends like PC/ABS. The material must match the end-use of the product. A good Mold Maker and the molding engineer help the client select the proper resin for both quality and cost.
Step 5: Injection Molding Process
Once the mold is placed into the injection molding machine, production can begin.
The steps include:
- Clamping: The two halves of the mold (core and cavity) close tightly.
- Injection: Molten plastic is injected into the mold cavity under high pressure.
- Cooling: The part cools and solidifies inside the mold.
- Ejection: Once cooled, ejector pins push the part out of the mold.
The whole cycle can take just 10 to 60 seconds depending on the size and material of the housing.
Step 6: Post-Molding Processes
Once parts are molded, they often go through finishing steps. These can include:
- Trimming flash
- Drilling holes
- Adding threads
- Painting or printing
- Assembly with other components
The Mold Maker ensures that the mold’s finish provides the correct texture or gloss as needed, which can reduce the need for extra finishing.
Benefits of Housing Injection Molding
Housing Injection Molding offers many advantages:
- High Precision: Perfect for tight-tolerance parts.
- Speed: Ideal for high-volume production.
- Consistency: Every part is the same.
- Durability: Molds last for hundreds of thousands of cycles.
- Flexibility: Easy to switch materials and colors.
And with a skilled Mold Maker, the results are even better—more efficient cycles, less waste, and better quality control.
Role of the Mold Maker
A great Mold Maker is not just a machinist. They are an engineer, designer, and problem-solver. Their work ensures the entire Housing Injection Molding process runs smoothly. They must:
- Understand 3D part geometry
- Know material flow behavior
- Build precise mold tooling
- Maintain and repair molds regularly
Without the Mold Maker, there would be no housing, no production, and no finished product.
Applications of Housing Injection Molding
Housing Injection Molding is used in many industries:
- Electronics: Phone cases, router housings, and battery enclosures
- Automotive: Switch housings and dashboard parts
- Medical: Casings for monitors and diagnostic devices
- Consumer Goods: Remote controls, toys, and kitchen appliances
Almost every product around you has some molded plastic housing that started with a good design and an expert Mold Maker.
Challenges and Solutions
Common challenges in Housing Injection Molding:
- Warping or shrinkage
- Flow marks or burn marks
- Poor ejection or sticking
- Tool wear or failure
Solutions often lie in better mold design or material selection. That’s why the Mold Maker must work closely with the production team. Their experience helps avoid problems before production starts.
Future Trends in Housing Injection Molding
Technology continues to improve:
- Automation: Robots and sensors increase efficiency.
- Simulation Software: Detect problems before cutting steel.
- Advanced Materials: More bio-based plastics and flame-retardant grades.
- Micromolding: Producing ultra-small housing parts for compact electronics.
All these trends require a more advanced and knowledgeable Mold Maker who can adapt to new techniques and materials.
Housing Injection Molding is a powerful, efficient, and reliable method for producing high-quality housings. From design to final product, every step must be handled with care. The Mold Maker plays a central role, creating the precision tools that shape plastic into functional, attractive, and durable enclosures.
As demand grows for smarter and smaller electronic devices, the need for expert Mold Makers and advanced Housing Injection Molding techniques will only increase. Whether for small startups or global manufacturers, this process remains at the heart of modern product development.