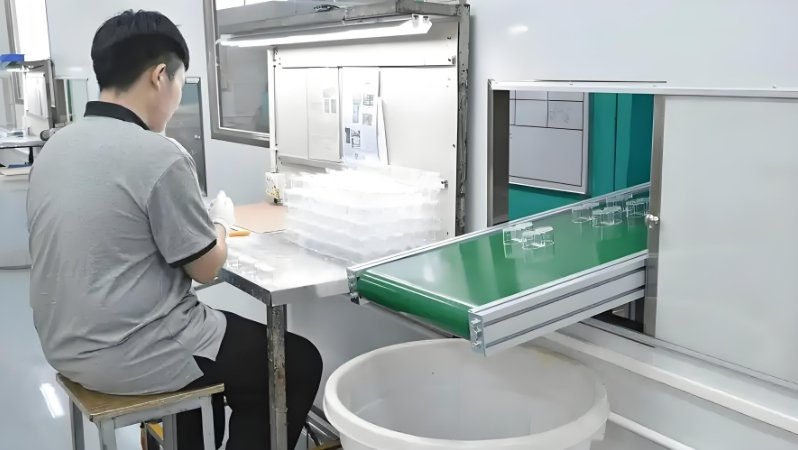
Electronic components require high precision. Electronic injection molding guarantees uniformity and quality. Small variations can affect performance. Mold makers play a key role in ensuring consistent part production.
This article explores how electronic injection molding maintains consistency in electronic parts.
1. The Need for Consistency in Electronic Components
1.1 Why Consistency Matters
- Ensures accurate electrical connections
- Prevents malfunctions and failures
- Improves product lifespan
- Reduces waste and rework
1.2 Common Challenges
- Material shrinkage
- Process variations
- Tooling wear
- Environmental factors
2. Role of Mold Makers in Consistency
2.1 High-Precision Mold Manufacturing
Mold makers use CNC machining, EDM, and laser cutting to create accurate molds.
2.2 Use of Durable Materials
High-quality steel ensures longevity and reduces dimensional changes.
2.3 Regular Mold Maintenance
Cleaning and polishing prevent defects and ensure consistent output.
2.4 Mold Cavity Inspection
Precise cavity dimensions guarantee uniform part production.
3. Key Factors in Consistent Electronic Injection Molding
3.1 Material Selection
- Stable polymers like LCP, PBT, and PPS resist shrinkage.
- Consistent resin quality improves molding accuracy.
3.2 Process Control
- Temperature, pressure, and cooling must be tightly controlled.
- Automated systems adjust settings in real time.
3.3 Injection Molding Machines
- High-precision servo-driven machines ensure repeatability.
- Advanced robotics minimize handling errors.
3.4 Quality Control Measures
- Real-time monitoring detects defects early.
- Automated vision systems check part dimensions.
4. Advanced Techniques for Improved Consistency
4.1 Scientific Molding
- Data-driven approach optimizes every molding parameter.
- Reduces variability in production.
4.2 Multi-Cavity Molds
- Produces multiple parts with identical dimensions.
- Ensures efficiency in high-volume production.
4.3 Real-Time Monitoring
- Sensors track temperature, pressure, and cooling.
- AI-driven adjustments maintain precision.
4.4 Automated Inspection Systems
- Optical and laser measuring tools verify dimensions.
- Minimizes human error.
5. Applications of Consistent Injection Molding in Electronics
5.1 PCB Connectors
- Tight tolerances ensure proper electrical contact.
5.2 Micro-Sensors
- Small parts require extreme accuracy.
5.3 Smartphone Components
- Consistent molding ensures perfect fit and function.
5.4 LED Casings
- Uniform dimensions improve heat dissipation.
5.5 Medical Electronics
- Reliable parts enhance device safety and performance.
6. Future of Consistency in Electronic Injection Molding
6.1 AI-Driven Process Control
- Predictive adjustments improve accuracy.
6.2 Smart Factories
- Automation and IoT enhance process stability.
6.3 3D Printing for Prototyping
- Validates mold designs before mass production.
6.4 Sustainable Manufacturing
- Reduces defects and material waste.
Consistency is critical in electronic injection molding. Mold makers use advanced techniques to maintain uniformity. By controlling materials, processes, and inspections, manufacturers ensure high-quality electronic components. As technology advances, automation and AI will further improve consistency in electronic injection molding.