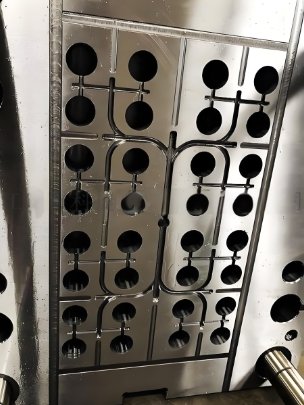
Medical injection molding has revolutionized the production of medical devices. It allows for the creation of precise, high-quality products in large volumes. Mold makers play a key role in this process. They ensure that medical devices meet strict standards and regulations. This technology has transformed how medical devices are designed, produced, and delivered to healthcare professionals and patients.
What is Medical Injection Molding?
1. The Basics of Injection Molding
Injection molding is a manufacturing process used to create parts by injecting molten material into a mold. The material cools and solidifies to form a part. In medical injection molding, the materials used must meet specific health and safety standards. These include FDA approval, biocompatibility, and the ability to withstand sterilization processes.
2. Role of a Mold Maker
A mold maker is responsible for designing and creating the mold used in the injection molding process. The mold must be precise to ensure that each part is consistent and high-quality. The mold maker ensures that the final product meets the required specifications, whether it’s for surgical tools, implants, or diagnostic devices.
Benefits of Medical Injection Molding in Device Manufacturing
1. High Precision and Accuracy
Medical devices need to be manufactured to strict tolerances. Medical injection molding offers high precision. The process allows for detailed designs, ensuring that each part is produced with exact accuracy. This is crucial for medical devices that must function reliably in sensitive healthcare environments.
2. Scalability and Efficiency
Injection molding is well-suited for large-scale production. Once a mold is designed and created, it can produce thousands or even millions of identical parts. This scalability is essential in meeting the growing demand for medical devices. Manufacturers can produce large quantities of parts quickly and efficiently.
3. Complex Geometries
Injection molding allows for the creation of complex shapes and geometries that may be difficult or impossible to achieve with other manufacturing methods. This is important for creating medical devices with intricate designs, such as surgical instruments or implantable devices.
4. Cost-Effective Production
While the initial setup cost for medical injection molding may be high, the long-term benefits make it cost-effective. The efficiency and speed of the process reduce labor costs and waste. Mass production also lowers the unit cost of each part, making it more affordable to produce medical devices at scale.
Applications of Medical Injection Molding
1. Surgical Instruments
Medical injection molding is widely used to produce surgical instruments. These instruments require high precision, as they must operate safely within the human body. Materials used in medical injection molding must be strong, biocompatible, and resistant to sterilization methods.
2. Implants and Prosthetics
Medical devices like implants and prosthetics rely heavily on injection molding. These devices often have complex shapes and require high precision. Mold makers use advanced techniques to ensure that implants fit perfectly and function properly. Injection molding allows for the mass production of these devices, making them more affordable and accessible.
3. Diagnostic Devices
Injection molding is commonly used to produce diagnostic devices such as test kits, tubes, and syringes. These devices must be manufactured to high standards to ensure accuracy and safety. Injection molding ensures that these devices are produced quickly and consistently.
4. Packaging for Medical Products
Medical injection molding is also used to create packaging for medical products. Packaging must protect sensitive medical devices from contamination and damage. Injection molding allows manufacturers to create custom packaging that meets the unique needs of medical products.
The Role of a Mold Maker in Medical Injection Molding
1. Expertise in Design and Development
A mold maker plays a critical role in the early stages of medical device manufacturing. They work closely with engineers and designers to develop molds that meet the specific requirements of the device. This includes considerations for material selection, part design, and functionality.
2. Quality Control and Testing
A mold maker ensures that the molds used in medical injection molding are of the highest quality. They test the molds to ensure that they produce parts that meet all specifications. This includes checking for defects, ensuring that the material flows properly, and verifying that the parts are the correct size and shape.
3. Ensuring Regulatory Compliance
Medical devices must meet strict regulatory standards. A mold maker must ensure that the molds and materials used in medical injection molding comply with FDA regulations, ISO standards, and other industry-specific guidelines. This is crucial to ensure that the devices are safe and effective for use in healthcare.
Challenges in Medical Injection Molding for Device Manufacturing
1. Material Selection
Choosing the right material is crucial for the success of medical injection molding. Materials must be biocompatible, durable, and resistant to sterilization methods. A mold maker must carefully select materials that meet these requirements while also ensuring that they are cost-effective and suitable for mass production.
2. Complexity of Designs
While injection molding allows for the creation of complex shapes, some designs may present challenges. Intricate features, such as thin walls, sharp corners, or deep cavities, can cause issues during the molding process. Mold makers must use advanced techniques and equipment to overcome these challenges and ensure that the final product meets the required standards.
3. Ensuring Quality at Scale
Mass production of medical devices requires consistent quality. Ensuring that each part is identical and free from defects is essential. Mold makers must use advanced quality control methods to ensure that the entire production run meets the required specifications.
The Future of Medical Injection Molding
1. Advancements in Material Science
New materials with enhanced properties are being developed for medical devices. These materials may offer better biocompatibility, durability, and resistance to sterilization. Mold makers will need to stay updated on the latest advancements in material science to continue producing high-quality medical devices.
2. Automation and Technology
Advancements in automation and technology are transforming the medical injection molding process. New machines and robotic systems are being developed to improve efficiency, reduce costs, and ensure greater precision. This will allow for even more complex designs and higher-volume production of medical devices.
3. 3D Printing and Injection Molding Integration
3D printing is becoming increasingly important in medical device manufacturing. In some cases, 3D printing may be used alongside medical injection molding to create prototypes, molds, or even final products. The integration of these two technologies will offer new possibilities for medical device design and production.
Medical injection molding has transformed the way medical devices are manufactured. It provides precision, scalability, and cost-efficiency, making it the ideal solution for producing high-quality medical devices. Mold makers play a vital role in ensuring that the molds and materials used meet the required standards and regulations. With ongoing advancements in materials and technology, the future of medical injection molding holds even more potential for improving healthcare solutions.