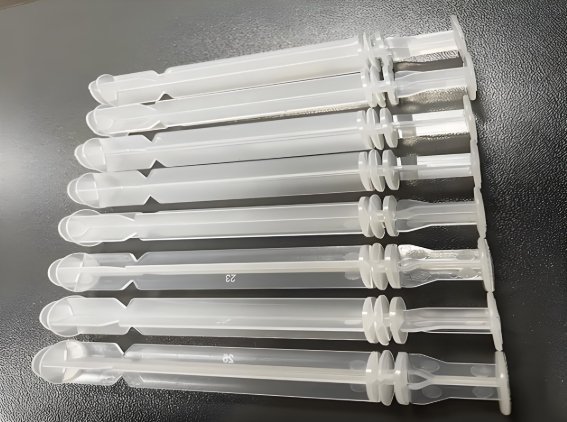
Patient safety is a top priority in medical manufacturing. Medical injection molding plays a vital role in producing safe and reliable medical devices. Mold makers ensure that each component meets strict industry standards. This article explores how medical injection molding guarantees patient safety.
Why Patient Safety Matters in Medical Injection Molding
1. Preventing Defective Medical Devices
Defective devices can cause serious health risks. Injection molding ensures precision and consistency.
2. Meeting Regulatory Requirements
Medical devices must comply with FDA and ISO standards. Compliance guarantees safety and reliability.
3. Avoiding Contamination
Medical parts must be free from bacteria and toxins. Cleanroom molding prevents contamination.
4. Ensuring Durability and Biocompatibility
Medical devices must function safely inside or outside the human body. High-quality materials improve safety.
Regulations and Standards for Patient Safety
1. FDA 21 CFR Part 820
- Sets quality system regulations for medical device manufacturers.
- Ensures products meet strict safety requirements.
2. ISO 13485
- Defines quality management for medical device production.
- Requires detailed documentation and testing.
3. ISO 14971
- Covers risk management for medical devices.
- Identifies potential failures before production.
4. ISO 10993
- Ensures that materials are biocompatible.
- Prevents toxic reactions in medical applications.
5. GMP (Good Manufacturing Practices)
- Establishes strict production standards.
- Ensures consistency, cleanliness, and safety in molding.
How Medical Injection Molding Prevents Contamination
1. Cleanroom Manufacturing
- Uses controlled environments to eliminate dust and bacteria.
- Meets ISO 14644 standards for medical-grade cleanliness.
2. Sterilizable Materials
- Medical-grade plastics resist heat and chemicals.
- Ensure safety after autoclaving, gamma radiation, or chemical sterilization.
3. Automated Production
- Reduces human contact with medical components.
- Lowers the risk of contamination.
4. Antimicrobial Additives
- Prevent bacterial growth on medical devices.
- Common in catheters, syringes, and implants.
The Role of Mold Makers in Ensuring Patient Safety
1. Precision Mold Design
- Mold makers create high-accuracy molds.
- Prevents defects and ensures exact part dimensions.
2. Material Selection
- Only FDA-approved plastics are used.
- Ensures compatibility with medical environments.
3. Regular Mold Maintenance
- Prevents defects and contamination.
- Ensures consistent product quality.
4. Process Validation
- Ensures that every batch meets safety standards.
- Includes installation, operational, and performance qualification.
Testing and Quality Control in Medical Injection Molding
1. Dimensional Accuracy Testing
- Uses laser and coordinate measuring machines (CMM).
- Ensures parts meet tight tolerances.
2. Biocompatibility Testing
- Confirms that materials are safe for human use.
- Prevents allergic reactions and toxicity.
3. Sterilization Validation
- Tests how materials respond to sterilization.
- Ensures parts remain safe after exposure to heat and chemicals.
4. Mechanical Testing
- Measures tensile strength and flexibility.
- Ensures parts withstand real-world medical conditions.
5. Leak and Seal Integrity Testing
- Confirms that IV components and drug delivery systems do not leak.
- Prevents contamination of medical fluids.
Common Challenges in Ensuring Patient Safety
1. Strict Regulatory Compliance
- Medical standards constantly evolve.
- Manufacturers must stay updated to remain compliant.
2. Material Selection Limitations
- Only specific plastics can be used.
- Must meet biocompatibility and durability requirements.
3. High Costs of Quality Control
- Advanced testing and cleanroom facilities increase costs.
- Compliance is expensive but necessary for safety.
4. Maintaining Process Consistency
- Every batch must meet identical specifications.
- Process validation prevents variations in production.
Technological Innovations for Patient Safety
1. AI-Powered Quality Control
- Detects defects in real time.
- Improves precision and reduces waste.
2. IoT-Connected Molding Machines
- Monitors production parameters continuously.
- Ensures consistency in every batch.
3. 3D Printing for Prototyping
- Speeds up mold testing.
- Allows faster validation of new medical designs.
4. Smart Materials
- Develops plastics that detect contamination.
- Improves safety in drug delivery systems.
5. Blockchain for Traceability
- Ensures secure, tamper-proof documentation.
- Enhances transparency in the medical supply chain.
Best Practices for Improving Patient Safety in Medical Injection Molding
1. Implement Strict Quality Control Measures
- Use automated inspection systems.
- Ensure every part meets safety requirements.
2. Maintain Detailed Documentation
- Record every step of production.
- Enables quick identification of defects or issues.
3. Train Employees on Compliance Standards
- Workers must understand FDA and ISO regulations.
- Ongoing training ensures best practices are followed.
4. Optimize Mold Maintenance Schedules
- Regular mold cleaning prevents contamination.
- Preventative maintenance reduces product defects.
5. Work with Certified Suppliers
- Ensure raw materials meet regulatory standards.
- Reduce risks by sourcing only FDA-approved plastics.
Future Trends in Patient Safety for Medical Injection Molding
1. Increased Automation
- Robots will further reduce human contamination risks.
- AI will enhance quality control inspections.
2. Sustainable Medical Plastics
- New biodegradable materials will improve eco-friendliness.
- Testing will ensure safety and durability.
3. Personalized Medical Devices
- Custom molding techniques will improve patient-specific care.
- Smart materials will enhance biocompatibility.
4. Advanced Cleanroom Technologies
- Improved air filtration will further reduce contamination risks.
- New sterilization methods will increase product safety.
5. Digital Compliance Monitoring
- Cloud-based regulatory tracking will streamline compliance.
- Blockchain will enhance product traceability.
Medical injection molding plays a crucial role in patient safety. Mold makers ensure precision, cleanliness, and compliance at every step. Strict regulations, advanced testing, and continuous innovation make medical devices safer than ever. By following best practices and embracing new technologies, manufacturers can further enhance patient safety in the future.