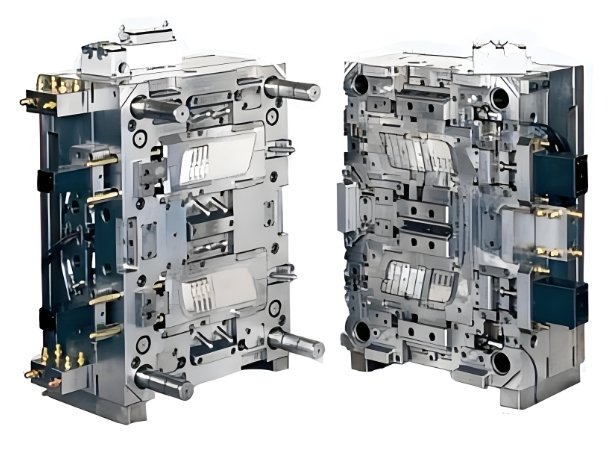
Precision is vital in healthcare. Medical injection molding creates accurate and sterile parts. A skilled mold maker ensures high-quality production. These components improve medical treatments and patient safety.
1. The Role of Medical Injection Molding
What is Medical Injection Molding?
This process forms plastic parts for healthcare. It produces consistent, sterile, and durable medical components. A mold maker designs molds for precision.
Why It Matters
- Reduces human error
- Enhances patient safety
- Ensures high-quality medical tools
2. Common Applications in Healthcare
Medical Device Components
Medical injection molding produces essential medical parts. A mold maker ensures precise dimensions.
Examples include:
- IV connectors
- Catheter parts
- Surgical handles
Drug Delivery Systems
Accurate dosing saves lives. Medical injection molding produces precise drug delivery tools.
Examples include:
- Insulin pens
- Syringe plungers
- Inhaler components
Implantable Devices
Biocompatibility is crucial. A mold maker selects safe materials for implants.
Examples include:
- Artificial joints
- Dental implants
- Pacemaker casings
3. Advanced Materials for Medical Molding
Why Material Selection is Important
Medical-grade plastics must be strong, sterile, and biocompatible. A mold maker ensures safe material use.
Common Materials
- Polycarbonate (PC) – Impact-resistant
- Polyetheretherketone (PEEK) – Biocompatible
- Polypropylene (PP) – Sterile and flexible
4. Cleanroom Manufacturing for Sterile Products
Why Cleanrooms Matter
Contamination can be dangerous. Medical injection molding happens in controlled cleanrooms. A mold maker follows strict cleanliness protocols.
Cleanroom Benefits
- Prevents bacteria buildup
- Ensures regulatory compliance
- Maintains product consistency
5. Micro-Molding for Small Medical Parts
What is Micro-Molding?
Some medical parts are tiny. Medical injection molding allows high precision. A mold maker creates molds for small-scale production.
Common Micro-Molded Parts
- Hearing aid components
- Miniature surgical tools
- Tiny catheter tips
6. Single-Use vs. Reusable Medical Components
Why Use Single-Use Medical Tools?
Hospitals rely on sterile disposables. Medical injection molding produces them efficiently. A mold maker ensures each piece is flawless.
Reusable Components
Some tools must withstand sterilization. Medical injection molding allows durability. A mold maker selects heat-resistant materials.
7. Multi-Shot Molding for Complex Designs
What is Multi-Shot Molding?
Some parts need multiple materials. Medical injection molding combines them in one step. A mold maker ensures seamless bonding.
Applications
- Soft-touch syringe grips
- Dual-layer medical tubing
- Ergonomic surgical tools
8. Regulatory Compliance in Medical Injection Molding
Why Compliance is Essential
Healthcare tools must meet strict standards. Medical injection molding follows global regulations. A mold maker ensures compliance.
Key Regulations
- FDA (U.S. Food and Drug Administration)
- ISO 13485 (Medical Device Quality Management)
- USP Class VI (Biocompatibility Standards)
9. The Role of Precision Engineering
Why Precision Matters
Medical tools need exact dimensions. Medical injection molding allows extreme accuracy. A mold maker ensures every part meets specifications.
Precision Techniques
- CAD-based mold design
- High-speed CNC machining
- Automated quality checks
10. Rapid Prototyping for Faster Development
Why Prototyping is Important
Medical devices evolve quickly. Medical injection molding enables rapid prototyping. A mold maker refines designs before mass production.
Prototyping Methods
- 3D printing
- Soft tooling
- Small-batch molding
11. Automation for High-Efficiency Production
How Automation Helps
Machines improve accuracy. Medical injection molding now uses robotic systems. A mold maker programs them for precision.
Automation Benefits
- Reduces human error
- Increases production speed
- Ensures uniform quality
12. Sustainable Medical Injection Molding
Eco-Friendly Manufacturing
Medical waste is a concern. Medical injection molding now includes sustainable plastics. A mold maker selects biodegradable materials.
Sustainable Medical Plastics
- Recycled PET
- Biodegradable polyesters
- Plant-based polymers
13. Advanced Cooling Systems for Faster Production
Why Cooling is Important
Faster cooling increases efficiency. Medical injection molding uses advanced cooling techniques. A mold maker ensures uniform temperatures.
Cooling Techniques
- Conformal cooling channels
- Copper-based inserts
- Water-assisted cooling
14. Gas-Assisted Molding for Lightweight Medical Parts
What is Gas-Assisted Molding?
Hollow parts reduce material use. Medical injection molding incorporates gas injection. A mold maker ensures even thickness.
Applications
- Lightweight prosthetic components
- Hollow syringe plungers
- Ergonomic handles
15. Hot Runner Systems for Reduced Waste
What are Hot Runners?
Cold runners waste plastic. Medical injection molding replaces them with hot runners. A mold maker optimizes material flow.
Hot Runner Benefits
- Minimizes scrap
- Speeds up cycles
- Enhances part consistency
16. The Future of Medical Injection Molding
What’s Next?
Technology keeps improving. Medical injection molding will become smarter. A mold maker will use AI-driven monitoring.
Upcoming Trends
- AI-powered quality control
- Fully automated molding lines
- Smart materials with built-in sensors
Medical injection molding enhances healthcare by ensuring precision, sterility, and efficiency. Skilled mold makers create reliable medical components, improving patient safety and medical advancements.